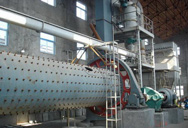
Coal crusher, Coal crushing plant - All industrial manufacturers
stationary coal fine. Contact. Capacity: 5 t/h - 80 t/h. Motor power: 7.5 kW - 132 kW. Hammer crusher is mainly used for crushing medium hardness and brittle materials, such as coal, cement, plaster, alum, brick, tile, limestone. Compressive strength of material
More
Coal Crusher Hammers United Conveyor Corporation - UCC
2023.9.14 Coal Crusher Hammers. The UCC Environmental Coal Crusher Hammer is designed for primary or secondary reduction of materials including coal, limestone, gypsum, and cement. This hammer incorporates UCC hard-facing technology
More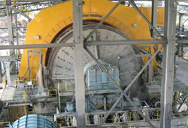
6 Types of Coal Crusher: Which Is Best for Crushing My Coal?
2023.10.8 5. Hammer crusher The hammer crushers are the choice of most coal plants because they can handle medium to bituminous coals of varying hardness. A single hammermill crusher can break coal into shape at one time, integrating coarse and
More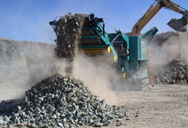
Coal Crusher, Coal Crushing Machine, Coal Crusher
Applied Coal Crusher. Since the compression strength of coal is about 5-50, general crusher is able to deal like jaw crusher, impact crusher and roll crusher, etc. However, there exist special requirements for processing
More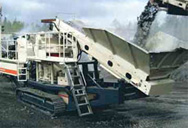
Coal Crusher Hammer, Peening Tool for DN100, Chain for DIP
Panja Industries is a leading manufacturer of Coal Crusher Hammer, Peening Tool for DN100, Chain for DIP. We manufacturer our product as per drawing and specification.
More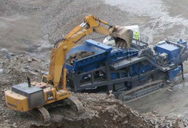
Coal Beneficiation Technology for Coking Non-Coking Coal
The benefits of low ash coal burning in boilers are realized but reimbursement of extra cost of beneficiation for washed non-coking coal needs to be considered. Key Words: Coking Coal, Middlings, Rejects, Deshaling, Coal Washing, Steel Plant, Power Houses.
More
Steelmaking: The Coke Oven By-Product Plant - accci
2021.7.22 The coke oven by-product plant is an integral part of the by-product cokemaking process. In the process of converting coal into coke using the by-product coke oven, the volatile matter in the coal is vaporized and driven off. This volatile matter leaves the coke oven chambers as hot, raw coke oven gas. After leaving the coke oven
More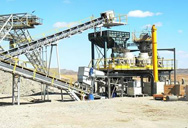
Effects and impacts of components of coal handling system on coke ...
for the coal handling system of the coke oven plant. The main equipment for this process is the crusher station. Normally it is equipped with hammer mills. After the feed material enters into the crusher, the coal is hit by the hammer heads and crushed by im-pact against the grinding wall. A further crushing
More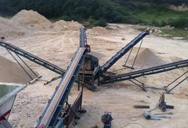
FOR E N - py
4.1 Coverage of Coke oven plant under the Purview of Notification ..... 4-1 4.2 Screening ... NGO Non-Government Organizations ... OECD Organization for Economic Co-operation and Development PBCC Partial Briquetting of Coal Charge PDU Process Development Unit PLD Percent Leaking Doors PLL Percent Leaking Lids
More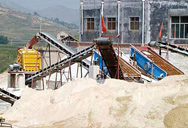
Application of Improved Quality Abrasion Resistant Materials in Hammer
2016.5.2 In an integrated steel plant coal and coke preparation units demand application of high performance hammers in coal crushing units to maintain high coal crushing index and heavy duty screen decks for maximizing yield of sized coke (25-80 mm fraction). These components work under severe wear due to the combined effects of
More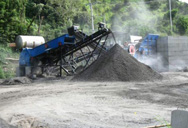
Effect of Grinding Behavior on Liberation of Coal Macerals - J-STAGE
In Tata Steel, coke plant received washed coal of size −13 mm from washeries. Typically, these coals are mixed in different proportion and crushed in the hammer mill. The size of the coal blend is maintained below 3 mm. After crushing the coal blend is charged in the coke oven for carbonization. Carbonization is basically heating of coal in ...
More
Safety Guideline for Coke Ovens - Ministry of Steel
Wagon tipplers, crushers (hammer/ roll crusher), conveyors, bins/ silos, screens, stackers cum reclaimers, Ovens machines like charging cars, pusher car, coke guide car ... COKE OVEN 1) Coal Handling Plant Hand getting pressed during coupling decoupling of wagons Use scotch block below wagon wheel. Ensure proper communication.
More
Compacting of coals in cokemaking - ScienceDirect
2019.1.1 11.1. Introduction. The aim of the coal compacting in cokemaking is to increase the bulk density of coal to be charged in coke ovens up to a relative material density of about 80%, i.e., a compact density around 1100 kg/m 3 (dry basis) depending on the true density of the coal. In stamp charge cokemaking operation, the coal blend is
More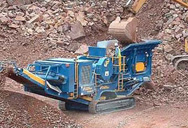
hammer crusher - Crushing, Screening Conveying
An energy-based swing hammer mill model has been developed for coke oven feed preparation. It comprises a mechanistic power model to determine the dynamic internal recirculation and a perfect mixing mill model with a dual-classification function to mimic the operations of crusher and screen.
