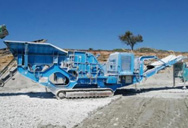
9 - Developments in the physical separation of iron ore: magnetic
2015.1.1 This chapter first introduces the principles and recent advances in magnetic separation technology in processing iron ore, followed by examples of flow sheets for magnetite and oxidized ores. 9.2. Principle of magnetic separation. 9.2.1.
More
Mineral and Technological Features of
2021.3.24 Obtaining high-quality concentrates with high iron content and low content of impurities from low-grade iron ores requires the
More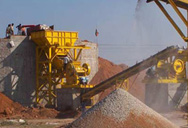
Magnetic separation: A review of principles, devices, and
Magnetic separation: A review of principles, devices, and applications Abstract: Conventional magnetic separation devices are widely used for the removal of tramp
More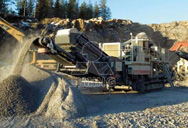
Developments in the physical separation of iron ore: magnetic ...
2015.1.1 Abstract. This chapter introduces the principle of how low-grade iron ores are upgraded to high-quality iron ore concentrates by magnetic separation. Magnetite
More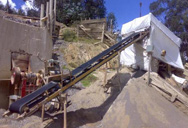
Characterisation and magnetic concentration of an iron ore
2019.1.1 Based on the ore characteristics (e.g. particle size, mineralogy and grade), gravity concentration (jig and Humphreys spiral), magnetic separation (low and high
More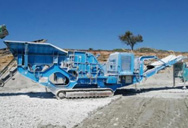
Particle-based characterization and classification to evaluate the ...
2022.8.1 Magnetic separation is a versatile technique widely used in the mining industry. Drum-type wet low-intensity magnetic separation (WLIMS) represents the
More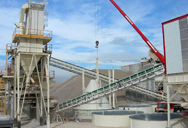
Measurement and Characterisation of Metallic Iron Particles
2020.9.18 Coal-based reduction followed by magnetic separation is a promising technology for processing refractory iron ores. Analysis of the size distribution of metallic
More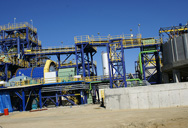
Improved iron recovery from low-grade iron ore by efficient
2022.8.1 At this time, iron minerals could be effectively recovered by a grinding and low-intensity magnetic separation process. Under the optimum roasting and magnetic
More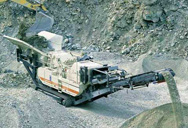
Developments in the physical separation of iron ore: magnetic ...
Preconcentration of Iron, Rare Earth, and Fluorite from Bayan Obo Ore Using Superconducting Magnetic Separation. Bayan Obo ore contains mainly bastnaesite,
More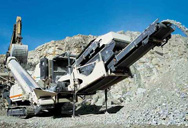
Magnetic separation studies for a low grade siliceous iron ore
2013.1.1 Magnetic separation is a simple, inexpensive, non-destructive and rapid means of concentrating iron-bearing minerals to nearly monomineralic levels, particularly
More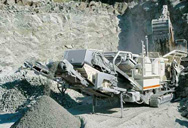
Magnetic Separation - Mining Fundamentals
Iron ores are usually subjected to the magnetic separation process, due to the high magnetic susceptibility of iron. Magnetic separation was first applied to the separation of wolframite from cassiterite. The first magnetic separator, invented by John Prince, consisted of two pairs of electromagnets with a feed belt running over them. Magnetic ...
More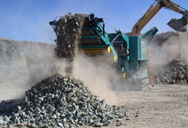
Recovery of magnetite-hematite concentrate from iron ore
To recover magnetite from tailings we used magnetic separation. Magnetic fraction contained 59.3% of Fe total and recovered 89% of Fe mag (table 2). Table 2. The results of the first stage of magnetic separation. Produc t Yield, % Fe content, % Fe recovery, % Tot Mag Hem Tot Mag Hem Magne-tic 18.0 59.3 55.5 2.4 52.5 89.0 8.2 Non-magne-tic
More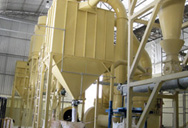
Magnetic Fluid Separation SpringerLink
2023.5.14 The magnetic fluid used in magnetic fluid separation is usually a strong electrolytic solution, paramagnetic solution, and ferrimagnetic colloidal suspension. It can be magnetized under the action of a magnetic field or the combination of a magnetic field and an electric field, which appears to be heavier. Heavier magnetic fluid density after ...
More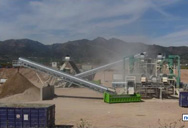
Maximizing the recovery of fine iron ore using magnetic separation
While flotation has a considerable capacity advantage over magnetic separation, the real advantage of magnetic separation over flotation in fine iron-ore beneficiation is that treatment of -10 µm iron ore is possible—in flotation, the feed is deslimed at 10 µm and the -10 µm stream is considered to be final tailings, even though there is often a significant
More
Minerals Free Full-Text A Novel Pneumatic Planar Magnetic
2020.8.27 In our previous studies, we investigated the performance of a novel pneumatic planar magnetic separator (PMS) for the dry beneficiation of a selected magnetite ore. In the present study, we have extended the studies on the PMS with the focus on investigating how various PMS processing flowsheet configurations influence its
More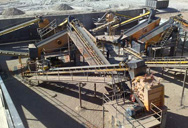
Magnetic Separation and Iron Ore Beneficiation – IspatGuru
2018.10.4 Magnetic separation is an old technique for the concentration of iron ores and for the removal of tramp iron. Since 1849, a number of patents on magnetic separation have been issued in USA, and texts of some of the patents before 1910 describe a variety of magnetic separators for mineral processing.
