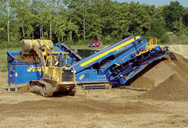
Characterization and Beneficiation of Dry Iron Ore Processing Plant ...
2018.9.18 During dry processing of iron ore in Khondbond region of Orrisa, approximately 30–40% (by weight) of total feed is produced as fines. These fines are
More
Iron ore beneficiation: an overview - ScienceDirect
2023.1.1 Dry processing of iron ore: In dry processing of iron ore, ROM is generally crushed below 40 mm through three-stage crushing and thus segregated by
More
Characterization and Beneficiation of Dry Iron Ore Processing Plant ...
fine ore having size below 8 –10 mm. Dry processing of iron ore is popular for treating hard massive hematitic ores; however, fines generated during processing of goethite
More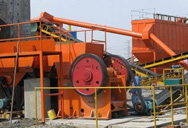
Evaluation of Dry Processing Technologies for Treating Low Grade ...
2020.10.25 Dry processing options, involving the use of a circulating air classifier and thermal roasting (advanced microwave-assisted magnetizing roasting), followed by
More
Energy analysis of the convective drying of iron ore
2022.10.19 Last Updated: 09 Jun 2023. PDF Drying operations in iron ore processing plants have a particularly high energy demand due to the massive solid flow rates employed in this... Find, read and ...
More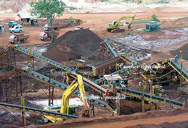
Iron Ore Processing, General SpringerLink
2022.10.20 Making iron and steel from iron ore requires a long process of mining, crushing, separating, concentrating, mixing, agglomeration (sintering and pelletizing),
More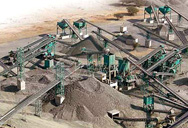
Comminution and classification technologies of iron ore
2022.1.1 Introduction. Hematite and magnetite iron ores are the most prominent raw materials for iron and steel production. Most of the high-grade hematite iron ores are
More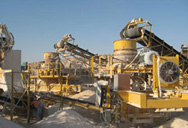
Characterization and drying kinetics of iron ore pellet feed and
Here, the characterization and drying kinetics of iron ore concentrates were presented and recommendations for the design of dryers were discussed. Pellet feed and sinter feed
More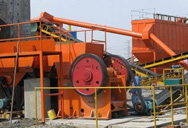
A novel dry gravity separation method for cleaner production of
It is noted that the fabricated unit can produce the sinter grade concentrate (63.5% Fe) with a mass recovery of 22.7% from iron ore 1 and 24.9% from iron ore 2. The performance
More
ADVANCES IN MAGNETIC SEPARATION OF ORES - 911
netic separation of iron ore have been in the field of dry processing, where a major revolution in iron ore beneficiation may be taking place. But now consider an area of magnetic separation where dry methods have never lost their attractiveness. Table I. Iron Analysis of Crude and Beneficiated Minerals Used in the Ceramic Industry Beneflcisted ...
More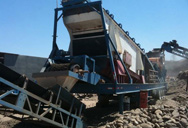
Solar-thermal beneficiation of iron ore: System-level dynamic ...
2022.12.11 According to Mujumdar [13], a range of drying operations are applicable in iron ore processing: moving grate dryers at 300 °C to 450 °C are used for drying of ‘green pellets’ [14], while rotary, shaft, fluidised bed and rotating-shelf dryers are used to dry iron ore concentrates.
More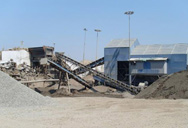
Dry processing of magnetic iron ores - addressing cost and ...
This product is exclusive to Digital library subscription. Subscribe. Dry processing of magnetic iron ores - addressing cost and environmental issues. PDF. Normal price $22.00. Member price from $0.00. Add to cart. Fees above are GST inclusive. PD Hours.
More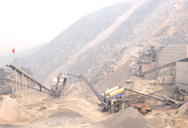
Controlling the rheology of iron ore slurries and tailings with
2021.6.1 Billions of tons of this material is consumed every year. To be economical and profitable, the daily product throughput of a given mine must be high and the mining and processing of the iron ore must be very efficient. Iron ore are beneficiated and derived from both dry and wet processing. In wet processing, the waste or tails are separated ...
More
Evaluation of Dry Processing Technologies for Treating Low
2020.10.25 ABSTRACT. Dry processing options, involving the use of a circulating air classifier and thermal roasting (advanced microwave-assisted magnetizing roasting), followed by magnetic separation using an Induced Roll Magnetic Separator (IRMS), were evaluated for upgrading low-grade hematite-goethite iron ore fines.
More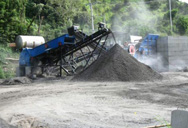
Beneficiation of Magnetite Ores
dam of one of Vale’s iron ore mines in Brazil collapsed killing 270 people with more than 180 people reported missing [12]. These challenges bring substantial economic uncertainties to large-scale, heavily capitalized wet mineral processing operations. Given these challenges, the application of dry processing technologies in iron ore ...
More
Vale starts dry iron ore concentration pilot with New Steel
2020.7.16 Vale has inaugurated its new dry pilot plant for processing iron ore in Minas Gerais, Brazil, as it continues to reduce its use of water in ore and waste processing. The Brazilian technology, known as FDMS (Fines Dry Magnetic Separation), is unique and has been developed by New Steel – a company Vale acquired in late 2018.
