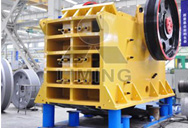
Primary Crushing Station SpringerLink
2023.1.31 Underground primary crushing station (Fig. 3) is generally fixed. It is usually located next to the skip shaft and is characterized by long service life, long
More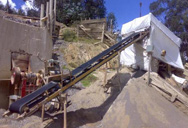
Primary Crusher - an overview ScienceDirect Topics
Primary Crusher. Primary crushers depend for normal operation on the fact that broken rock contains a certain voidage (space between particles). From: Wills' Mineral
More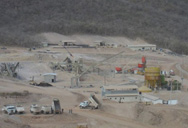
Comminution Circuits for Gold Ore Processing - ScienceDirect
2016.1.1 This chapter considers comminution for gold ores, starting with breakage induced in the blasting process, continuing through primary crushing, primary milling,
More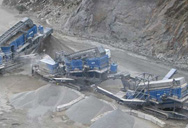
Review of Underground Mining Methods in World
2022.12.23 There are several massive deposits around the world with different geological characteristics. Thus, different mining methods and strategies are applied based on the particularity of each method and
More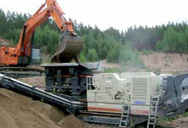
SILICA DUST SOURCES IN UNDERGROUND METAL/NONMETAL MINES - TWO
2002.1.1 U.S. Mine Safety and Health Administration (MSHA) dust compliance sampling data from 2009 to 2012 also indicate that 8.9 percent of the crusher operators in metal/nonmetal mines and mills exceeded ...
More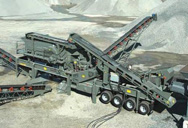
Comminution Circuits for Gold Ore Processing - ScienceDirect
2016.1.1 This chapter considers comminution for gold ores, starting with breakage induced in the blasting process, continuing through primary crushing, primary milling, and secondary milling. Both technical and operational considerations are reviewed; while gold ore comminution is broadly similar to like-sized circuits for other mineral processing ...
More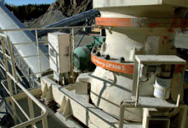
Meekatharra Gold Project - Mining Technology
2013.7.30 Meekatharra Gold Operation (MGO) of Reed Resources is located in the Murchison District of Western Australia. Reed Resources acquired the 2.7 million ounces (moz) gold project from Mercator in January 2011. Metana Minerals, St Barbara Minerals and Mercator Gold previously owned the Meekatharra Gold Mine. The MGO includes the
More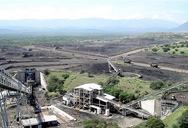
Rock Fragmentation Evaluation towards Blast-To-Mill Concept of
2021.9.29 the Run-of-Mine (ROM) ore to a level that grinding can be carried out until the valuable mineral (e.g., gold) and gangue are substantially produced as separate particles. A primary crusher receives the run-of-mine ore after blasting and produces the first reduction in size after mine field blasting.
More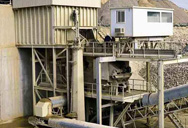
AMIT 135: Lesson 5 Crushing – Mining Mill Operator Training
The purpose of the primary crusher is to reduce the ROM ore to a size amenable for feeding the secondary crusher or the SAG mill grinding circuit. The ratio of reduction through a primary crusher can be up to about 8:1. Feed: ROM up to 1.5 m. Product: -300mm (for transport) to -200mm (for SAG mill) Feed Rate:
More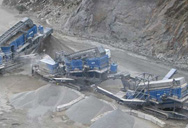
Ivanhoe Mines installs new primary crusher as underground
2018.5.29 Kipushi’s unmined Big Zinc Deposit has an estimated 10.2 million tonnes of Measured and Indicated Mineral Resources grading 34.9% zinc, 0.65% copper, 19...
More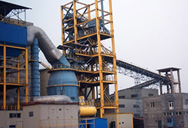
Crusher - an overview ScienceDirect Topics
When used underground, jaw crushers are commonly used in open circuit. This is followed by further size reduction in crushers located on the surface. When the run of mine product is conveyed directly from the mine to the crusher, the feed to the primary crusher passes under a magnet to remove tramp steel collected during the mining operation.
