
Grinding wheel - Wikipedia
Grinding wheels are wheels that contain abrasive compounds for grinding and abrasive machining operations. Such wheels are also used in grinding machines. The wheels are generally made with composite material. This consists of coarse-particle aggregate pressed and bonded together by a cementing matrix (called the bond in grinding wheel terminology) to form a solid, circular shape. Variou
More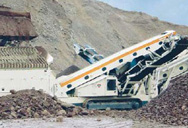
11.31 Abrasives Manufacturing - US EPA
The process description is broken into three distinct segments discussed in the following sections: production of the abrasive grains, production of bonded abrasive products,
More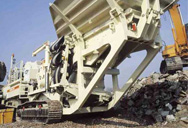
(PDF) Principles of Modern Grinding Technology - ResearchGate
2013.1.1 PDF Principles of Modern Grinding Technology explains the principles that led to rapid improvements in modern grinding technology over recent decades....
More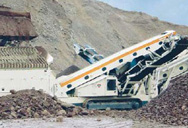
Design of Tools, Grinding Wheels, and Precision Spindles
2020.8.2 This chapter focuses on process demands of ultraprecision machining technology, which contains cutting tools, grinding wheel, and ultraprecision spindle
More
Grinding Wheel - an overview ScienceDirect Topics
In this chapter, the basic characteristics of conventional and superabrasive grinding wheels are described and directions for grinding wheel developments including high-speed
More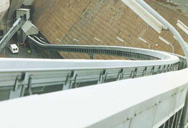
Car steering wheel manufacturing process
The grinding process of transmission gear with worm grinding wheel usually relies on the manual parameter setting by experienced engineers, but the reliability and validity are quite hard to...
More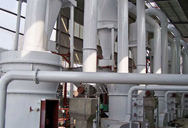
Grinding Wheel Process Flow Diagram [classic] - Creately
Grinding Wheel Process Flow Diagram [classic] by Matthew James. Edit this Template. Use Creately’s easy online diagram editor to edit this diagram, collaborate with others
More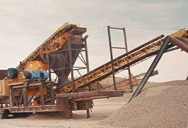
Flow chart for calculating generatrix of wheel with wear.
Download scientific diagram Flow chart for calculating generatrix of wheel with wear. from publication: Simulation of multi-axis grinding considering runout based on envelope theory As...
More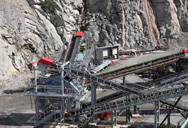
Grinding Wheel Market Size, Share Trends to 2027
Grinding wheel Market size is estimated to grow by 5,877.71 from 2023 to 2027 at a CAGR of 5.24% with the straight wheels segment having the largest market share. ... Approximately 85% of the total production cost
More
Surface Grinding in Silicon Wafer Manufacturing - Kansas State
For example, a typical lapping operation. will take about 40 minutes to reduce the wafer thickness (200mm or 300mm in diameter) by about 80 f.trn D/andamme, Xin and Pei, 20001. As-sliced Waviness Thickness variation. The advantages of surface grinding over lapping are: (1) fully automatic with cassette-to-cassette.
More
Flow chart of grinding procedure. Download
Download scientific diagram Flow chart of grinding procedure. from publication: Grinding Wheel Loading Evaluation by Using Acoustic Emission Signals and Digital Image Processing In the ...
More
Design of Tools, Grinding Wheels, and Precision Spindles
2020.8.2 Noncontact grinding is a grinding method that let the abrasive flow through the surface to be processed which the workpiece is not in contact with the grinding disk and noncontact state. In the mechanical grinding process, the surface of the material will produce a large stress field, so that the surface has been processed to produce
More
Evaluation of the characteristics of diamond grinding wheels at
wheel, e.g., for high-speed grinding, can be determined by meansofcalculation.Indeed,oneofthesolutionstotheprob-lem under consideration is 3D simulation of the mentioned processes. The analysis aims at improving tool reliability at the stages of production, tool sharpening, and operation. Optimum grinding conditions can
More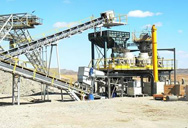
Grinding wheel - Wikipedia
Various types of grinding wheels. Grinding wheels are wheels that contain abrasive compounds for grinding and abrasive machining operations. Such wheels are also used in grinding machines.. The wheels are generally made with composite material.This consists of coarse-particle aggregate pressed and bonded together by a cementing matrix (called
More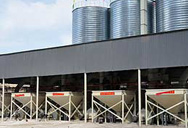
Texturing Methods of Abrasive Grinding Wheels: A Systematic
2022.11.14 Creating textures on abrasive wheels is a strategy that allows a significant improvement in grinding operations. The reduction of the internal stresses in the workpiece and the temperature during the grinding operation generates an increase in the dimensional accuracy of the workpiece and a longer tool life. Textured abrasive wheels
More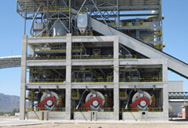
flow chart of grinding wheel production
122KB Chapter 2: Grinding Wheels: Composition and The properties and performance of bonded abrasive tools depend on the type of abrasive grain material, the size of the grit, the bond material, the properties of abrasive and bond, and the porosity Grinding wheels are made from many types of grit in a wide range of sizes, in
More
Flowchart of grinding force calculation process - ResearchGate
But the more complicated grinding process needs special consideration, such as thread grinding, the inclination angle φ of grinding wheel is also considered, and the changed orthogonal coordinate ...
