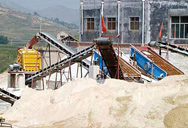
CHAPTER 20: SIZE REDUCTION – EQUIPMENT FOR SIZE
• Size reduction is by compression, impact and shear and not by compression alone, as in the case of smooth roll crushers • Can accommodate larger particles than
More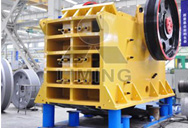
(PDF) SIZE REDUCTION BY GRINDING METHODS
2017.3.4 Grinding mills – Reduction ratios . All crushers including impactors have lim ited reduction ratios. Due to the design there is a
More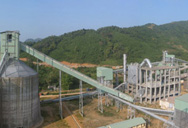
Size reduction in feed technology and methods for determining ...
2020.3.1 The hammer mill has the highest reduction ratio of 5.95 for coarsely ground corn, followed by the roller mill, whilst the multicracker system (see the
More
Determining the Bond Efficiency of industrial grinding circuits
2DETERMINING THE BOND EFFICIENCY OF INDUSTRIAL GRINDING CIRCUITS Calculations: 1. Calculate the Actual Operating Bond Work Index of the grinding circuit. •
More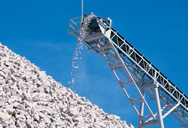
Energy-Efficient Advanced Ultrafine Grinding of Particles Using
2023.7.10 Grinding becomes simpler after the ore has been crushed until the minerals and gangue have been largely separated. After this activity, the ore is
More
SAG Mill Grinding Circuit Design - 911 Metallurgist
2016.6.6 The ratio of the trunnion thickness to trunnion diameter in a mill of 2,134 m diameter is almost twice that of a mill of 5,8 m diameter, i.e. a ratio (T/D) of 0,116 to 0,069 for the large mill. However the design stress
More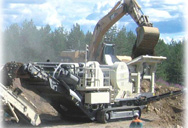
Full article: Optimizing hammer mill performance through screen ...
2014.4.9 The results are presented in two sections: improved size reduction via optimization of hammer mill configuration, and improved control of particle size and
More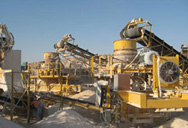
SIZE REDUCTION BY GRINDING METHODS By - ResearchGate
Grinding mills – Reduction ratios All crushers including impactors have limited reduction ratios. Due to the design there is a restricting in retention time for the material passing.
More
Theoretical modeling and experimental study on grinding force of ...
2022.12.30 The influence of structural parameters of the grinding wheel on grinding force is studied. The research work of this paper has important theoretical significance
More
Full article: Optimizing hammer mill performance through
2014.4.9 Typically, the metal bars swing freely from the drum, but fixed hammers are also common in hammer mill designs. Hammer mills are recognized as technology capable of finely grinding the greatest variety of materials Citation [3,13] and are noted for achieving high size-reduction ratios and yielding cubic-shaped particles Citation [14,15].
More
Determining the Bond Efficiency of industrial grinding circuits
The metal Bond ball mill is 30.5 cm inside diameter and. 30.5 cm inside length, with rounded corners. It is smooth except for the door hole used for charging. The grinding charge consists of 285 iron or steel balls (43 @ 36.8 mm diameter, 67 @ 29.7 mm diameter, 10 @. 25.4 mm diameter, 71 @ 19.1 mm diameter, and 94 @.
More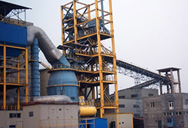
The Art of Milling - RETSCH
reduction. One way is to embrittle the sample in liquid nitrogen (N 2, LN) before grinding. At a temperature of -196°C even soft rubber becomes so hard and brittle that it can be ground without problems. Another possibility is to mix the sample with dry ice (CO 2). For indirect cooling, the grinding jar is placed in liquid nitrogen.
More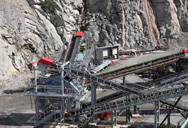
ideal reduction ratio grinding
كسارة تصادمية سلسلة pf. استيعاب jby التكنولوجيا المتقدمة من العالم، ونحن بحثها ومصممة كسارة تصادمية سلسلة pf ويمكن استخدامه للتعامل مع المواد
More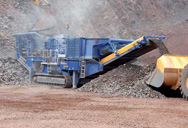
Profile Grinding Large Diameter Gears
2022.9.15 Illustration 14: Feedrate and reduction of burning risk Speed ratio qs. ... For this process, creepfeed grinding has shown to be the ideal solution.
More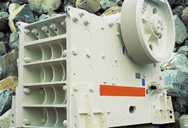
Ideal Reduction Ratio Grinding
Ideal Reduction Ratio Grinding 2021-09-10T10:09:17+00:00 CHAPTER 20: SIZE REDUCTION – EQUIPMENT FOR SIZE . p – Size reduction ratio • Coarse grinding has RRs below 8:1 • Fine grinding can exceed 100:1 • Grinding of coarse particles in which the increase in surface area per unit mass is relatively small, Kick's Law is a reasonable ...
More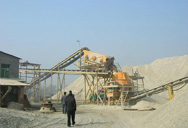
Particle Size Reduction Strategies BioCycle
2017.3.8 Particle size reduction is an important organic materials handling step that enhances the biological or chemical process by optimizing the particle surface area-to-volume ratio. Grinders, shredders and chippers are used for size reduction of wood wastes, yard trimmings, land-clearing debris, and in some cases, food waste.
