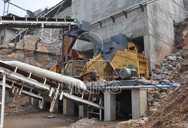
Optimization of Cement Manufacturing Process - ScienceDirect
1987.8.1 From our experience and technical knowledge accumulated through the use of Ono-method for long years, we have succeeded in developing a real-time quality
More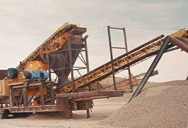
Cement plant performance optimization Benchmarking, correction
ABB’s Cement FingerPrint is a process optimization and energy consulting service designed to capture, analyze and improve operational performance and energy efficiency
More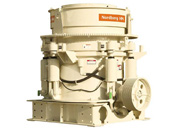
Digitization and the future of the cement plant
2020.9.16 The per-ton cement cost at such a plant is between $35 and $40. This future is not far off. Our analysis shows that pursuing
More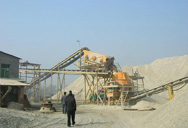
Cost-efficient strategies for sustainable cement production
Figure 1: Our technology and solutions work across the cement manufacturing process to deliver higher quality product, at lower cost, with reduced environmental impact access
More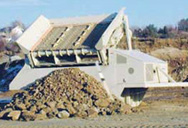
Advanced process control for the cement industry - FLSmidth
ECS/ProcessExpert® Why use advanced process control? Advanced process control from FLSmidth ensures that cement plants perform better, resulting in increased stability and
More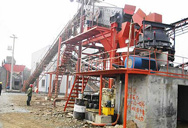
Parametric Studies of Cement Production Processes
2019.11.13 The cement industry is one of the most intensive energy consumers in the industrial sectors. The energy consumption represents 40% to 60% of production cost. Additionally, the cement industry
More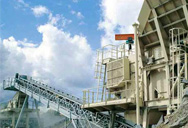
Grinding process optimization - IEEE Xplore
2017.6.19 As a world-wide leader in grinding solutions for the cement industry and understanding the changing needs of cement producers and how to tailor solutions to
More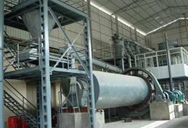
Artificial intelligence helps cut emissions and costs in
AI can help optimize energy consumption and throughput of cement kilns and mills by improving equipment productivity in view of rising environmental concerns and CO 2 costs. (PDF-520 KB) Worldwide, more than 2,200
More
A comprehensive review on Advanced Process Control of cement
2023.1.1 Thus, there is a need for optimal design and efficient operation of the cement kiln to minimise this energy loss. Changes in the kiln design demand a large
More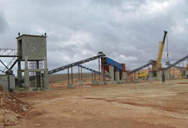
Parametric Studies of Cement Production Processes
2019.11.13 The cement industry is one of the most intensive energy consumers in the industrial sectors. The energy consumption represents 40% to 60% of production cost. Additionally, the cement industry
More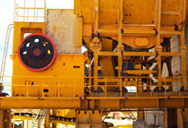
7-Ways to achieve energy saving in Cement grinding
2016.6.3 At fixed process conditions, so that the sieve 45μm cement and specific surface area of control at a reasonable level to limit 3μm 45μm particles below and above, in order to get a good cement ...
More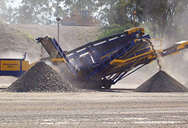
Cement plant performance optimization Benchmarking, correction
Cement FingerPrint facilitates customers to collaborate with ABB experts to achieve optimal process performance and improve cost effectiveness. Cement FingerPrint ensures tuning of plant control system efficiently, benchmarked to Industry-best practices. Further, Cement FingerPrint offers a
More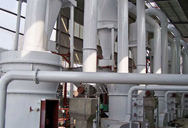
Different Possible Ways for Saving Energy in the Cement Production
5.2.2 Exhaust Gas from Preheater. The pre-heater exhaust contains a certain amount of heat. The gas has a temperature of 350 oC and a dust content of about 20-30 ton/h depending on separation efficiency of cyclone pre-heater. If the raw materials moisture content is low, only using a part of this gas for drying.
More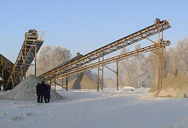
Energy-Efficient Technologies in Cement Grinding IntechOpen
2016.10.5 The energy consumption of the total grinding plant can be reduced by 20–30 % for cement clinker and 30–40 % for other raw materials. The overall grinding circuit efficiency and stability are improved. The maintenance cost of the ball mill is reduced as the lifetime of grinding media and partition grates is extended. 2.5.
More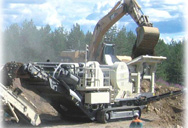
A Review on Pyroprocessing Techniques for Selected Wastes
2020.2.9 The energy efficiency of dry ball-mill grinding of cement depends on factors such as ball charge fill-ratio, mill length/diameter ratio, size distribution of the ball charge, operating conditions of the air separators, air flow through the mill, production rate, use of grinding aids, and the hardness and fineness of the feed and product (generally referred
More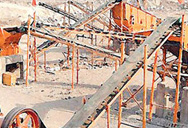
(PDF) A Survey and Analysis on Electricity Consumption
2021.1.22 In the whole process of cement production, the electricity consumption of a raw material mill accounts for about 24% of the total. Based on the statistics of the electricity consumption of the raw ...
