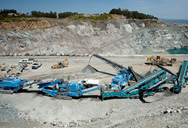
Surface modification of silica powder by mild ball milling
2022.11.5 Surface modification of silica particles without a catalyst or solvent was performed using ball milling, and the effects of the amount of HTMS used as a modifier,
More
Comparative Study on Improving the Ball Mill Process Parameters ...
2021.2.19 The optimum process parameters setting concluded that balls to powder weight ratio are 20:1, the optimum ball mill working capacity is 2 L while the optimum
More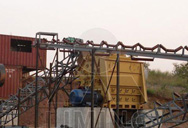
Parameter Optimization of Ball Milling Process for Silica
2019.3.1 The three main parameters applied in this study are Ball to Powder weight Ratio (BPR), time milling process, and rotational speed (rpm). The materials used in the
More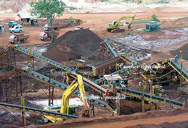
Enhanced hydrogen generation in low-range acidic solutions using ...
2023.10.25 This study presents a novel approach to boost the speed of hydrolysis reactions by utilizing Mg 2 NiH 4 powder. The approach involves ball milling with NaCl
More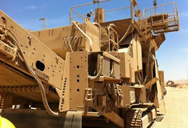
Surface modification of silica powder by mild ball milling
2022.11.5 In this study, a catalyst- and solvent-free ball mill treatment was conducted to modify the silica powders by the mild ball milling process as the simple and the low
More
Surface modification of silica powder by mild ball milling
2022.7.1 Abstract. Surface modification of silica particles without a catalyst or solvent was performed using mild ball milling. The effects of the amount of the modifier,
More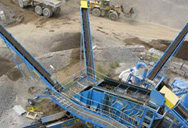
Influence of mechanical properties on milling of amorphous and ...
2021.10.1 Milling of silicates in two forms, amorphous and crystalline, is analysed. • Breakability index, i.e. hardness over toughness squared, is characterised. • It describes
More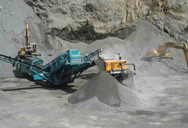
Evolution of grinding energy and particle size during dry ball
silica sand as a model material in an oscillatory ball mill for a broad range of the values of vibration frequency and amount of powder. We show that the re-agglomeration of fine
More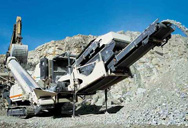
Surface modification of silica powder by mild ball milling
2022.7.1 Surface modification of silica powder by mild ball milling. Yuki Nakashima, M. Fukushima, Hideki Hyuga. Published in Colloids and Surfaces A 1 July 2022.
More
The effect of alumina contamination from the ball-milling of fused ...
2011.6.1 The contamination from ball milling has been shown to affect high temperature properties in some ceramic materials, 5 but not for silica based ceramics
More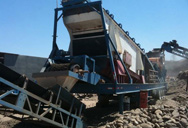
Effects of Fused Silica Addition on Thermal Expansion, Density,
2022.5.12 Effects of Fused Silica Addition on Thermal Expansion, Density, and Hardness of Alumix-231 Based Composites. ... Two zirconia balls—each with a diameter of 10 mm and a mass of 6.04 g—were added, keeping the ball to powder ratio 2:1. Ball milling was carried out in a SPEX 8000M Mixer/Mill ball mill for 20 min, ...
More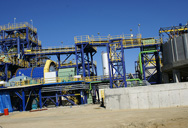
2 Solidification of Turbine Blades - MDPI
fused silica and 40 wt% zircon. Porous silica-based ceramic cores were prepared by using ceramic injection molding. After a series of procedures, such as mixing, ball milling, adding adhesive, and drying, the green bodies were obtained. The sintered samples were subsequently subjected to heat
More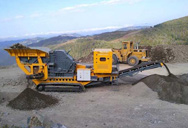
The effect of alumina contamination from the ball-milling of fused ...