More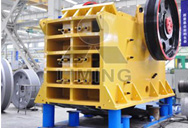
Theoretical modeling and experimental study on grinding force of ...
2022.12.30 Structured grinding wheel has obvious advantages in reducing grinding force, and the structural parameters of grinding wheel have important influence on the reduction of grinding force. In order to determine the influence law of structural parameters on grinding force, the following theoretical modeling and experimental research work are
More
Size reduction in feed technology and methods for determining ...
2020.3.1 Different grinding methods, including the use of roller mills, hammer mills, multicracker and multi-stage grinding were reviewed. Roller milling tends to produce a more uniform particle size distribution (PSD) and consumes less energy, whilst hammer mills have a greater grinding capacity and a higher reduction ratio compared to roller mill.
More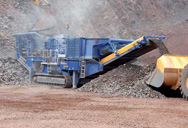
(PDF) Effect of circulating load and classification efficiency on
2014.10.20 PDF The ball mill is the most common ore grinding technology today, ... the highest reduction ratio for 50% passing size of feed and . product (F50/P50=RR50) and the nest product, as shown .
More
Rod Mill Feed Size - Grinding Classification Circuits
Bond would say ideal feed is 80% -16mm for a 13 W.I> material. If the Material has a higher W.I. there is a Bond formula to calculate the ideal feed size for a normal 1.5 to 1.8 L/D ratio rod mill. Dependent upon the Material and the Process! I seen feed as
More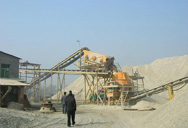
Dressing of Grinding Wheels SpringerLink
2010.10.18 Assuming a roller running in an ideal round movement, ... cracks were induced in the bond by the vibration, which in subsequent grinding operetion led to a reduction in the grinding ratio. ... the grinding ratios after conventional down dressing and ultrasonic assisted up dressing, with q d =+0.4 and q d =−0.4 respectively, are the ...
More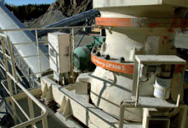
AENG 252 :: Lecture 08
Df / Dp – Size reduction ratio. Coarse grinding has RRs below 8:1; Fine grinding can exceed 100:1; Grinding of coarse particles in which the increase in surface area per unit mass is relatively small, Kick's Law is a
More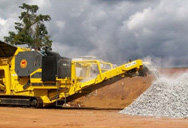
Grinding comparative analysis between different proportions of
2021.2.3 Grinding is an abrasion machining process designed to correct the geometric and surface imperfections of the workpieces. In this way, it is possible to provide parts with dimensional accuracy and excellent surface finish [1,2,3].In this machining, the material is removed through the contact between the abrasive grains of the wheel (tool of
More
Energy-Efficient Advanced Ultrafine Grinding of Particles Using
2023.7.10 The present literature review explores the energy-efficient ultrafine grinding of particles using stirred mills. The review provides an overview of the different techniques for size reduction and the impact of energy requirements on the choice of stirred mills. It also discusses the factors, including the design, operating parameters, and feed
More
Paper No. : 04 Paper Title : Unit Operations in Food processing
reduction ratios is below 8:1 and in fine grinding it is more than 100:1. Solids are broken mainly by four different ways, which are used in size-reduction machines. They are (1) compression, (2) impact, (3) attrition, or rubbing, and (4) cutting. Examples are a nutcracker, a sledge hammer, a file, and a pair of shears.
More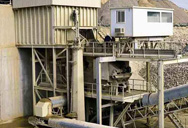
AMIT 135: Lesson 5 Crushing – Mining Mill Operator Training
The purpose of the primary crusher is to reduce the ROM ore to a size amenable for feeding the secondary crusher or the SAG mill grinding circuit. The ratio of reduction through a primary crusher can be up to about 8:1. Feed: ROM up to 1.5 m. Product: -300mm (for transport) to -200mm (for SAG mill) Feed Rate:
More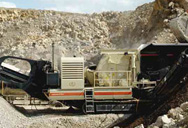
(PDF) Grinding characteristics, gravimetric properties and energy ...
2016.1.1 Size reduction ratio and grinding effectiveness of coriander seed were found decreased from 4.92 to 2.29 and 0.002 to 1.600 with the increase of moisture content, feed rate and grinder screen opening.
More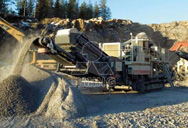
Analytical model of grinding force for ultrasonic-assisted grinding
2023.3.18 Ultrasonic-assisted machining of silicon carbide (SiC) ceramic matrix composites (CMCs) has the ability to decrease grinding force and improve processing quality. The machining process often produces large cutting forces which cause defects, such as delamination and burrs, due to the brittleness and high hardness of the material.
More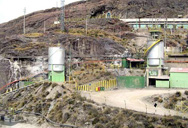
Ultrafine Grinding with Laboratory Ball Mills - Technology Networks
Colloidal grinding of aluminum oxide in the PM 100 Fig. 5: Grinding of alumina in water with 1 mm grinding balls (left) after 1 hour (blue) and after 4 hours (green) Fig. 6: Grinding of alumina with a 1 mm grinding ball (1 hour) and then with 0.1 mm balls (3 hours) in water [µm] Q 3 [%] percent by volume particle size 0,01 0,1 1 10 100 90 80 ...
More