More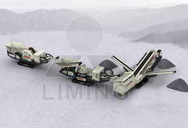
CN103962978A - Grinding wheel manufacturing method
2014.5.5 Compared with prior art, a kind of method for manufacturing grinding wheel provided by the present invention, emery wheel is in grinding process, and the grinding ratio of emery wheel improves 6-15 doubly, emery wheel dust in grinding process has reduced more than 95%, improve production efficiency simultaneously, saved cost,
More
Grinding Wheel Process Flow Diagram [classic] - Creately
Grinding Wheel Process Flow Diagram [classic] Use Creately’s easy online diagram editor to edit this diagram, collaborate with others and export results to multiple image formats. You can easily edit this template using Creately. You can export it in multiple formats like JPEG, PNG and SVG and easily add it to Word documents, Powerpoint (PPT ...
More
Fabrication of Pneumatically Powered Grinding Machine - IRJET
02 Flow control valve 360 03 Bench vice 1000 04 Solenoid valve 1700 05 Connecting nuts and pipes 410 06 Grinding wheel 350 07 Metal pipes for structure 2000 All the parts are assembled together and final model of pneumatically powered grinding machine is made. Fig 02:- Pneumatically powered grinding machine
More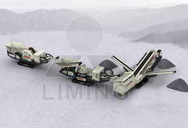
How to Make a Production Flow Chart for
2022.12.21 You know why a production flow chart is important and you’ve seen how it works in our example of a production flow chart. Now, let’s take a look at how you make a production flow chart. 1. Identify
More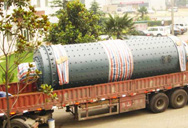
Analysis of loads on grinding wheel binder in
2015.6.1 The load on grinding wheel (GW) binder in grinding process is an important issue in grinding studies. It affects binder behaviors, wheel-workpiece interaction, grinding force, heat and energy ...
More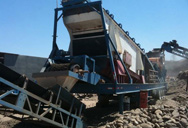
Optimization of Cylindrical Grinding Process Parameters on
The cutting parameters are cutting speed, feed rate and depth of cut for turning of work piece EN 21 tool steel. In this work, the optimal parameters of cutting speed are 1000rpm, 700rpm and 500rpm, feed rate are 0.075mm/min, 0.095mm/min and 0.120mm/min and depth of cut are 0.02mm, 0.03mm and 0.0.04mm.
More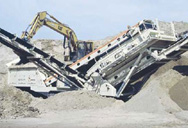
Improving the Productivity of CNC Grinding Machines
B. EWAG machine It is able to process carbide, and CBN/PCD tools, EWAG Compact Line grinder has a number of features designed to reduce non-productive cycle times. C. CNC Profile grinding Machine CNC allows profiling of HM carbide and HSS cutting tools. It was designed for maximum flexibility and ease of operation.
More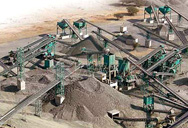
Roll grinding procedures, wheels, belts, setup, end relief, tips
2019.10.8 Grinding tips Roughing. Average wheel speed: 4,000 to 4,500 sfpm; Average roll speed: 100 to 150 sfpm; Rough dress the grinding wheel. Before the start of the grind set for rapid traverse, two-thirds of wheel width or better per revolution. Finishing. Average wheel speed: 4,000 to 4,500 sfpm; Average roll speed: 120 sfpm
More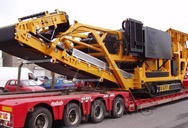
Understanding Forces in Creepfeed Grinding for Reducing Costs
Figure 1: Schematic of simple creepfeed grinding operation. The tangential force is the force required to maintain the wheel speed while it is engaged with the workpiece under the given frictional and cutting forces. It is the sum of the abrasive cutting forces (i.e. forces required to remove material) and frictional forces between the grains ...
More
Electrochemical Grinding SpringerLink
2019.1.1 In ECG processes, schematically shown in Fig. 1, the rotating grinding wheel acts as cathode (negatively charged) which provides the desired shape of the workpiece.The workpiece is connected to the positive pole of a DC power supply. The electrolyte fluid, such as sodium chloride, sodium nitrate, potassium nitrate, etc., is
More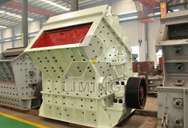
Generating gear grinding
However, generating grinding also shows potential regarding material removal rate, making it even more desirable for batch production [9]. 2.2 Generating gear grinding The gear grinding process can be divided into different classes and subclasses (Figure 1), describing the continuity and shape of the grinding wheel. Generating grinding is based on
More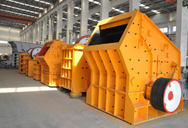
Design manufacturing of feeding mechanism for horizontal grinding
1) Through-feed (thru-feed) Mechanism-The mechanism is simplest of all. The piston rings are supposed to feed manually to the machine by a continuous force. The system actually suits simple shaped work pieces. The feeding system has high efficiency for mass production. Fig 3.
More