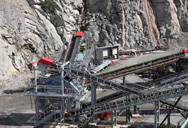
Ball mill for cement grinding - FLSmidth
The best ball mills enable you to achieve the desired fineness quickly and efficiently, with minimum energy expenditure and low maintenance. With more than 4000 references
More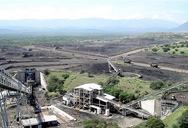
ball mill - thyssenkrupp Polysius
The proven classical option for cement grinding. Whether employed as a two-compartment separator mill in an independent grinding system, or in combination with a high
More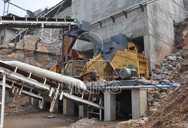
Ball mill - Wikipedia
A ball mill, a type of grinder, is a cylindrical device used in grinding (or mixing) materials like ores, chemicals, ceramic raw materials and paints. Ball mills rotate around a horizontal axis, partially filled with the material to be ground plus the grinding medium. Different materials are used as media, including ceramic balls, flint pebbles, and stainless steel balls. An internal cascading effect reduces the
More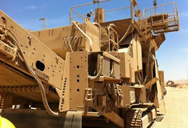
Grinding in Ball Mills: Modeling and Process Control
2012.6.1 PDF The paper presents an overview of the current methodology and practice in modeling and control of the grinding
More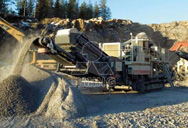
Ball mill Superior cement quality, More fl exibility, higher
way around. This table shows the range of FLSmidth ball mills for cement grinding, with capacities up to ~10 000 kW in an array of mill diameters and lengths. FLSmidth MAAG
More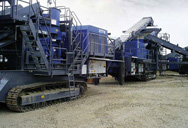
Optimization of Cement Grinding Operation in Ball
Cement ball mills typically have two grinding chambers. The first chamber is filled with larger diameter grinding media and lined with lifting liners. The first chamber coarse-grinds the feed material and prepares it for the
More
Cement mill - Wikipedia
A cement mill (or finish mill in North American usage) is the equipment used to grind the hard, nodular clinker from the cement kiln into the fine grey powder that is cement.
More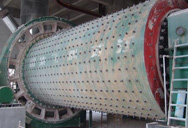
OPTIMIZATION OF CEMENT GRINDING OPERATION IN BALL MILLS
Cement ball mills typically have two grinding chambers. The first chamber is filled with larger diameter grinding media and lined with lifting liners. The first chamber coarse
More
Energy-Efficient Technologies in Cement Grinding
2016.10.5 The comminution efficiency of a HPGR is better than ball mills such that it consumes 30–50 % of the specific energy as compared to a ball mill. Four circuit configurations of HPGR can be used in grinding
More
Energy-Efficient Technologies in Cement Grinding
2016.10.5 The energy consumption of the total grinding plant can be reduced by 20–30 % for cement clinker and 30–40 % for other raw materials. The overall grinding circuit efficiency and stability are
More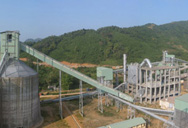
Ball Mill - an overview ScienceDirect Topics
Mechanical Crushing and Grinding. Oleg D. Neikov, in Handbook of Non-Ferrous Metal Powders, 2009 Tumbling Ball Mills. Tumbling ball mills or ball mills are most widely used in both wet and dry systems, in batch and continuous operations, and on a small and large scale.. Grinding elements in ball mills travel at different velocities. Therefore, collision
More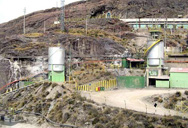
BALL MILLS Ball mill optimisation
Ball mills and grinding tools Cement ball mills are typically two-chamber mills (Figure 2), where the first chamber has larger media with lifting liners installed, providing the coarse grinding stage, whereas, in the second chamber, medium and fine grinding is carried out with smaller media and classifying liners.
More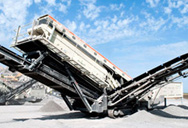
Ball Mill for Cement Grinding Process - cementmillequipment
Cement Ball Mill Structure. When Ball Mill is working, raw material enters the mill cylinder through the hollow shaft of the feed. The inside of the cylinder is filled with grinding media of various diameters (steel balls, steel segments, etc.); when the cylinder rotates around the horizontal axis at a certain speed, Under the action of centrifugal force and friction force,
More
OPTIMIZATION OF CEMENT GRINDING OPERATION IN BALL MILLS
Operation and Elements of a Closed-Circuit Ball Mill System . Cement ball mills typically have two grinding chambers. The first chamber is filled with larger diameter grinding media andlined with lifting liners . The first chamber coarse-grinds the feed material and prepares it for the second chamber. The second chamber is the fine grinding ...
More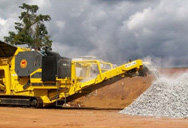
EVERY COMPONENT OF BALL MILL DETAILED EXPLAINED
1.Axial/radial runout. 2.Alignment of the drive trains. 3.Uneven power splitting. 4.Centre distances variable. 5.Face load distribution. 6.Sealing of the girth gear. 7.Girth gear is through hardened only, fatigue strength is limited. -Dynamic behaviour. -A lot of individual rotating masses risk of resonance vicinities.
More
Ball mill Superior cement quality, More fl exibility, higher
Ball mill with Central Drive Mill length Mil l diame te r M il l di amet er 5 3 2 3 2 1 3 5 6 6 4 4 Ball mill with Sid e Driv 1 Inlet 2 Outlet casing 3 Slide shoe bearing 4 Main gearbox 5 Mill motor 6 Auxiliary drive 1 3 Ball mill for cement grinding 3 Cement grinding – taking on the tough tasks Cement ball mills have to achieve the desired ...
