
Copper Mining and Processing: Processing Copper
2020.7.13 The copper concentrate is first sent through the smelting furnace to be heated up to 2,300 °F and converted into molten liquid.
More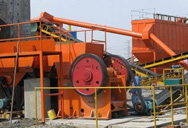
Copper Concentrates - Cargo Handbook - the world's
Copper is processed in several stages from extraction and crushing of the ore to electrolytic refining, which allows obtaining 99.99% pure Copper
More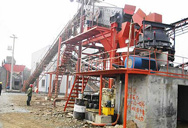
Processing of Complex Materials in the Copper
2020.7.6 Pyrometallurgical processing of complex copper concentrates has been traditionally associated with the smelting of
More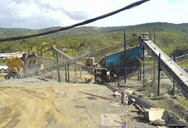
Copper Concentrate - an overview ScienceDirect Topics
Copper Concentrate. Typically, copper concentrates contain 20–30% Cu and up to 5% Zn. Copper flotation tailings are activated with copper sulfate and zinc minerals floated
More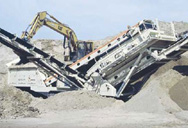
Pressure leaching of copper concentrates at Morenci, Arizona – 10 ...
Copper was recovered through the existing and subsequently by electrowinning (EW) in an expanded tankhouse at the site. An acid cost credit was provided to the concentrate
More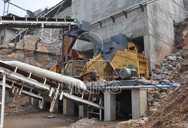
Your Process Challenge for Copper - Heraeus
In the pyro-metallurgical process route, raw mined ore is first upgraded to copper concentrate by means of crushing and flotation enrichment processes. This
More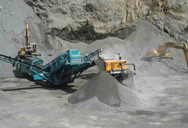
Current Status of Copper-Ore Processing: A Review
The amount of copper in copper sand-stones and slates varies from 1 to 6%, in sulfide cop-per-nickel ores from 1.1 to 4.9%, in copper-pyrite ores from 0.1 to 3%, and in copper
More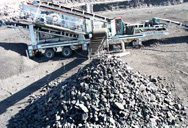
Cu–Ni processing improvements at First Quantum’s Kevitsa mine
2016.3.15 Installation of a column cell in the Cu circuit has improved copper recovery to copper concentrate by 1.5% at 99% level of confidence. The concentrate grade has
More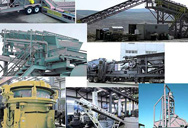
Grind Optimization of Konkola Blended Copper Ore
2020.8.1 Konkola West Concentrator stockpile handles 55000 tonnes copper ore per day producing an average of 400 tonnes of concentrate. The grade of the concentrate is 36 to 40% TCu. The plant efficiency
More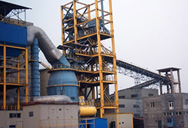
Current Status of Copper-Ore Processing: A Review
2021.9.8 Abstract An analysis of flowsheets for processing sulfide and oxide copper ores, reagent modes, processing equipment, and flotation indicators in some domestic and foreign processing plants and productions is carried out. Autogenous and semiautogenous mills are commonly used in the primary grinding stage in ore processing plants, which
More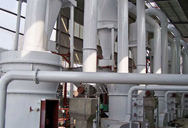
Extraction of cobalt ore by crushing and dressing technology
2022.12.29 When the preferential flotation process is used to treat copper-cobalt ore, it is generally used to preferentially flotation copper and then flotation cobalt. By using lime as inhibitor, YK1-11 as copper collector and butyl xanthoxanthate as cobalt collector, copper concentrate and cobalt sulfur concentrate can be obtained respectively.
More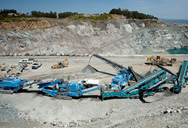
Copper Ore Processing Methods - 911 Metallurgist
2017.4.11 The four major steps in the production of marketable copper are mining, concentrating, smelting, and refining. In a few instances, however, leaching takes the place of concentrating, smelting, and refining. At present, although considerable leaching and direct-smelting ores are produced, the bulk of the copper ore mined is concentrated.
More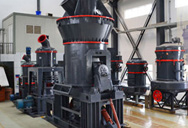
Enhancing the flotation recovery of copper minerals in smelter
2020.1.1 One of the results obtained after flotation and used to calculate recovery had concentrate and tailings grades of 31.6 and 0.38 % Cu, respectively. The concentrate and tailings weights were 12.4 and 337 g, respectively. This gave mass of copper in concentrate of 3.92 g and in the tailings, it was 1.28 g, to give a Cu recovery of 75.4%.
More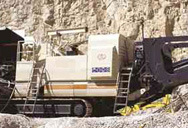
Copper Ore Beneficiation Processing Technology - JXSC Mineral
2022.12.30 Crushing and screening → grinding and grading → priority flotation of copper concentrate. Since many copper ores are associated with many other metal substances, copper ore flotation methods are divided into three types. Priority flotation When the copper ore contains two or more valuable minerals and is beneficiated by the
More
The Ore Grade and Depth Influence on Copper Energy Inputs
2016.11.22 with extraction energy usage \(E\) in MJ per kg concentrate copper based on the depth D of mining and ore grade \(G\) in percentage of copper per mass of ore. The parameter \(\gamma\) now captures the joint effects of both depth and ore grade differences per mine. The equations can be used for total energy inputs or to assert the
More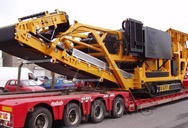
Optimizing the Rougher Flotation Process of Copper Ore
2019.2.22 In the conditioner, the collectors, foamers, and pH modifiers are mixed well. The rougher stage produces a final concentrate of 26% copper. Final relave with a law of 0.13% copper and final concentrate of the mill with a 16% copper grade. The tail of the rougher cells feeds the scavenger cells (see Fig. 2).