More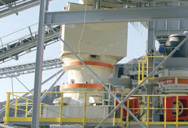
Processing of Lean Iron Ores by Dry High Intensity Magnetic Separation ...
2015.2.9 Abstract. Dry high intensity magnetic separation (DHIMS) is investigated to process a lean hematite ore. It was found the feed particle size and the drum rotation speed have significant influences ...
More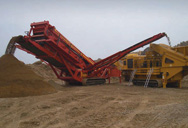
Developments in the wet and dry processing of lower grade magnetite ores
The results of early laboratory test work on the development of an efficient and environmentally sustainable dry processing option for the beneficiation of lower grade magnetite ores were tabled by IMP Technologies Pty. Ltd. (IMPTEC) and Cyclomag Pty.Ltd. at Iron Ore 2017 in Perth W.A. Since that time, the companies have experienced
More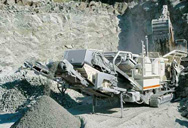
Comminution and classification technologies of iron ore
2022.1.1 Additionally, iron ore processing facilities often receive ores from various sources (such as satellite pits) with different qualities. These ores may be treated by different processing routes and/or blended to meet product specifications. Some examples of different iron ore crushing and screening flowsheets are provided below: 8.2.3.1.
More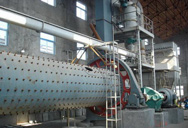
Electroosmotic Dewatering of Iron Ore Tailings: A
2022.10.28 Minerals are subjected to ore processing to turn them into usable and saleable raw materials. First of all, the ore is reduced to the smallest size with the crushing-grinding process, and after using water
More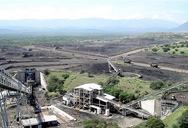
Evaluation of VSK separation in the classification of two ...
2022.12.21 With gradually diminishing Fe grade in tandem with the ever-increasing demand for high-grade iron ores, iron ore industries are now focusing on the beneficiation of low-grade iron ore fines, mainly considered waste. Besides, the scarcity of water at many of the mines’ sites and the new water conservation policies of the governments have
More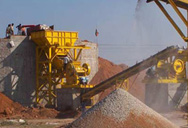
The six main steps of iron ore processing - Multotec
Six steps to process iron ore. 1. Screening. We recommend that you begin by screening the iron ore to separate fine particles below the crusher’s CSS before the crushing stage. A static screen is used to divert the fine particles for crushing. This step prevents overloading the crusher and increases its efficiency.
More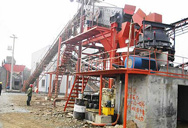
A Novel Sintering Process for Porous Iron Ore Sintering with
2022.2.28 The present work proposes a novel process to sinter porous iron ore (porosity ~23–24%) with enhanced productivity and quality. The iron ore is pre-processed in the presence of calcined lime for the temporary closure of pores, which further prevents water absorption during the granulation process in drum in the presence of water. The
More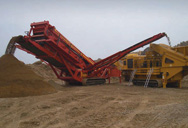
NMDC : Press Release on “NMDC and CSIRO signed Research
2018.5.31 A one day work shop on "PROCESSING OF COMPLEX GOETHITIC IRON ORES " was organized jointly by NMDC and CSIRO Austr alia in th e premises of NMDC RD Centre, Hyderabad on 29 1 h May 2018. The work shop covered various technical aspects rang ing from Iron Ore Characterization, Geometallurgy, Beneficiation
More
Beneficiation of Iron Ores – IspatGuru
Dry processing of iron ore – It presents an opportunity to eliminate costs and wet tailings generation associated with flotation and wet magnetic separation circuits. STET (ST equipment and technology) has evaluated several iron ore tailings and run of mine ore samples at bench scale (pre-feasibility scale).
More
Recovery of magnetite-hematite concentrate from iron ore
A processing flowsheet includes magnetic separation, milling and gravity concentration methods. The separation technology provides for production of iron ore concentrate with total iron content of 65.9% and recovers 91.0% of magnetite and 80.5% of hematite from the tailings containing 20.4% of total iron.
More
Processing of Magnetite Iron Ores–Comparing Grinding Options
• CMS2 – second cleaner magnetic separation, 2 Perth, WA, 27 - 29 July 2009 Iron Ore Conference PROCESSING OF MAGNETITE IRON ORES – COMPARING GRINDING OPTIONS 90 y = 10.737ln(x) - 3.0945 80 R² = 0.9705 Mass % of feed to magnetic concentrate 70 60 50 40 30 10 100 1000 10000 P80 Size (µm) FIG 2 - Grind versus
More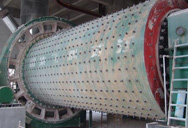
Beneficiation of Low-Grade Dilband Iron Ore by Reduction
2023.2.1 This research is aimed at the up-gradation of indigenous Pakistani iron ore, i.e., Dilband iron ore (hematite), by utilizing common metallurgical processes. First, the magnetic properties of the ore were determined. Initially, the iron ore samples contained 34 wt. % Fe in addition to other gangue materials. Therefore, the ore was subjected to a
More