More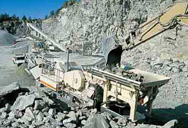
Grinding in Ball Mills: Modeling and Process Control
2012.6.1 A ball mill is a type of grinder widely utilized in the process of mechanochemical catalytic degradation. It consists of one or more rotating cylinders partially filled with grinding balls (made ...
More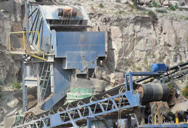
Cement Ball Mill Cost Effective Cement Grinding Mill from
AGICO cement ball mills have a wide range of models, with a maximum output of 130 tons per hour, which can meet the production needs of large, medium, and small cement manufacturers. Based on the grinding system used by customers, we can customize and optimize the ball mill. Whether it is an open-circuit grinding system, a closed-circuit ...
More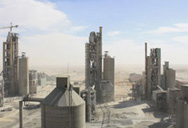
Ball Mill For Cement Grinding – Cement Ball Mill Ball Mill ...
Cement ball mill is a kind of important cement equipment in the process of raw material preparation and finished product grinding in cement plants. It is mainly used to grind limestone, clay, and other cement raw materials, as well as calcined clinker. As we all know, in the whole process of cement manufacturing, the power consumption of ...
More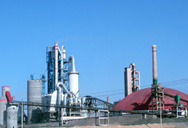
polysius® booster mill
Bead mill working principle for dry cement grinding. One crucial characteristic of this mill is the high energy density, 10-20 times higher than of a ball mill, and the resulting very compact design. The bead-stirring elements on the shaft inside the fixed shell reach a tip speed of 5 times the critical speed.
More
Christian Pfeiffer cement industry Christian Pfeiffer
Hallett Construction Materials assigns Christian Pfeiffer with a sustainable ball mill grinding circuit for its Green Cement Manufacturing plant located in Port Augusta, South Australia. Projects. ... Mill considerations when grinding finer cement. Most mill circuits are presently not designed to produce fine cements effectively.
More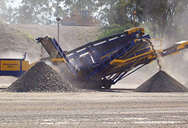
Cement grinding Vertical roller mills versus ball mills
For a ball mill grinding OPC to a fineness of 3200 to 3600 cm2/g (Blaine) the cost of wear parts (ball, liners and mill internals) is typically 0.15-0.20 EUR per ton of cement. For an OK mill grinding a similar product, the cost of wear parts depends on the maintenance procedures, i.e. whether hardfacing is applied.
More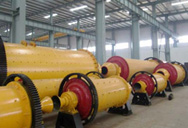
What Are the Parts of a Cement Mills? - Cement Ball Mill
2023.8.23 After exiting the cement kiln, the clinker is cooled and stored. To produce cement, clinker is mixed with a small amount of gypsum and other additives, such as pozzolans or slag. This mixture is then ground in the cement ball mill. The grinding process involves passing the clinker and additives through the rotating drum of the ball
More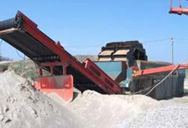
Predictive Controller Design for a Cement Ball Mill Grinding
The annual cement consumption in the world is around 1.7 billion tonnes and is increasing by 1% every year [].Cement industries consume 5% of the total industrial energy utilised in the world [].A total of 40% of the total energy consumption of a cement plant is used in clinker grinding in a ball mill to produce the final cement product []. ...
More
Ball Mill SpringerLink
2023.4.30 Ball mill is a type of grinding equipment that uses the rotary cylinder to bring the grinding medium and materials to a certain height and make them squeeze, impact, and grind and peel each other to grind materials. Ball mill is the key equipment for crushing materials after they are crushed. It is widely used in cement, silicate products,
More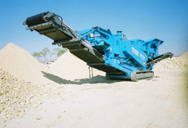
How to choose proper grinding media for your ball mill
2021.2.24 Steel balls are one of the most widely used grinding media in cement ball mills, their diameters can range from 20mm to 120mm according to different grinding requirements. In a cement ball mill, generally, φ50–100mm steel balls are used in the coarse grinding chamber, φ20–50mm steel balls are used in the fine grinding chamber. 2.
More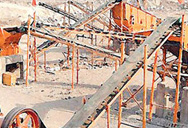
Everything you need to know about clinker/cement Grinding
Ball Mill. Cement Lafarge max R5% >25mm, Holcim 30mm; Raw Meal max R1% > 30 mm (Lafarge). ... For instance, in large diameter ball mills, the impact force of the grinding media is so great, that a high material surface unbalance prevails in the mill when grinding all types of clinker, ...
More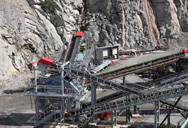
(PDF) Open and Closed Circuit Dry Grinding of Cement Mill
2004.1.14 Within the content of this work, sampling campaigns were organized around a cement grinding circuit and varying cement ball mill speed as well as an air classifier speed at various dosage feed rate.
More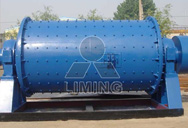
Cement Grinding Mill Ball Mill, Vertical Cement Mill, Cement
2023.8.25 Cement grinding mill play vital role in cement grinding plant, including cement ball mill, vertical mill, cement roller press, AGICO CEMENT supply all types cement grinding mill with competitive price, Ask now! Skip to content +86 13683722138. info@cement-plants. about.
More