More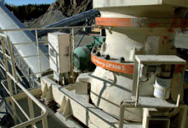
Cement mill process Download Scientific Diagram - ResearchGate
Download scientific diagram Cement mill process from publication: DEVELOPMENT OF A FUZZY EXPERT SYSTEM BASED ON PCS7 AND FUZZYCONTROL++ CEMENT MILL CONTROL The basic idea of this work was to ...
More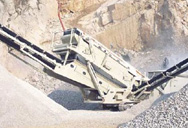
Methodological development for the optimisation of electricity cost
2021.11.10 Cement factories require large amounts of energy. 70% of the variable cost goes to energy—33% to kiln thermal energy and 37% to electrical energy. This paper represents the second stage of a broader research study which aims at optimising electricity cost in a cement factory by means of using artificial intelligence. After an analysis of the
More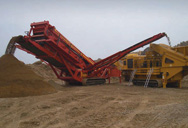
Technological Energy Efficiency Improvements in Cement Industries
2021.3.30 The cement industry is highly energy-intensive, consuming approximately 7% of global industrial energy consumption each year. Improving production technology is a good strategy to reduce the energy needs of a cement plant. The market offers a wide variety of alternative solutions; besides, the literature already provides reviews of
More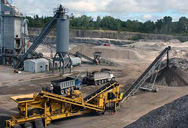
BALL MILLS Ball mill optimisation
and cement. Roller presses are used mainly in combination with a ball mill for cement grinding applications and as finished product grinding units, as well as raw ingredient grinding equipment in mineral applications. This paper will focus on the ball mill grinding process, its tools and optimisation possibilities (see Figure 1). The ball mill
More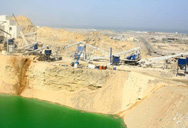
Cement Mill - Academic Accelerator
However, particle size distribution became an issue again and roll-pressing is now gaining popularity as a “pre-grinding” process for finishing cement in single-chamber ball mills. This results in good cement performance and a 20-40% reduction in energy consumption compared to standard ball mill systems.
More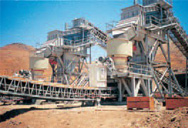
Advanced process control for the cement industry - FLSmidth
process experts designs solutions specifically for cement applications. With more than 40 years of plant automation experience, FLSmidth has installed over 700 control systems and 450 laboratory systems – and understands the needs of today’s cement plants. FLSmidth is a world leader in building and maintaining cement plants, and
More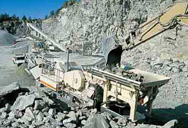
GRINDING TECHNOLOGY COURSE - The Cement Institute
2023.10.16 A 6-week modular course is designed to give the course attendee a solid understanding of the grinding system and its auxiliary equipment. The purpose of the training is to Identify and understands necessary known and unknown information towards the completed cycle of the grinding system, whether it is a ball mill, vertical mill, or
More
Demystifying Automation in Cement Manufacturing Birlasoft
2021.4.28 The cement mill (or finish mill) presents a convincing case for automation as the optimization process employed by many cement manufacturers is mainly manual. Particle fineness of the cement is measured by way of Blaine measurements, routinely carried out separately off-line. In a conventional setup, peak performance was ensured
More
Facility Layout PDF Cement Mass Production - Scribd
heat 3333 lathe mill grind - 3333 treat. 4444 mill drill gear - 4444 cut cm layout advantages • lower work-in-process inventories – reduced material handling costs – shorter flow times in production – simplified production planning (men, material etc.)
More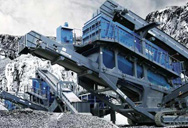
Optimize Your Process Ensure Product Quality. Improve Plant ...
the cement producer the flexibility to choose the right equipment for the right application. Among others we can supply a unique X-ray analyzer which allows two X-ray techniques—XRF and XRD—to be integrated into one instrument. This system provides both elemental analysis and analysis of specific process-related phases all on the same
More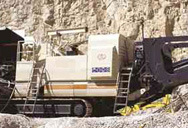
A Survey and Analysis on Electricity Consumption of Raw Material Mill ...
2021.1.22 In the whole process of cement production, the electricity consumption of a raw material mill accounts for about 24% of the total. Based on the statistics of the electricity consumption of the raw material mill system of 1005 production lines in China between 2014 and 2019, it is found that the average electricity consumption of the raw
More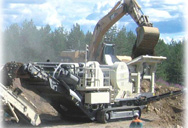
Transforming cement industry by using AI in Blaine prediction
2021.3.5 Delivering high-quality products, while keeping production costs low and plant efficiency high, is an ongoing challenge for all process industries. Traditional industries such as cement, face numerous challenges to reduce the cost of operations while maximising the yield and improving quality at the same time. With the global pandemic
More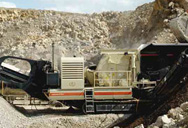
Grinding process optimization - IEEE Xplore
2017.6.19 As a world-wide leader in grinding solutions for the cement industry and understanding the changing needs of cement producers and how to tailor solutions to meet those needs. Optimizing output, improving efficiency, and reducing CO2 emissions while keeping investment costs to a minimum are common challenges that the modular
More