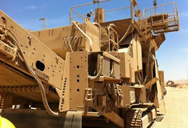
Coke (fuel) - Wikipedia
Coke is a grey, hard, and porous coal-based fuel with a high carbon content and few impurities, made by heating coal or oil in the absence of air—a destructive distillation process. It is an important industrial product, used mainly in iron ore smelting, but also as a fuel in stoves and forges when air pollution is a concern. The unqualified term "coke" usually refers to the product derived from low-as
More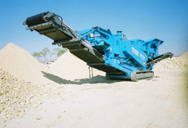
12.2 Coke Production
control the rate of coke falling onto a conveyor belt, which carries the coke to a crushing and screening system. The coke is then crushed and screened to the proper size for the
More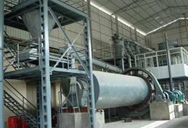
Coke Plant Technologies - ThyssenKrupp
Our Business Unit Process Technologies supplies chemical plants, refineries and coking plants on the basis of tried-and-tested technologies made by Uhde, while the portfolio of
More
coke crushing plant - LinkedIn
2023.5.19 Here is a general overview of the process: Primary Crushing: The larger coke pieces obtained from the coke production process are initially crushed in a
More
Industrial perspective of the cokemaking technologies
2019.1.1 The quality of coke depends on factors such as properties of coal/coal blend, granulometry of charged coal/coal blend, methods of coal preparation (i.e.,
More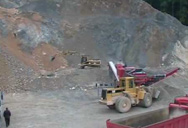
Effects and impacts of components of coal handling system on
like selective crushing of coal types and moisture/density-control devices. Key Words coal handling and preparation system for coke oven plants, selective coal crushing, bulk
More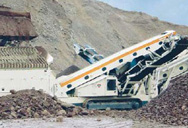
The FMC Coke Process - Springer
The FMC Coke Process. new, continuous method for the production of high-grade, preformed metallurgical coke from a wide range of coking and non-coking coals. This
More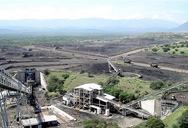
Effect of Coal Size on Coking Pressure and Coke Strength
coke-making process. Focusing on the fine crushing of coal to achieve them, we investigated the reduction of the coking pressure by a selective fine crushing of high
More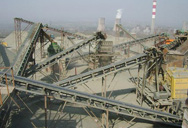
coking plant - ArcelorMittal in Belgium
This process is referred to as ‘dry distillation’. It takes about 18 hours to convert 35 tonnes of coal into 25 tonnes of metallurgical coke. The coke cake is unloaded from the oven by a pusher machine, which is equipped
More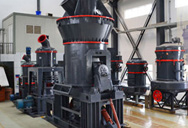
Petroleum Coke Calcining Systems - Metso
Petroleum coke calcining is a three step process, including drying, devolatization and densification. The coke calcining process is a time-temperature function, conducted in an oxygen deficient atmosphere.
More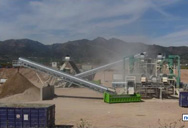
Lecture 32: Coke production - National Institute of Technology,
Process flow sheet: Illustrated in Figure. Figure 32.1 Flow sheet of coking of coal 32.3 Functional role of each unit (Figure 32.1): ... Coke breeze (or fines) is generated while crushing of coke. (f) Condenser: The foul main is cooled by indirect heat transfer with water for condensation of tar.
More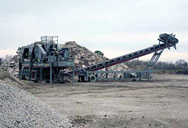
Intelligent Optimization and Control of Coking Process
2019.11.14 3.5.3 Results of Actual Runs for Intelligent Optimization and Control of Coke-Oven Combustion Process. The temperature of the coke-oven in the iron and steel company was controlled manually before the intelligent integrated optimization and control system was installed in 2005. Some results of actual runs are shown in Figs. 3.16 and 3.17.
More
Sintering plant at a glance PPT - SlideShare
2014.10.27 Sintering plant at a glance - Download as a PDF or view online for free. ... Blast furnace process-Drain rate vs cating rate pdf 29 07 2020 by Anil Mistry. ... COKE CRUSHING BY FOUR ROLL CRUSHERS 8 ( 08 Nos. CAPACITY – 16 T/Hr. EACH ) ...
More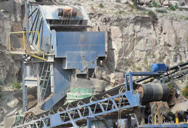
Project Report on calcined petroleum coke Manufacturing Plant,
Detailed Project Report (DPR) includes Present Market Position and Expected Future Demand, Technology, Manufacturing Process, Investment Opportunity, Plant Economics and Project Financials. comprehensive analysis from industry covering detailed reporting and evaluates the position of the industry by providing insights to the SWOT analysis of
More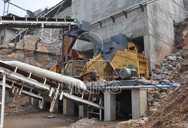
Influence of Particle Shape and Porosity on the Bulk Density
2020.1.28 The impact of VBD test parameters on measured values has been well covered in other publications (For example see the papers in the session “Petroleum Coke VBD in Light Metals 2011 []) and will not be discussed further here.Previous work in the current project [1, 2] investigated the coke property/Bulk Density relationships in Eq.. ()
More
Study of Coal Cake Bulk Density and Its Shear Strength for Stamp ...
2022.3.21 2.4 Bulk Density and Stamping Energy Measurement (Plant Scale). 30 days bulk density measurement trial was carried out at coke plant unit (Battery 11) of Tata Steel (Jamshedpur) in order to report the fluctuation of charging coal cake bulk density under different combination of moisture, crushing fineness (–3.15 mm size fractions) and
More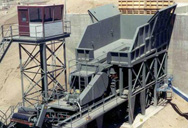
Chemical Technology Prof. Indra D. Mall Department of Chemical ...