More
primary crusher for underground metal mine
primary crusher for underground metal mine in . The mine is operating an underground crusher on level 850 which is fed by a surge bin reaching up to the 910 level with a capacity of roughly 5000 t The ore is crushed in two steps (primary jaw crusher and secondary cone crusher) to a discharge size of 60 mm and then transported to the processing plant by
More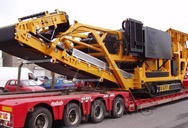
thyssenkrupp launches next-gen ERC primary crusher
2019.9.9 This next generation crusher features a fully hydraulic gap setting/retraction system which allows for automatic adjustment of the gap, compensation of liner wear and release of tramp metal or otherwise uncrushable material content. “The ERC can also crush large hard lumps for example, our ERC 25-25 model has a roll diameter of 2500 mm by
More
NOC 2011 - 8411 - Underground mine service and support
National Occupational Classification (NOC) 2011 - Underground mine service and support workers perform a range of duties related to the operation of orepasses, chutes and conveyor systems, the construction and support of underground structures, passages and roadways, and the supply of materials and supplies to support underground mining.
More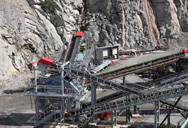
Blasting Techniques Used in Underground and Opencast Mines Mining ...
Pull per round – 1.06 m. Coal yield/kg of explosive – 2.0 te (soligex) Coal yield/detonator – 0.9 te. One driller and two helpers drill 60-70 holes in a shift of 8 hours; one shot firer, 2 explosive carriers and 1 stemming material carrier constitute the blasting crew and fire nearly 60 shots in a shift of 8 hours.
More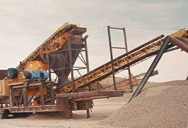
primary crusher used underground metal mine - MC Machinery
Primary Crushing Mineral Processing Metallurgy. Feb 26, 2016 Thus a 15 in by 24 in jaw crusher would be suitable for a small mine hoisting 300 tons in eight hours from underground workings from which lumps larger Gold Mineral Fact Sheets Australian Mines Atlas Gold, the only yellow metal, has the chemical symbol Au, which is derived from the
More
Industrial Solutions Gyratory crushers - ThyssenKrupp
thyssenkrupp gyratory crushers in primary crushing is second to none. KB 63-89 for iron ore. Capacity: 6,200 t/h KB 63-75 for aggregates. Capacity: 2,600 t/h KB 54-75 for iron ore Applications • Large ore mines • Limestone and cement industries • Open pit and underground mining • Aggregates industry Features • Cyclo-palloid spiral ...
More
Primary Crushing Station SpringerLink
2023.1.31 Underground primary crushing station (Fig. 3) is generally fixed. It is usually located next to the skip shaft and is characterized by long service life, long infrastructure time, etc. The main equipment of the primary crushing station includes a crusher, feeder, dedusting apparatus, crane, etc. The primary crusher is mainly divided
More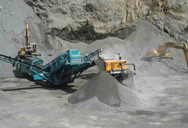
Minerals Free Full-Text A Mine-to-Crusher Model to Minimize
2022.8.18 Innovation has an important role in improving the productivity, safety and sustainability of mining operations. Historically, ore transport was done by diesel trucks, but with the commitment to reduce CO2 emissions and increase mine safety, mining companies have invested in innovative, more sustainable ore transport technologies. The innovative
More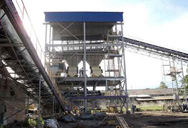
Crusher - Wikipedia
A crusher is a machine designed to reduce large rocks into smaller rocks, gravel, sand or rock dust.. Crushers may be used to reduce the size, or change the form, of waste materials so they can be more easily disposed of or recycled, or to reduce the size of a solid mix of raw materials (as in rock ore), so that pieces of different composition can be differentiated.
More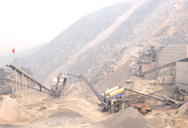
underground mine crushers
Primary crusher for underground metal mine. Underground mining (hard rock) - Wikipedia, the free encyclopedia The primary sources of heat in underground hard rock mines are rock ... A point anchor bolt is a metal bar between 20 mm – 25 mm in diameter, and .... In some cases the underground primary crusher feeds an inclined conveyor
More
Different types of crushing equipments - Constro Facilitator
2020.5.6 Common types of Impact Crushers are Horizontal Shaft Impactor (HSI) and Vertical Shaft Impactor (VSI). The new hybrid models of impact crusher are engineered for maximum feed size, target output size, and total capacity. The newer models are capable of producing construction-grade aggregate, artificial sand and stone materials, run of mine ...
More
Air cleaning performance of a new environmentally controlled primary ...
U.S. Mine Safety and Health Administration (MSHA) dust compliance sampling data from 2009 to 2012 also indicate that 8.9 percent of the crusher operators in metal/nonmetal mines and mills exceeded the 100 μg/m 3 respirable silica dust limit, with 24.8 percent of these operators exceeding a 50 μg/m 3 silica dust level (U.S. Department of Labor, 2013).
More