
Iron ore beneficiation: an overview - ScienceDirect
2023.1.1 Iron ore processing operating practices vary depending upon the the quality of iron ore deposit. For high-grade ore, dry- or wet processing can carried out and for
More
Comminution and classification technologies of iron ore
2022.1.1 Most of the high-grade hematite iron ores are typically subjected to simple dry processes of crushing and classification to meet the size specifications required for
More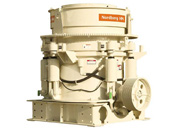
Iron Ore Beneficiation ST Equipment Technology
Dry processing of iron ore presents an opportunity to eliminate costs and wet tailings generation associated with flotation and wet magnetic
More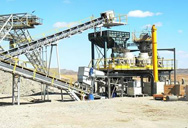
Different Effects of Wet and Dry Grinding on the Activation of Iron
1 Introduction Iron Ore Tailings (IOTs) refer to the solid waste associated with the process of iron concentrate extraction from iron ore and are an important source of environmental...
More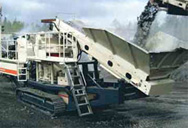
Modification of Wet Granulation Process During Iron Ore Sintering ...
2020.7.1 Mixture of iron ore fines, limestone, dolomite, coke breeze, lime and metallurgical wastes are fused partially to form lumpy porous iron bearing mass called
More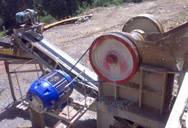
Different Effects of Wet and Dry Grinding on the Activation of Iron
The effect of wet grinding on the activation of IOTs was evaluated through ion leaching from an alkaline solution and the reactivity index. Additionally, a detailed comparison
More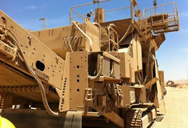
Magnetic separation studies for a low grade siliceous iron ore
2013.1.1 Considerable advantages must, therefore, be offered by dry separation techniques to justify its use in preference to wet process. This present paper discusses
More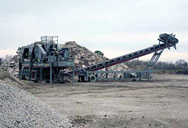
Characterization and Beneficiation of Dry Iron Ore ... - Springer
During dry processing of iron ore in Khondbond region of Orrisa, approximately 30 –40% (by weight) of total feed is produced as fines. These fines are being dumped and get
More
Different Effects of Wet and Dry Grinding on the Activation of Iron Ore
Wet grinding; iron ore tailings; particle characteristics; mineral admixture 1 Introduction Iron Ore Tailings (IOTs) refer to the solid waste associated with the process of iron concentrate extraction from iron ore and are an important source of environmental pollution [1,2]. Approximately 5 billion tons of IOTs are currently present in China ...
More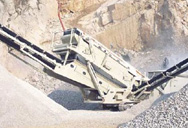
Magnetic separation studies for a low grade siliceous iron ore sample ...
2013.1.1 Considerable advantages must, therefore, be offered by dry separation techniques to justify its use in preference to wet process. This present paper discusses both the dry and wet magnetic separation techniques used for processing of a low grade siliceous iron ore sample. 2. Materials and methods
More
Controlling the rheology of iron ore slurries and tailings with
2021.6.1 Storing tailings with paste-like consistency or high yield stress and viscosity is one way of reducing the risk. Iron ore plants that adopt a wet fine recovery process produce a large amount of waste comprising of solids and water. A large amount of water is required to separate the fine value leaving a large amount of dilute tailings for disposal.
More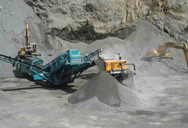
Iron ore concentration process with grinding circuit, dry
The present invention discloses an advantageous and effective process for the concentration of iron ores, which can be fully dry or mixed, part of the process being dry, part wet. The invention thereby improves process efficiency as a whole by increasing recovery of concentrators and increasing the useful life of the mines.
More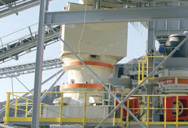
Electroosmotic Dewatering of Iron Ore Tailings: A Laboratory
2022.10.28 Minerals are subjected to ore processing to turn them into usable and saleable raw materials. First of all, the ore is reduced to the smallest size with the crushing-grinding process, and after using water and chemical additives, according to the characteristics of the ore, useful minerals are taken, and unwanted minerals are stored in
More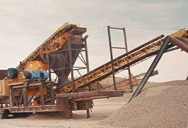
Different Effects of Wet and Dry Grinding on the Activation of Iron Ore ...
2021.1.1 XPS analysis was used to characterize the effects of dry and wet grinding on the surface characteristics. The high-resolution scan curves for Si2p, Al2p, and O1s, which are important for the ...
