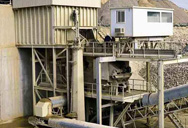
Crusher Condition Monitoring Mining, Minerals Metals
Detect Crusher Issues Early to Avoid Unplanned Downtime. Given the severity of impact absorbed by primary, secondary and tertiary crushers, it’s not uncommon for small,
More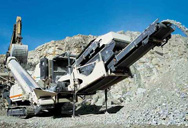
CrusherMapper Condition Monitoring - Metso
Benefit from the next generation of condition monitoring for your gyratory crushers. Metso CrusherMapper™ Condition Monitoring is a unique service that allows your metallurgists and maintenance personnel to
More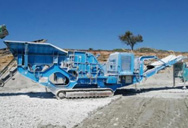
Condition monitoring of cone crushers brings huge savings - ABB
– Applicable to Sandvik cone crusher CTHS 660 and 440 models – First alarm at pressure drop – Second alarm at pressure equalization. Condition monitoring of cone crushers
More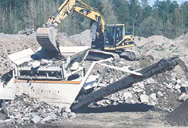
Crusher Condition Monitoring Mining, Minerals Metals
Leverage real-time crusher condition monitoring solutions to detect crusher issues early and avoid unplanned downtime.
More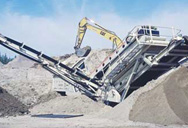
Crushermapper™TM - A new tool for crusher condition monitoring
... CrusherMapper TM for the first time provides an accurate and repeatable condition monitoring method that can be used on mantles in situ and without interruption to
More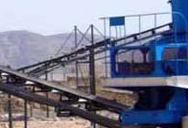
Mining
Typical applications in open pit mining are excavator gearboxes, conveyors and crushers, where very slow rotational speed and load variations make condition monitoring complicated. In underground mining, applications
More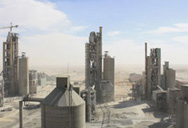
Crushers SKF
Designed to endure harsh conditions, this compact on-board, on-line condition monitoring system for predictive maintenance helps reduce unscheduled machinery
More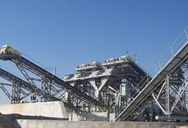
Vibration and Stress Analysis for Condition Monitoring of Symon
1990.4.1 Condition-Monitoring of the crusher frames, using stress and vibration analysis, is described. It is shown that the meshing clearances between the countershaft
More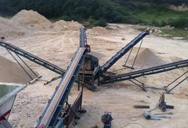
ABB Ability™ Asset Vista Condition Monitoring for cement
ABB Ability™ Asset Vista Condition Monitoring for cement. Digital application lets evaluate precise maintenance needs in cement plants by pulling together previously disparate
More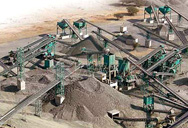
Case study: Jaw crusher monitoring with SPM HD
A Jaw Crusher Application in the Mining Industry by Tim Sundström. This case study describes the condition monitoring setup and findings on a jaw crusher (crushing ore at a normal operating speed of 181 RPM) located
More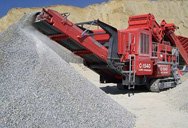
Crusher Condition Monitoring Mining, Minerals Metals
Crusher Condition Monitoring Detect Crusher Issues Early to Avoid Unplanned Downtime Given the severity of impact absorbed by primary, secondary and tertiary crushers, it’s not uncommon for small, undetected problems to rapidly accelerate to catastrophic failure, meaning extended periods of unplanned downtime.
More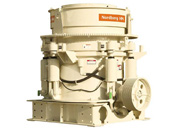
Study on Load Distribution in the Working Space of Lever Crusher
2017.9.6 This paper presents laboratory jaw crusher stand equipped with special construction measuring system which allows to determine the load distribution in crusher’s working space. ... Part of the Applied Condition Monitoring book series (ACM,volume 10) Abstract.
More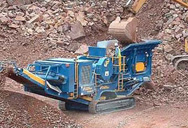
Oil Analysis — The Basics
Oil Analysis Assists Maintenance Personnel in Two Primary Ways: First — Determining the physical condition and contamination of the oil. Lubricant serviceability can be impacted by either reaching the lubricant’s life span OR contamination levels have reached a point requiring a drain and refll, unless purifcation is an option.
More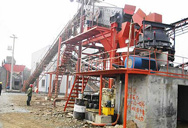
An end-to-end harmful object identification method for sizer crusher
2023.4.1 Therefore, the condition monitoring signals of the crusher are needed to identify different feeds to prevent harmful objects from entering the crushing cavity. 3.2. Time series classification. According to Ismail Fawaz et al. (2019), there are some formal definitions for TSC: Definition 1
More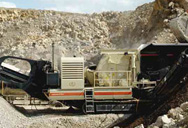
ARTO AHLSTEN CONDITION MONITORING APPLICATIONS OF CRUSHING
dition monitoring methods are tested by designing and implementing measurement setup. The measurement setup is installed on a mobile crushing unit – Metso Lokotrack LT106. The measurement setup includes measuring of machine orientation, monitoring of a frame bearing of the crusher and monitoring vibration of machine’s main conveyor. The used
More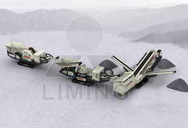
THE EFFECT OF LINER WEAR ON GYRATORY CRUSHING
2011.6.21 Despite the pressing requirement to tightly control gyratory crusher operation, no accurate, reliable, cost efficient, or practical condition monitoring tools or holistic performance assessment ...