In the lecture 2, we will be discussing about the coal carbonization, the process that has been used in coke oven plant and the in detail about the coke oven plant. How the coke is ... Coke sorting plant crushing and sorting of coke to suitable sizes for use in the blast furnace. The steps involved are coking, coke pushing, coke quenching coke ...
More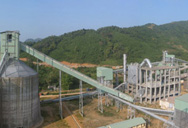
Effects and impacts of components of coal handling system on coke ...
Figure 4: Coke quality in relation to bulk density [2] Coal crushing The different grain size distribution of the raw coal is cause by the different structural strength, methods of mining and processing. This effects the requirements for the coal handling system of the coke oven plant. The main equipment for this process is the crusher station.
More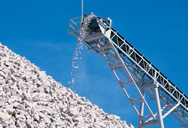
Effect of Coal Size on Coking Pressure and Coke Strength
2.1.2 Fine crushing of high-coking pressure coal at commercial coke-making plant Based on the findings in the laboratory test, we decreased push-ing loads in testing the fine crushing of high-coking pressure coal at the Kimitsu coke-making plant using a few oven chambers. The ra-Fig. 1 Reactor tube of plastic coal permeability test
More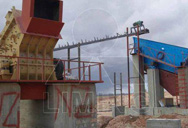
Effects and impacts of components of coal handling system on coke
Figure 4: Coke quality in relation to bulk density [2] Coal crushing The different grain size distribution of the raw coal is cause by the different structural strength, methods of mining and processing. This effects the requirements for the coal handling system of the coke oven plant. The main equipment for this process is the crusher station.
More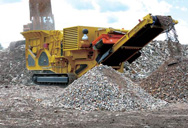
Coke Plant Technologies - ThyssenKrupp
Coke Plant Technologies Pioneering coke plant technologies are part of our daily business. The effi ciency and environmental performance of our plants are renowned worldwide. Tailor made complete coke oven plants from a single source – that’s our commitment and your advantage gained from a partnership with us. 500 coking plants
More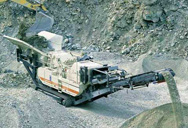
Effect of Binders on the Crushing Strength of Ferro-Coke - MDPI
2021.2.10 Ferro-coke, as a new burden of blast furnace (BF), can not only greatly reduce the energy consumption and CO2 emission, but also promote the resource utilization by using the low-quality iron ore and low-grade coal. However, the strength of ferro-coke decreased with the increasing amount of iron ore powder. In order to maintain the
More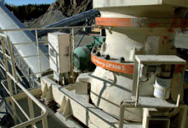
Development of a Novel Shaft Dryer for Coal-Based Green Needle Coke ...
2019.8.12 Needle coke, as an important carbon material, can be classified into two types, i.e., petroleum-based needle coke [] with heavy oil as the raw materials, and coal-based needle coke [] with coal tar, coal pitch, or their fractions as the raw materials.Initially, petroleum-based needle coke occupies the dominant position, while the production of
More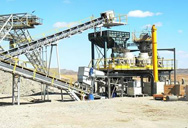
Sinter Plant Presentation (Sinter Operation) - [PDF Document]
2015.10.13 2) Fuel (coke breeze) crushing is done for obtaining required crushing index (90%) and can be used in sintering process. 3) To meet the production and process requirement, coke discharged from Double Roll Crusher 900 Dia. X 900mm is fed to 3 nos. of Four Roll Crusher to ensure that minimum 85% of 3 0 mm fraction in crushed coke
More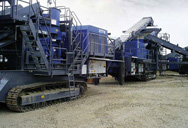
11.21 Phosphate Rock Processing - US EPA
11.21.1 Process Description1-5. The separation of phosphate rock from impurities and nonphosphate materials for use in fertilizer manufacture consists of beneficiation, drying or calcining at some operations, and grinding. The Standard Industrial Classification (SIC) code for phosphate rock processing is 1475.
More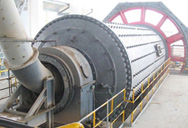
What is Blast Furnace Slag and How to Process It?
2022.2.26 In the production process, a drum with a diameter of 1m, a length of 2M and a speed of about 300 revolutions per minute is installed in front of the furnace to disperse the slag for about 20m. ... How much a rock crushing plant? 300t, 500t, 800t, 1000tph . What are the concrete crushers? and price . How much is the 50tph glass
More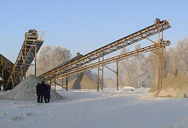
Petroleum coke processing plant Mining Quarry Plant
2013.7.18 In August 2005, the Chalmette plant was under 4-5 feet of water in the Hurricane Katrina disaster. Covered green coke storage for 25,000 tons of raw material.
More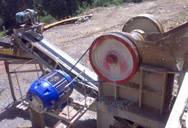
Coke (fuel) - Wikipedia
Raw coke. Coke is a grey, hard, and porous coal-based fuel with a high carbon content and few impurities, made by heating coal or oil in the absence of air—a destructive distillation process. It is an important industrial product, used mainly in iron ore smelting, but also as a fuel in stoves and forges when air pollution is a concern.. The unqualified term "coke"
More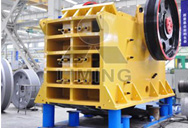
Japanese firms look to plant-based, carbon-neutral 'biocoke' fuel
2022.6.19 Oitomi usually consumes about 20 metric tons of coal coke annually. The workshop signed on to the biocoke experiment with Japan's legal pledge to go carbon neutral -- reaching zero net greenhouse ...
More