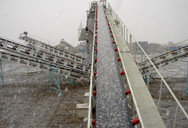
A vertical ball mill as a new reactor design for ... - ScienceDirect
2017.12.1 Abstract. A vertical ball mill (VBM) reactor was evaluated for use in biomass conversion processes. The effects of agitation speed (100–200 rpm), number of
More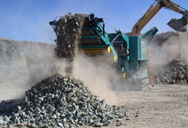
Design and Testing of UMM Vertical Ball Mill (UVBM) for
2018.4.1 The concept of design was adopting design theory of Phal and Beitz with emphasis on increasing of probability of success in engineering and economy
More
(PDF) A vertical ball mill as a new reactor design for
2017.7.28 A vertical ball mill (VBM) reactor was evaluated for use in biomass conversion processes. The effects of agitation speed (100-200
More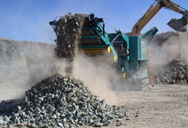
Design and Testing of UMM Vertical Ball Mill (UVBM) for
2018.4.1 The concept of design was adopting design theory of Phal and Beitz with emphasis on increasing of probability of success in engineering and economy
More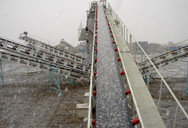
Analysis and Optimization of Grinding Performance of
2022.1.23 This work concentrates on the energy consumption and grinding energy efficiency of a laboratory vertical roller mill (VRM) under various operating parameters. For design of experiments (DOE), the
More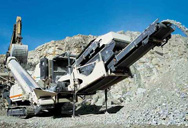
A Novel Particle-Based Approach for Modeling a Wet Vertical
2021.1.9 Modeling of wet stirred media mill processes is challenging since it requires the simultaneous modeling of the complex multiphysics in the interactions between grinding media, the moving internal agitator elements, and the grinding fluid. In the present study, a multiphysics model of an HIG5 pilot vertical stirred media mill with a nominal
More
(PDF) A Comparative study on a vertical stirred mill agitator design ...
2015.7.16 This study focused on ultra-fine grinding of calcite powder (CaCO3) using a vertical stirred ball mill. The influences of various operating parameters such as stirrer speed (rpm), ball filling ...
More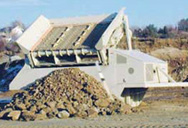
Lime Slaking Systems - Storage Transfer Technologies (STT)
Vertical Ball Mills When lime or water quality is poor and/or when lime consumption rates are high, STT designs slaking systems utilizing a vertical ball mill. The total grinding process of a vertical ball mill utilizes all residual reaction value, virtually eliminates grit disposal problems, and significantly improves lime usage efficiency.
More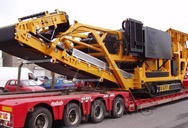
Verticall Ball Mill Slaker Storage Transfer Technologies (STT)
2022.3.28 Vertical Ball Mill Slakers Eliminate Grit Disposal Problems When lime or water quality is poor and/or when lime consumption rates are high, STT designs slaking systems utilizing a vertical ball mill. The total grinding process of a vertical ball mill utilizes all residual reaction value, virtually eliminates grit disposal problems, and significantly
More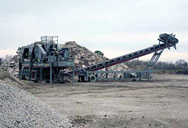
Stirred Mill - an overview ScienceDirect Topics
Stirred Mills – Ultrafine Grinding. In Mineral Processing Design and Operations (Second Edition), 2016. 10.2.4 Operation of Vertical Mills. Vertical stirred mills are usually charged with media occupying 80% of the mill volume which is in sharp contrast to tumbling mills that are seldom charged more than 40% of their volumes to allow space for the tumbling
More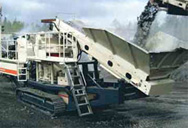
Cement grinding Vertical roller mills VS ball mills
For a ball mill grinding OPC to a fineness of 3200 to 3600 cm2/g (Blaine) the cost of wear parts (ball, liners and mill internals) is typically 0.15-0.20 EUR per ton of cement. For an OK mill grinding a similar product, the cost of wear parts depends on the maintenance procedures, i.e. whether hardfacing is applied.
