
Cement plant performance optimization Benchmarking, correction
Benchmarking, correction and sustaining services to improve system performance. Process and energy consulting optimization services identify and remove performance problems
More
Optimization of Cement Manufacturing Process - ScienceDirect
1987.8.1 Optimization of Cement Manufacturing Process. Cement manufacturing process is now operated with the aid of various control systems, such as raw meal
More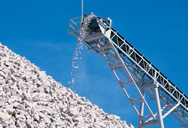
OPTIMIZATION OF CEMENT GRINDING OPERATION IN BALL MILLS
The consumption of energy by the cement grinding operation amounts to one third of the total electrical energy used for the production of cement. The optimization of this process
More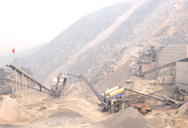
Full article: Evaluation of optimization techniques for predicting ...
Utlu et al. (Citation 2006) also assessed the energy and exergy efficiency of a cement raw mill in the sector. Atmaca and Atmaca ( Citation 2016 ) summarised the cement
More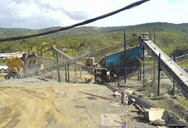
Cement Mills Optimization--- The Quality Perspective - LinkedIn
2019.6.13 Overview: Cement Milling / Finish grinding is the last unit operation in the cement manufacturing process (Excluding Cement Packing). However, is most critical
More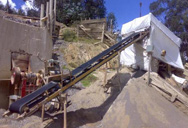
Cement Industry - Optimization, Characterization and Sustainable ...
2021.6.9 Cement is the basis of the building and construction industry and of fundamental importance for many civil engineering applications. As such, the cement
More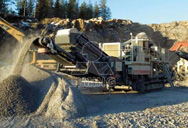
Digitization and the future of the cement plant McKinsey
2020.9.16 The plant has an average overall equipment effectiveness (OEE) of 90 percent, and it uses up to 15 percent plastics as an alternative fuel source. It has also
More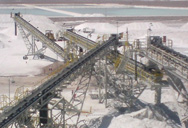
Cement grinding optimisation - ScienceDirect
2004.11.1 The increasing demand for “finer cement” products, and the need for reduction in energy consumption and green house gas emissions, reinforces the need for
More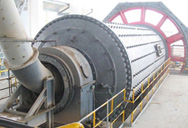
optimising >> - ABB
experts, at Adana Cement on 11 May 2009 for process optimisation of clinker production line 4, which has an average capacity of 4500 tpd, including the control of the rotary kiln,
More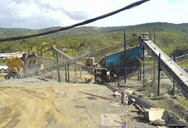
Optimization of Cement Grinding Operation in Ball Mills PEC ...
The optimization of this process would yield substantial benefits in terms of energy savings and capacity increase. 1. Optimization of the Cement Ball Mill Operation. Optimization
More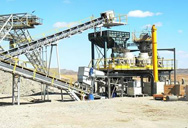
LM Master: Optimising VRM - Indian Cement Review
2021.10.14 LM Master: Optimising VRM. Vertical roller mills are often operated at lower capacities to safeguard the process against variables in feed characteristics. Using intelligent automation tools for mill control, operators can consistently obtain a good quality product while running the mill at its optimum capacity.
More
Energy and exergy analyses for a cement ball mill of a
2020.2.1 Nowadays, ball mills are used widely in cement plants to grind clinker and gypsum to produce cement. In this work, the energy and exergy analyses of a cement ball mill (CBM) were performed and ...
More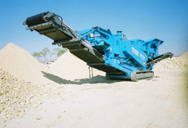
ABB Ability Expert Optimizer for cement
RMP for raw mill (Raw Mix Proportioning module) reduces and controls short-term fluctuations to the target values by controlling the dosage of raw meal additives to the raw mill feed. Features. Mix control with laboratory
More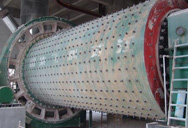
Effects and Control of Chemical Composition of Clinker for Cement ...
2020.10.15 Clinker of cement consists of alite C3S (Tricalcium silicate Ca3SiO5), belite C2S (Dicalcium silicate Ca2SiO4), aluminate C3A (Tricalciumaluminate Ca2Al2O6) and ferrite C4AF (Tetracalcium ...
More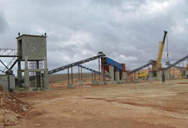
Technological Energy Efficiency Improvements in Cement Industries
2021.3.30 Figure 1. Cement production process. The colored boxes show the sequential operations, while the white boxes summarize the process machinery. Based on the water content of the raw materials, the cement manufacturing process can be divided into four categories: dry, semi-dry, semi-wet, and wet [9]. Since cement
More
Indian Cement Sector – A Hallmark of Energy Efficient Operations
2021.7.28 Cement Mill - Vertical Roller Mill: 27.07: Cement Mill - Ball Mill Closed Circuit: 23.20: Cement Mill - Ball Mill with HPRG: 0.65: Packing Plant: 0.67: ... efficiently combine high grade limestone with that of poor grade to enhance the life span of captive mines while also optimising the requirement of raw ore. ...