More
New dry iron ore processing technology developed
2016.5.26 New dry iron ore processing technology developed. Ben Creagh May 26, 2016, 9:24 am. The mine tailing dam spill at BHP and Vale’s Samarco iron ore operations last year killed 19 people and had ...
More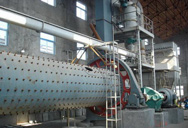
What is dry screening iron ore? - LinkedIn
Published Mar 30, 2023. + Follow. Dry screening of iron ore refers to the process of removing impurities and unwanted materials from the ore through the use of various screening techniques. This ...
More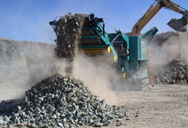
Different Effects of Wet and Dry Grinding on the Activation of Iron Ore
Iron Ore Tailings (IOTs) refer to the solid waste associated with the process of iron concentrate extraction from iron ore and are an important source of environmental pollution [1,2]. Approximately
More
Use of dry grinding process to increase the leaching of gold from
2021.5.1 Iron-containing oxides are the main minerals associated with roasted gold concentrates. The influence of different iron-containing oxides on the gold thiosulfate leaching process is very complex. In this study, we found the use of dry grinding methods can considerably eliminate the adverse effects on gold thiosulfate leaching under wet
More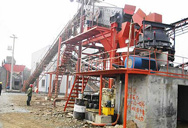
A Novel Sintering Process for Porous Iron Ore Sintering with
2022.2.28 The present work proposes a novel process to sinter porous iron ore (porosity ~23–24%) with enhanced productivity and quality. The iron ore is pre-processed in the presence of calcined lime for the temporary closure of pores, which further prevents water absorption during the granulation process in drum in the presence of water. The
More
Beneficiation of Magnetite Ores
Platts Iron Ore Index specification. The demonstrated economic and socio-environmental benefits show that dry processing flowsheet o ers significant energy and cost savings and improved revenue generation compared with the wet process flowsheet. These findings are vital to the magnetite
More
Different Effects of Wet and Dry Grinding on the Activation of Iron Ore
Additionally, a detailed comparison between Dry-grinding Iron Ore Tailings (DIOTs) and Wet-grinding Iron Ore Tailings (WIOTs) was made. This comparison was based on particle characteristics, crystal structures, chemical structure, and surface properties. The results showed that the particle size of IOTs reduced rapidly during wet grinding.
More
Economic and Socio-Environmental Benefits of Dry Beneficiation
2020.10.26 The LKAB iron ore operations in Sweden process high-grade magnetite ore through an AG milling circuit with a throughput of 500 to 582 t/h to achieve product P 80 of 45 µm . Since the conventional SABC milling circuits are not efficient in achieving the required magnetite liberation sizes, usually less than 45 µm, IsaMill™ and stirred media
More
Development of a Novel Grinding Process to Iron Ore Pelletizing
2020.3.28 Modern iron ore pelletizing process operations may be divided into two main process sections: feedstock preparation and agglomeration processes. ... The intrinsic pellet quality was compared with agglomerates generated from a ball-milled ore blend, where wet-CCS and dry-CCS presented respectively 1.1 and 4.1 kgf/pel ...
More
A comparative study on the effects of dry and wet ... - ScienceDirect
2019.9.1 Feng and Aldrich (2000) also observed that the dissolution of Cu, Ni, and Pd from a platinum-bearing sulfide ore was higher after dry grinding compared with the wet process. They indicated the dry ground particles showed more stable, higher loaded froths than wet ones [14] .
More
Modification of Wet Granulation Process During Iron Ore
2020.7.1 Sintering is the most extensively used and economic agglomeration process to prepare iron ore fines for blast furnace use. Granulation is the most critical factor controlling iron ore sintering process, as it improves sinter mix permeability. Currently, sinter plants are receiving significant proportion (up to 40%) of − 150 μm micro
More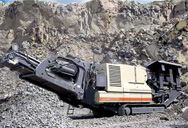
Iron ore concentration process with grinding circuit, dry
The present invention discloses an advantageous and effective process for the concentration of iron ores, which can be fully dry or mixed, part of the process being dry, part wet, such enhancing the process efficiency as a whole by increasing recovery of concentrators and increasing the useful life of the mines.
More
Fortescue - explaining the various cost and price metrics
2015.3.20 Fortescue’s delivered price is adjusted for its quality and lower ferrous content – it has historically been able to sell its product at an 85% discount to the index price. So if the iron ore index price is at US$58/dmt, Fortescue will be realising a price of about US$58 x 85% = US$49.3/dmt on its iron ore. C1 Cost.
More
What is wet process cement? - LinkedIn
2023.3.23 The wet process is one of the two primary methods used in cement manufacturing, the other being the dry process. The wet process involves mixing raw materials such as limestone, clay, and iron ore ...
More