More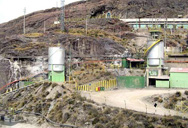
OPTIMIZATION OF MILLING PARAMETERS OF PLANETARY BALL MILL
The ball mills can be classified into two categories according to the axis of rotation of the bowl. 1. Vertical axis and 2. Horizontal axis. Figure 1 Direction of rotations of drums in (a) Vertical and (b) Horizontal axis ball mills In Vertical axis ball mill, the drum with material to be ground and grinding balls rotates about
More
The Influence of Stirred Mill Orientation on Calcite Grinding
2021.4.21 In this study, mill orientations (vertical vs. horizontal) were compared in the same mill (same design) and under the same test conditions, which has not been studied before. On the other hand, a qualitative comparison of the number of stress events, especially stress intensity, could be used to explain comminution results obtained from
More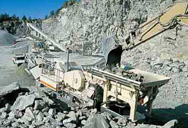
Modelling of vertical spindle mills. Part 2: Integrated models for E ...
2015.3.1 Mill description. Three different vertical spindle mill designs were investigated and modelled as a part of the Asia-Pacific Partnership on Clean Development and Climate program (APP) funded by the Australian Government Department of Resources, Energy and Tourism. All are called vertical spindle mills reflecting their
More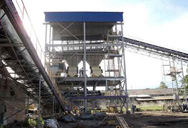
A vertical ball mill as a new reactor design for ... - ScienceDirect
2017.12.1 A vertical ball mill (VBM) reactor was evaluated for use in biomass conversion processes. The effects of agitation speed (100–200 rpm), number of glass spheres (0–30 units) and temperature (40–46 °C) on enzymatic hydrolysis of rice straw and on glucose fermentation by a thermotolerant Kluyveromyces marxianus strain were
More
Design and Analysis of Ball Mill For Paint Industries - IJSRD
Design and Analysis of Ball Mill For Paint Industries Mayur H Patel1 Mr. Vishal A Pandya 2 1ME-Machine Design- pursuing2Asst. Prof 12 B.V.M Engineering College, ... Vertical ball mills often come with a variety of ball sizes (and have variable speed settings) for more efficient processing.
More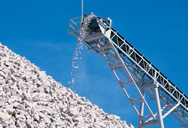
(PDF) Industrial Vertical Stirred Mills Screw Liner Wear Profile ...
2021.4.10 Vertical stirred mills have been widely applied in the minerals ... mills presents the energy saving around 30% when compared to tumbling ball mills used. ... such as the industrial VTM-1500 design.
More
OK™ cement mill The most energy- efficient mill for cement
mill consistently uses five to ten percent less power than other cement vertical roller mills, and in comparison with traditional ball mill operations, the energy requirements for the OK cement mill is 30-45 percent lower for cement grinding and 40-50 percent lower for slag. The OK mill can contribute significantly to profitability and
More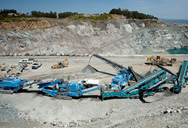
FLSmidth® Tower Mill A vertical leap in fi ne grinding
The major design feature of the tower mill is a central agitator screw, the only moving machine component in contact with the slurry and steel media, which allows size reduction by attrition. This arrangement reduces energy consump-tion in fine grinding of minerals by 25% to 50% when compared to traditional horizontal ball mills for the same
More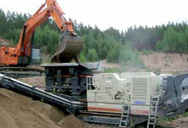
Investigating grinding media dynamics inside a vertical stirred mill
2020.3.15 In this work the grinding media motion inside a vertical stirred mill was investigated using the Discrete Element Method (DEM) and the results were qualitatively compared against similar conditions from published literature. Two impeller designs having different arm length were investigated as function of low and high rotational speeds (50
More
Ball Mill Design/Power Calculation - 911 Metallurgist
2015.6.19 Ball Mill Power/Design Calculation Example #2. In Example No.1 it was determined that a 1400 HP wet grinding ball mill was required to grind 100 TPH of material with a Bond Work Index of 15 (guess what mineral type it is) from 80% passing ¼ inch to 80% passing 100 mesh in closed circuit.
More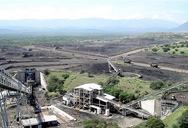
Vertical Roller Mills - FLSmidth
PERI™ AutoCharge Mill Grinding Ball Charging System. Back. PERI™ Online Slurry Analysis System. ... The OKTM Mill’s flexible design makes it possible to operate it with a number of rollers out of service while still reaching 60 to 70 percent of the normal ... As vertical roller mills are 30 to 50 percent more efficient than other grinding ...
More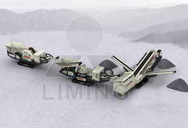
Design and Testing of UMM Vertical Ball Mill (UVBM) for
2018.4.1 UMM Vertical Ball Mill (UVBM) was intended to be the apparatus to produce metal powder with superior characteristic in production rate while retaining good quality of metal powder. The concept of design was adopting design theory of Phal and Beitz with emphasis on increasing of probability of success in engineering and economy
More