More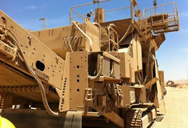
Utilization of steel plant waste and by-products in reactive coke
2023.1.4 In the present work, briquetting technique was used for producing briquettes having non-coking coal up to 40%, and rest is slightly coking coal along with reactive materials and binders. Those ...
More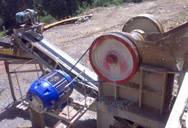
Coke (fuel) - Wikipedia
Raw coke. Coke is a grey, hard, and porous coal-based fuel with a high carbon content and few impurities, made by heating coal or oil in the absence of air—a destructive distillation process. It is an important industrial product, used mainly in iron ore smelting, but also as a fuel in stoves and forges when air pollution is a concern.. The unqualified term "coke"
More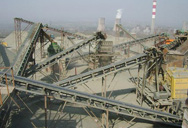
6 Types of Coal Crusher: Which Is Best for Crushing My Coal?
2023.10.8 The selection of coal crushing equipment mainly depends on the input size of raw coal, the moisture of the coal, and the production scale (output) of the plant. Of course, the output size and the final use of coal also need to be considered, such as 0-25 mm for gas furnaces, 8-25 mm for steam locomotives, 6-25 mm for industrial furnaces,
More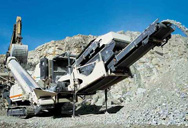
Coke Making: Most Efficient Technologies for Greenhouse Emissions ...
2019.7.19 The blending with low-quality coal is 15% maximum in the wet system, and it arrives to 30% in the dry configuration. By converting coke ovens (50 t/h capacity) from wet to dry, a reduction of over 130,000 t/year of CO 2 can be reached; this corresponds to 8% of net reduction of CO 2 emissions in the atmosphere.
More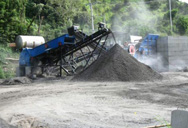
Single Stage Crusher - Made-in-China
Single-Stage Heavy Type Hammer Crusher Cement Plant Crusher 150-5000 Ton Per Hour High Capacity Crusher Instead of Jaw Crusher Cone Crusher Impact Crusher. US$ 26000-30000 / Piece. 1 Piece (MOQ) ... Two Stage Shale Crusher Single-stage Coal Coke Hammer Crusher Single Machine Crusher Machine Double Single Single Screw Single
More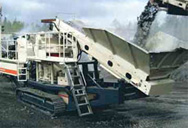
Crusher - an overview ScienceDirect Topics
Mechanical Crushing and Grinding. Oleg D. Neikov, in Handbook of Non-Ferrous Metal Powders, 2009 Crushers. Crushers are widely used as a primary stage to produce the particulate product finer than about 50–100 mm in size. They are classified as jaw, gyratory and cone crushers based on compression, cutter mill based on shear and hammer
More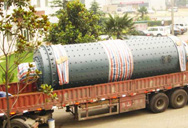
Construction, Working and Maintenance of Crushers for Crushing
Operating the crusher with a completely filled crushing chamber. Choking Stoppage of the flow of material through the crusher, which is usually due to the wet and sticky material clogging exit points. Circulating Load The amount of oversize material returned back to the crusher from a screen in a closed circuit crushing system.
More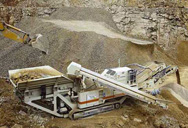
coal hammer crusher for non coke oven plant
fineness vs mill capacity xrp 883 bowl.Coal Hammer Crusher For Non Coke Oven Plant. Hammermill Crushers Gilson Co. Holmes Hammermill Coal Crushers are available in a small unit for 2in (51mm) or smaller samples of coal and coke classifying and conveying together the Hammer mill used in coke oven plant for crushing the coal. 21-04-2021.
More
(PDF) Non-Recovery/Heat-recovery Cokemaking - A Review of
2011.5.4 A plant scale trial was conducted to recycle the mill oil waste through non recovery coke oven route. The waste mill oil was added in the coal blend as a binder before hammer mill and charged in ...
More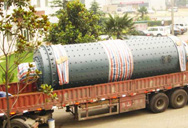
Lecture 32: Coke production - National Institute of Technology,
Briquetting increases strength of coke produced and to make non - coking or poorly coking coals to be used as metallurgical coke. Blending prevents damage to oven when high pressure develops. (b) Coke oven: Oven has usually 0.3 to 0.6m width. Here coal is kept for 17 hrs, heat is supplied completely from the flues on the sides.
More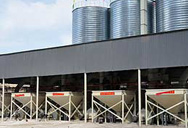
Coke Oven By-Product Plant – IspatGuru
2014.1.17 On a typical coke oven and by-product plant, the liquor production rate is around 120 litres/ton (l/t) to 130 l/t of coal carbonized. The flushing liquor supply to the battery is around 4,000 l/t of coal carbonized, depending upon the battery and collecting main arrangement.
More