2011.6.1 The supplied powders were mixed to create a specific particle size distribution (PSD), within ±5% for the D 90 and D 10 and ±10% for the D 50, to avoid significant PSD effects.The properties of these mixed powders are shown in Table 1.The final alumina amounts present in each material were then a consequence of meeting this
More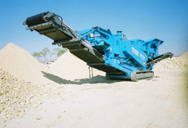
ball for milling fused silica powder

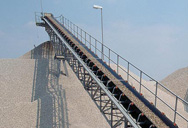
Influence of mechanical properties on milling of amorphous and ...
2021.10.1 Environment relative humidity and temperature could influence the milling characteristics if the milled powder is hygroscopic. Water vapour adsorption of the silicate samples was investigated using dynamic ... Stainless steel ball and capsule Fused silica Quartzite; Density (kg/m 3) 7800: 2190: 2780: Young's modulus (GPa) 190: 83.1: ...
More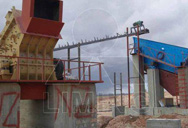
Fused Silica – Sibelco
Introduction. Fused silica is an angular “shaped” silica produced by grinding and milling high purity silica/quartz. Fused silica therefore has the same intrinsic properties as any other silica. Its chemical formula is SiO2. At Sibelco high purity quartz is being used to make fused silica. Quartz (silica, SiO2) is the core mineral within ...
More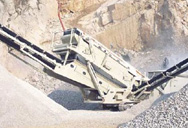
Fused silica powder-Sinoteng Silica Materials Technology
SINO-RG series Fused silica powder is made of the high purity crystal silica materials by electrically fusing to amorphous silica and then by sorting、ball milling、air classifying etc processes to amorphous silica powder material.. Product Features: Superior heat resistance chemical performance; Low Na+, Cl-, E/C content; High purity low
More
Thermal Field Modeling and Experimental Analysis in Laser
2020.8.29 Fused silica, a high-strength brittle material, is widely used in optical, aerospace, and laser industries. However, a high-efficiency and high-quality machining method for fused silica is widespread demand in the industry. In this paper, based on the three-dimensional cylindrical transient heat transfer model and cutting experiments, the
More
Influence of mechanical properties on milling of amorphous and ...
Influence of Mechanical Properties on Milling of Amorphous and Crystalline Silica-Based Solids Siwarote Sirilucka, Umair Zafara, Colin Harea,1, Ali Hassanpoura, Nadja T. Lönnrothb,2, Navin Venugopalb, Martin J. Murtaghb,3, Mojtaba Ghadiria aSchool of Chemical and Process Engineering, University of Leeds, LS2 9JT, UK bCorning
More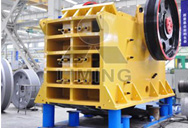
Ball milling preparation and characterization of poly (ether ether ...
2011.2.15 PEEK/SiO 2 nanocomposite powder was prepared by using a high energy ball milling technique and characterized in the terms of morphology, particle size distribution and crystalline structure of PEEK/SiO 2 during milling. The effects of milling process and surface pretreatment of silica nanoparticles on particle dispersion in matrix
More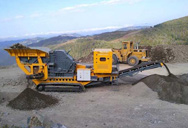
Mingjun CHEN Professor (Full) PhD Harbin Institute
Point defects with different species are concentrated on most mechanically machined fused silica ... powder spreading, and ... Using micro-ball end milling cutters to repair and remove ...
More
mill/sbm milling machine for high purity fused silica.md at
You can not select more than 25 topics Topics must start with a letter or number, can include dashes ('-') and can be up to 35 characters long.
More
Research on laser-assisted micro-milling of fused silica
Experiment used a 3-axis micro milling machine platform (Fig. 5) in which silica workpiece was xed on the top of Kistler 9256C dynamometer, and the fused silica plates were used as the workpiece. φ 0.5 mm Magfor 8527-G diamond-coated ball end mills with 3-μm edge radius were used as the tools. The spindle speed was 30,000 rpm
More
Influence of Solid Loading and Ratio of Monomers on Mechanical
2018.12.15 Mishra S et al (2010) Structure–property correlation in cellular silica processed through hydrophobized fused silica powder for aerospace application. J Alloys Compd 504:76–82. Article CAS Google Scholar Wan W et al (2013) Gelcasting of fused silica glass using a low-toxicity monomer ... the ball-milling of fused silica on the ...