More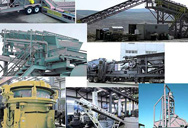
How can we improve cement mill production? - LinkedIn
2023.2.21 To improve cement mill production, consider increasing the mill's capacity, optimizing operating parameters, improving the grinding process, enhancing separator efficiency, and implementing online ...
More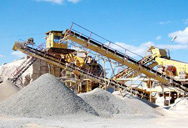
OPTIMIZING THE CONTROL SYSTEM OF CEMENT MILLING:
Mill Feed Sep. Return Final Product System Fan Figure 1: Closed circuit grinding system. milling system is a delicate task due to the multivari-able character of the process, the elevated degree of load disturbances, the different cement types ground in the same mill, as well as the incomplete or missing information about some key process charac-
More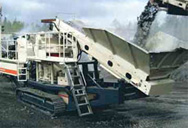
Cement mills optimising parties
Optimizing cement mill using APC techniques at Votorantim Cimentos 1 raw mill vertical 1 coal mill balls 1 kiln ; 1 calciner ; 1 cooler ; 2 cement mills vertical Customer benefits: Reduction in standard deviation of . raw mill power - 62%, raw mill bed depth - 60%, kiln motor load - 24%, free lime - 27%, liter weight 16%, burning zone temperature - 5%;
More
sbm/sbm presentation on optimization ofcement ball mill
You've already forked sbm 0 Code Issues Pull Requests Packages Projects Releases Wiki Activity
More
Integrated energy optimisation for the cement industry: A case
2014.2.1 Finishing mill: P11: Cement (n products) [t] M11: Cement silo for product i: M12: ... A third-party optimiser was used to optimise the generated model for optimal cost. ... Implementing the developed ENMS resulted in a reduction in peak electricity demand while optimising electricity costs for the cement plant.
More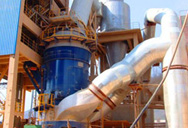
Digitalization, Control and Optimization for Cement Plants
2021.1.1 Abstract. In this paper, we present digitalization, control and optimization for entire cement plants based on model predictive control (MPC) technologies. We provide an overview of the employed MPC technologies and report statistics from several industrial implementations. This demonstrates that MPC technology can simultaneously increase
More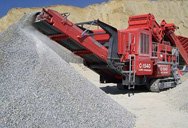
Modeling of energy consumption factors for an industrial cement ...
2022.5.9 Cement production is one of the most energy-intensive manufacturing industries, and the milling circuit of cement plants consumes around 4% of a year's global electrical energy production. It is ...
More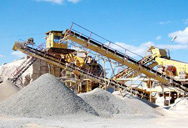
Cement Industry - Optimization, Characterization and Sustainable ...
2021.6.9 Cement is the basis of the building and construction industry and of fundamental importance for many civil engineering applications. As such, the cement industry is one of the key industries worldwide necessary for the current and future sustainable development of society. Despite its undisputed importance, the cement
More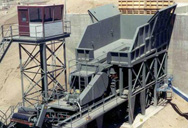
cement mills optimising parties
Unlocking Plant Capability through Targeted In 2009 Arrium began an optimization program on the concentrator plant to updated ensuring the rigour of third party review was continued Grinding Rolls 39 Performance – A Case Study with the
More
Methodological development for the optimisation of electricity
2021.11.10 Cement factories require large amounts of energy. 70% of the variable cost goes to energy—33% to kiln thermal energy and 37% to electrical energy. This paper represents the second stage of a broader research study which aims at optimising electricity cost in a cement factory by means of using artificial intelligence. After an
More
Building Main Head an intelligent cement plant - ABB
ball mill that is used for the production of high-quality and special cements using a hybrid third-generation separator. Following the successful roll-out on CM3, the system has now been installed on the plant’s two additional cement mills (CM2 and CM4), as well as the raw materials mill with commissioning scheduled in late February.
More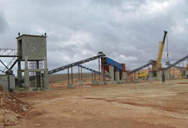
CRUSHERS SIZERS Optimising Salonit Anhovo’s crushing process
Optimising Salonit Anhovo’s crushing process When Slovenia-based producer Salonit Anhovo looked to optimise its primary crushing process, thyssenkrupp Cement Technologies implemented a modern, alternative system ... raw material either for ball mills (0-25mm) or for vertical roller mills (0-80mm). A suitable location
More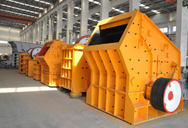
Monetary Benefits due to Process Improvements in Raw and Cement Mills
2018.8.23 Let us consider the larger Cement Plant Y, with an annual production of 1 million tons of clinker in a region with high energy costs of 150 USD/MWh: the monetary benefits of a 5% increase in ...
More
cement mills optimising parties
Cement Mills Optimization--- The Quality Perspective - PROCESS DIAGNOSTIC STUDIES FOR CEMENT MILL Mill Feed Sep. Return Final Product System Fan Figure 1: Closed circuit grinding system. milling system is a delicate task due to the multivari-able character of the process, the elevated degree of load disturbances, the different cement types ground
More