More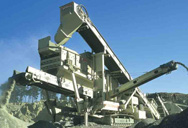
Optimized magnetic separation for efficient recovery of V and
2021.10.1 Moreover, the magnetic concentrates obtained by magnetic separation are composed of relatively smaller particles. However, an opposite trend was observed in the results of this study and was found to be similar to the results obtained by the magnetic separation of iron ore [40, 41].
More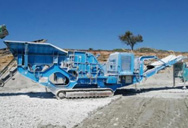
Semi-Smelting Reduction and Magnetic Separation for the
2019.4.9 This work presents a semi-smelting reduction and magnetic separation process for the recovery of iron and alumina slag from iron rich bauxite ore. The effect of the process parameters on the recovery rate of iron, maximum particle size of the iron nugget, and the Al2O3 content of the alumina slag was investigated and optimized. The
More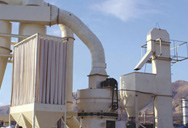
Separation of Iron and Zinc Values from Blast Furnace Dust
2023.7.8 Blast furnace dust is a typical secondary resource and hazardous waste generated in the process of iron and steel production, which often contains a large amount of metal resources such as iron and zinc. In order to recycle the iron, the separation of the zinc element is the first consideration. This study proposed a process of separating iron
More
Dry beneficiation of iron ore - Mineral Processing
In the beneficiation plant, high-pressure grinding rolls (HPGR) with downstream dry screening and dry magnetic separation are used as tertiary crushers to obtain a concentrate with 67 % iron content. In 2013, CITIC Pacific Mining had put into operation a first line from a total of six for the production of a magnetite iron ore concentrate in the
More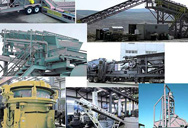
Minerals Free Full-Text Dry Permanent Magnetic
2022.9.9 Dry permanent magnetic separators have been widely used in the mineral and coal processing industries due to their simple operation and high separation efficiency. These tools not only discard
More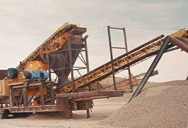
Fluidization Roasting Technology of Jingtieshan Iron
2022.10.21 This study presents a fluidization roasting technology for siderite-bearing iron ore without the use of carbon additives. Samples of Jingtieshan iron ore were subjected to fluidization magnetization
More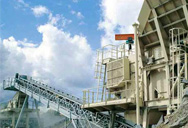
Characterisation and magnetic concentration of an iron ore
2019.1.1 Based on the ore characteristics (e.g. particle size, mineralogy and grade), gravity concentration (jig and Humphreys spiral), magnetic separation (low and high-field) and inverse cationic flotation (especially applied to pellet feeds) are used [3], [4]. It is estimated that for each tonne of beneficiated iron ore, 400 kg of tailings are produced.
More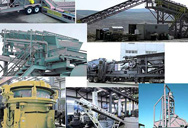
Recovery of rare earth elements minerals from iron oxide–silicate ...
2019.6.1 Magnetic separation has been an important technique usually employed in combination with other separation methods for the beneficiation and recovery of REE minerals (Jordens et al., 2016b, Moustafa and Abdelfattah, 2010; and Yang et al., 2015). Most of the REE processing plants in China use magnetic separation technique (Li and
More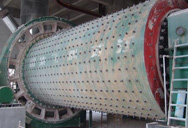
Particle-based characterization and classification to evaluate the ...
2022.8.1 Magnetic separation is a versatile technique widely used in the mining industry. Drum-type wet low-intensity magnetic separation (WLIMS) represents the backbone of the iron ore upgrading circuits since the mid 19 th century. However, it has been traditionally applied through guidelines that commonly disregard the ore properties
More
Novel Technology for Comprehensive Utilization of Low-Grade Iron
2022.4.18 In this study, a novel technology for the comprehensive utilization of low-grade iron ore is presented. For the iron ore with a Fe content of 24.91%, a pilot-scale study of pre-concentration, suspension magnetization roasting, grinding, and low-intensity magnetic separation was conducted, and an iron concentrate with a grade of 62.21%
More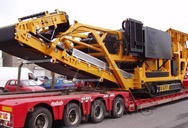
Recycling of steelmaking slag fines by weak magnetic separation
2014.11.1 The characterization of these steelmaking slag fines has led to the development of a technology of weak magnetic separation (between 200 G and 800 G of surface magnetic field strength) coupled with selective particle size screening to upgrade the steelmaking slag fines for producing clean products with high iron grades, low
More
Increasing efficiency of iron ore magnetic separation by using ...
enhance efficiency of iron ore magnetic separation by applying ultrasonic technologies. Thus, it is required to combine research results in the following directions: theoretical and practical research into iron ore magnetic separation; methods and means of operative control over physical-mechanical and chemical-
More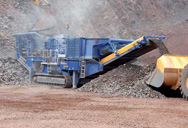
Application of magnetic separation to steelmaking slags
2006.1.1 To remove the metallic iron the slag is crushed to facilitate separation, using a rotating magnetic drum process (Alanyali et al., 2006; Ma and Houser, 2014 Matino et al., 2017; Bölükbaşı and Tufan, 2014). Crushing the slag to a smaller particle size as well as increasing the distance between the rotating drum and the blade.
More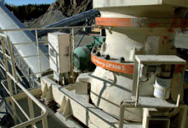
Measurement and Characterisation of Metallic Iron Particles
2020.9.18 Coal-based reduction followed by magnetic separation is a promising technology for processing refractory iron ores. Analysis of the size distribution of metallic iron particles is an effective approach for exploring the mechanisms of coal-based reduction. As metallic iron particles exhibit very complex shapes compared with nature ores,
More