More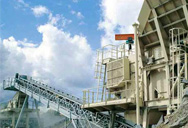
Crusher services - Metso
Predictive crusher maintenance Predictive maintenance refers to monitoring the condition of the rock crusher while it is in operation. Metso offers numerous solutions for this, including Metso Metrics and Metso CMMS. Predictive maintenance tools such as these aid in providing visibility on: Uptime and energy use
More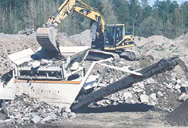
Online condition monitoring services - FLSmidth
Spot the earliest signs of parts failure, and act in a way that suits your schedule with our online condition monitoring services. Using a combination of operating data, advanced diagnostics software and our network of experts, we identify potential problems and their root causes, and develop optimal solutions so that you can prevent those problems from
More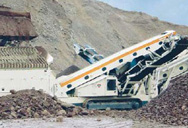
Crusher Condition Monitoring Mining, Minerals Metals
Leverage real-time crusher condition monitoring solutions to detect crusher issues early and avoid unplanned downtime. Click to view our Accessibility Policy and contact us with accessibility-related issues
More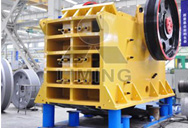
SPM HD Shock pulse monitoring - SPM Instrument
SPM HD. SPM HD® is a patented further development of the Shock Pulse Method (SPM) used for a fast, easy, and reliable diagnosis of the operating condition of rolling element bearings. It provides easy-to-understand condition evaluation in a green-yellow-red scale, as well as crystal-clear spectrums and time signals for further analysis.
More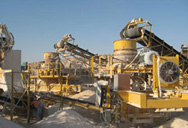
Condition monitoring of cone crushers brings huge savings - ABB
Asset Monitoring for lubrication and hydraulic unit – Condition Monitoring System integrated to Control System – Applicable to Sandvik cone crusher CTHS 660 and 440 models – First alarm at pressure drop – Second alarm at pressure equalization. Condition monitoring of cone crushers brings huge savings. SITUATION. SUCCESS. MINING ...
More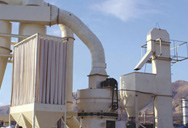
High Pressure Grinding Roll for advanced crushing
KREBS® SmartCyclone™ - Optimisation and condition monitoring solutions. Back. KREBS® Urethane Cyclones. Back. KREBS® Vessel (DeOiler) Back. REFLUX® Classifier. Back. Conveyors. Rail-Running
More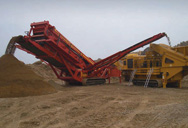
Case study: Jaw crusher monitoring with SPM HD
English (United Kingdom) 1 MB. 12/2/2014. A Jaw Crusher Application in the Mining Industry by Tim Sundström. This case study describes the condition monitoring setup and findings on a jaw crusher (crushing
More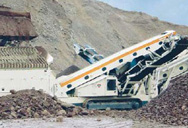
Crusher Condition Monitoring Mining, Minerals Metals
Leverage real-time crusher condition monitoring solutions to detect crusher issues early and avoid unplanned downtime. Click to view our Accessibility Policy and contact us with accessibility-related issues
More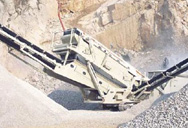
The Effect of Liner Wear on Gyratory Crushing - ResearchGate
Despite the pressing requirement to tightly control gyratory crusher operation, no accurate, reliable, cost efficient, or practical condition monitoring tools or holistic performance assessment ...
More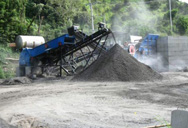
Crushers SKF
Dual-line lubrication systems. For oil, semi-fluid grease and grease up to NLGI 2. For heavy applications like pulp and paper, mining and metals. Up to 2000 lubrication points over long distances up to 120 m. Tough machines need tough solutions. SKF solutions for crushers ensure reliable uptime even in the most intense operating conditions.
More
Compressor monitoring and control - Turbomachinery Magazine
2020.4.17 By Tim Shea. Compressor monitoring and controls are critical for optimizing the performance of compressors widely used across the oil gas, refining, chemical and petrochemical industries. Economic drivers include the growing demand for energy, improving compressor efficiency and increasing production of compressor
More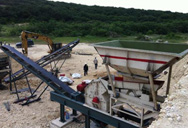
Failure rate analysis of Jaw Crusher: a case study Sādhanā
2019.1.2 Failure of crusher components has considerable influence on the productivity of a crushing plant. In order to improve performance and operational reliability, its critical components are needed to be identified to make replacement in time before any catastrophic failure happens. Though traditional maintenance practices exist in crushing
More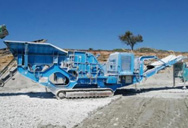
ROXON HX170 Belt Condition Monitoring - YouTube
2022.7.1 ROXON's HX170 is the ideal system for monitoring the wear and damage of belts in light-duty conveyors, reducing costs related to production loss and belt sto...
More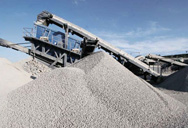
Condition-Based Monitoring for a Construction Aggregate
2019.9.12 BB-SG30000525-42. Advantech provided a Condition-Based Monitoring (CBM) sensor system for a constructions aggregate plan so it could continually monitor motors in real time, apply data analytics to detect changes in motor behavior, and alert maintenance staff anywhere they happened to be.
More