More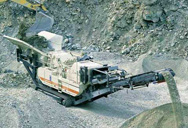
Facile, fast, and green preparation of high-purity and quality silica ...
2023.1.12 1 kg of synthesized pure silica powder and 20 kg of silica balls were placed in the handmade mill. The rotating speed, powder-to-ball ratio, milling time, air blowing speed, and air sucking speed were adjusted at 240 rpm, 1:20 kg, 12 h, 7.5 km/h, and 50 m 3 /h, respectively. The DLS results are illustrated in Fig. 7.
More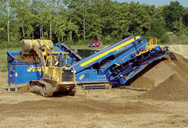
Surface modification of silica powder by mild ball milling
2022.11.5 Fig. 3 shows a typical TG-DTA curve of the silica powder modified by 0.5 ml of HTMS after ball milling for 24 h. The DTA curve showed two peaks at approximately 130 and 300 °C. The first endothermic peak corresponds to the loss of physically adsorbed and/or hydrogen-bonded water from the silica powder [22].The second exothermic peak
More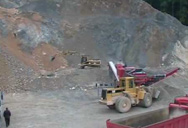
2" JGS1 Ultraviolet (UV) Grade Fused Silica Wafer, 500 um, DSP,
UV grade Fused Silica (JGS1) is synthetic amorphous silicon dioxide of extremely high purity. It exhibits a broad OH absorption band between 2600 and 2800 nm. JGS1 Ultraviolet Grade Fused Silica is comparable to Suprasil 1 and 2 (Heraeus), Spectrosil A and B (Saint-Gobain) and Corning 7940 (Corning), Dynasil 1100 and 4100 (Dynasil).
More
Effect of Milling Time on the Rheology of Highly Loaded Aqueous-Fused
Milling/mixing is an important step for all slurry-based ce- (B) Particle Surface Characterization: To examine the ramic processing during which the powder experiences the fol- extent of development of surface hydroxide on fused silica par- lowing changes: breakage of agglomerates into individual ticle surfaces with milling time, FTIR was
More
Preparation of high purity, low water content fused silica glass
2001.12.1 There are several methods to prepare silica based materials, i.e., thermal decomposition technique, flame spray pyrolysis, chemical vapor deposition, micro emulsion, ball milling, vapor-phase ...
More
The effect of alumina contamination from the ball-milling of fused ...
DOI: 10.1016/J.JEURCERAMSOC.2010.12.016 Corpus ID: 136472684; The effect of alumina contamination from the ball-milling of fused silica on the high temperature properties of injection moulded silica ceramic components
MoreRelated Information:
- trituracioacuten aumenta la concentracioacuten de mineral de hierro
- molino de bolas precios compra en México
- rubber tyred mobile crusher sales
- moagem de diamante pengxing
- disposicion de la planta de trituracion de agregados
- Quebradora de oro en Guanajuato
- trituradoras de mandíbula agregados en la india
- molino para roca en venta
- Supresor Polvo Riego
- maquinas trituradoras de piedra medellin
- triturador industrial de 15 hp modelo 570x620
- plancha de goma cordoba
- cómo usan las muelas en el molino de cemento
- mineria procesamiento de la plata proveedor de equipos
- mantenimientos en los bancos de moliendas
- Trituradora de hojas colombia
- maquinaria utilizada en la fabricación de cemento pdf
- Molino de plomo en mexico
- trituración de piedra caliza triturada
- Rocas de cantera y planta de arena de río
- fabricantes de moinhos de bola para ceramicas
- tamantildeo de bolas en molinos de bolas
- de trituradoras parker bolivia
- trituradoras piedra en baja california
- relatório de projeto da planta de britagem de 200 tph