More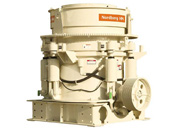
Current Status of Copper-Ore Processing: A Review
The rougher bulk concentrate contains 4% copper with 75% recovery. After recleaning, the final copper con-centrate produced contains at least 20% copper with 85% recovery. The plant within the Tominskii MPE produces 28 million t of porphyry copper ore per year, where the initial content of copper in the ores is 0.4%.
More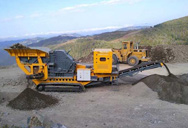
Copper Ore - an overview ScienceDirect Topics
Copper ore usually contains about 0.5 to 2% copper that occurs in the form of disseminated and stringers. The run of mine ore is reduced from 150 mm to 25 mm size in Jaw and Cone crushers. The crushed ore is grinded in ball mills to −74 μm size. The ore is processed by froth flotation comprising rougher and scavenger cells.
More
Copper Concentrates - Cargo Handbook - the world's
The production of concentrates implies the crushing and later milling of the ore down to a particle size allows releasing copper by flotation. The concentrates from different regions have approximately between 24%
More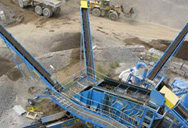
Behavior of copper and lead during mineralurgical and ...
2021.2.13 There are only a few smelters processing copper concentrates directly into blister copper. Despite the many advantages of this process, a serious challenge of this technology is the need to process the resulting flash smelting slag. It contains 12–15% copper and 2.5–4% lead. In this form, it cannot be considered as waste material and,
More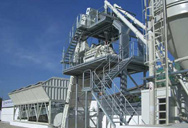
Copper Ore Crushing, Grinding Flotation - 911 Metallurgist
2017.5.21 Grinding and Flotation. Fine ore at minus 19mm (¾”) sizing is fed at a controlled rate into the open-circuit 2600mm x 3960mm (8’-6 x 13’-0) Hardinge rod mill at an average feed rate of 2,106 STPD or 87.75 STRH. Rod mill discharge at a nominal size of minus 16 mesh and a pulp density of 75 percent solids combines with ball mill discharge ...
More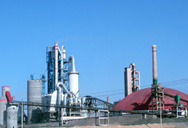
Copper extraction - Wikipedia
Copper concentrates produced by mines are sold to smelters and refiners who treat the ore and refine the copper and charge for this service via treatment charges (TCs) and refining charges (RCs). The TCs are charged in US$ per tonne of concentrate treated and RCs are charged in cents per pound treated, denominated in US dollars, with benchmark
More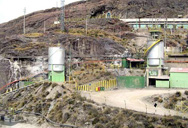
How to Process Copper Ore: Beneficiation Methods and Equipment
2023.3.13 Copper ore beneficiation methods. Before the beneficiation of copper ores, crushing and grinding are required. The bulk ores are crushed to about 12cm by a jaw crusher or a cone crusher. Then the crushed materials are sent to the grinding equipment, and the final particle size of the copper ore is reduced to 0.15-0.2mm.
More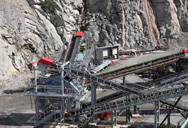
COPPER Copper production - TU Delft
Generally, copper extraction follows the sequence (see Figure below): 1. Beneficiation by froth flotation of ore to give copper concentrate (Optional partial roasting to obtain oxidized material or calcines) 2. Two-stage pyrometallurgical extraction 1. smelting concentrates to matte 2. converting matte by oxidation to crude (converter or ...
More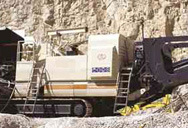
Extraction of Copper: Detailed Process - The Chemistry Notes
2023.4.4 Copper is extracted from its ore by a series of procedures, including mining, crushing, heating, chemically isolating impurities, refining, and purifying. Creating useful items from raw resources like copper ore requires a lengthy process but is possible with careful preparation and attention to detail.
More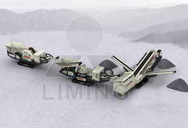
Production flow – Business overview – Nornickel 2022 Annual Report
Talnakh Concentrator processes high-grade, cuprous and disseminated ores from the Oktyabrskoye and Talnakhskoye deposits to produce nickel-pyrrhotite and copper concentrates, as well as metal-bearing products. Its key processing stages include crushing, milling, flotation, and thickening. In 2022, Talnakh Concentrator increased its
More
Comparison of environmental performance of modern copper
2021.12.1 In this work, three different concentrates with various copper grades were used to simulate different concentrate types available in the market. For each concentrate, three different capacity scenarios, namely 0.8, 1.2 and 1.6 million tonnes per annum were calculated to evaluate capacity influence without considering possible mechanical
More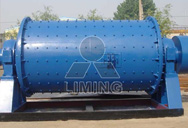
Copper Geoscience Australia
2023.9.7 Copper is soft but tough. It is easily mixed with other metals to form alloys such as bronze and brass. Bronze is an alloy of tin and copper and brass is an alloy of zinc and copper. Copper and brass are easily recycled¿perhaps 70% of the copper now in use has been recycled at least once. The Properties of Copper.
More