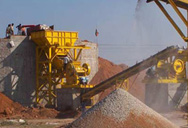
Comminution and classification technologies of iron ore
2022.1.1 Most of the high-grade hematite iron ores are typically subjected to simple dry processes of crushing and classification to meet the size specifications required for direct shipping ore (DSO). This involves multistages of crushing and screening to obtain
More
Crushing characteristics and performance evaluation of iron ore in
2023.12.1 In this study, the crushing process of spherical iron ore particles, constructed by an Apollonian sphere packing (ASP) method, was numerically reproduced
More
Why is there a need to crush iron ore bearing rock? - LinkedIn
2023.10.11 The reasons for crushing the ore-bearing rock include: Size Reduction: Iron ore typically exists in large, hard and unwieldy chunks. Crushing the ore helps
More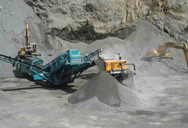
Iron ore beneficiation: an overview - ScienceDirect
2023.1.1 Dry processing of iron ore: In dry processing of iron ore, ROM is generally crushed below 40 mm through three-stage crushing and thus segregated by screening
More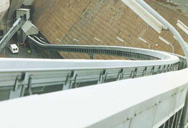
(PDF) SIZE REDUCTION BY CRUSHING METHODS
2017.3.4 Crushing of ore and minerals. ... INVESTIGATING THE REASONS FOR QUARRY SHUT-DOWN IN PLATEAU ... 9.00% of Iron
More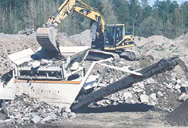
The six main steps of iron ore processing - Multotec
Six steps to process iron ore. 1. Screening. We recommend that you begin by screening the iron ore to separate fine particles below the crusher’s CSS before the crushing stage. A
More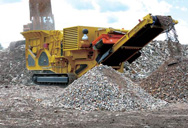
Role of pre-crusher stockpiling for grade control in
2013.12.1 Role of pre-crusher stockpiling for grade control in iron ore mining Authors: K. Jupp T. J. Howard Jim Everett University of Western Australia Abstract Pre-crusher stockpiles are designed...
More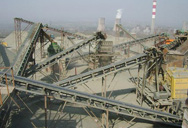
Reduction of Fragment Size from Mining to Mineral Processing: A
2022.10.4 According to the study by Norgate and Haque mentioned earlier, crushing and grinding made a contribution of about 21% and 47%, respectively, to the total
More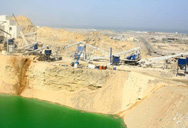
Iron Mining Process - Minnesota Iron
Crushing At the processing plant, the taconite is crushed into very small pieces by rock crushing machines. The crushers keep crushing the rock until it is the size of a marble. The rock is mixed with water and ground in
More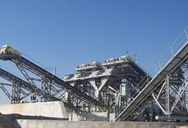
A Mine-to-Crusher Model to Minimize Costs at a
2022.8.18 This paper presents an economic analysis of a mine-to-crusher model to estimate and minimize the operating expenses of an open-pit iron mine located in northern Brazil. The activities at this truckless
More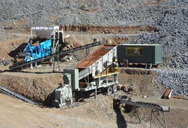
A Mine-to-Crusher Model to Minimize Costs at a
2022.8.18 Innovation has an important role in improving the productivity, safety and sustainability of mining operations. Historically, ore transport was done by diesel trucks, but with the commitment to reduce
More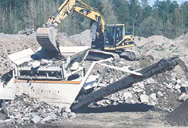
Roller crushers in iron mining, how does the degradation of
2021.4.1 In the present work, a tribological study was carried out on concave and mantle linings of cone crushers used in the fourth-stage crushing process of an iron ore processing plant. Initially, an analysis of the characteristics over the lifetime of the applied coatings was carried out, and samples of the parts that suffered the most critical wear
More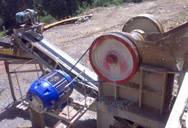
reasons for crushing iron ore
Rainttree Mining. Mining Equipments Solution Stone Crushing Sand Making Ore Processing Grinding Plant Construction Building Material Home Mine 2 reason for crushing sieving the mineral particles 2 reason for crushing sieving the mineral particles More Details Raintree The Wealth Of The Rainforest 2020 5 31Raintree advocates the
More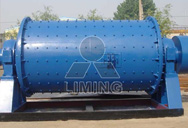
Top 6 Steps of Iron Ore Processing Australian Mining Services
2023.9.18 Before crushing, we advise screening the iron ore to remove small particles smaller than the crusher’s CSS. The tiny particles are sent to a static screen for crushing. This process keeps the crusher from being overloaded and boosts its effectiveness. Fine particles reduce the efficiency of the crusher and increase the power
More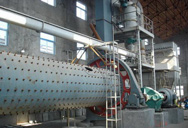
China consortium wins rights to develop Guinea iron ore deposit
2019.12.2 Simply sign up to the Mining myFT Digest -- delivered directly to your inbox. The China-backed consortium that has secured rights to develop half of the huge Simandou iron ore deposit in Guinea ...
More
Low grade Iron Ore Beneficiation and the Process of Jigging
2018.9.25 The reasons for choosing jigging for the iron ore beneficiation over other processes include (i) relatively easy separation, (ii) beneficial trade-off between operating cost and reduced yield relative to dense medium processes, (iii) ability to treat ores requiring cut densities higher than a density of 4.0, and (iv) physical characteristics of the ore
More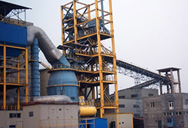
Roller crushers in iron mining, how does the degradation of
2021.4.1 1. Introduction. Abrasion and impact-abrasion conditions are one of the major reasons for crushing wear parts deterioration. Although the abrasive wear resistance of steel tends to increases with the hardness, the synergic performance between abrasion wear and impact-abrasion wear depends on a combination of hardness, toughness,
More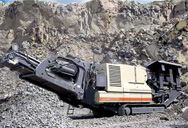
Crushing characteristics and performance evaluation of iron ore
2023.12.1 1. Introduction. Due to the decreasing reserves of high-grade iron ore and secondary resources used for steelmaking, it has become an important research and development area to improve the grade of iron ore through crushing (Gul et al., 2014).The quality of iron ore crushing directly affects the performance of pellets and sinter, so as
More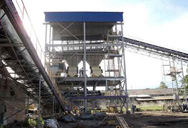
Common Iron Ore Crushing and Screening Process
2021.6.25 When dealing with argillaceous iron ore with high water content, or when restricted by terrain conditions, a three-stage open-circuit crushing and rod mill crushing process is sometimes used. That is to relax the particle size of the finely crushed product to 25~30mm, and add a rod mill for fine crushing, which is equivalent to a four-stage open
More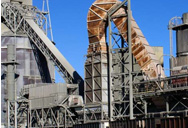
(PDF) SIZE REDUCTION BY CRUSHING METHODS - ResearchGate
2017.3.4 Crushing of ore and minerals. ... INVESTIGATING THE REASONS FOR QUARRY SHUT-DOWN IN PLATEAU ... 9.00% of Iron (II) oxide (Fe2O3) while samples from Pit 5 to Pit 10 in the mine site at Bisichi ...
More
Environmental Code of Practice for metal mines:
Major steps in ore processing include grinding and crushing, chemical/physical separation and dewatering. Grinding and Crushing. Grinding and crushing of ore is undertaken to physically liberate
More
Why Should Iron Ore be Crushed First in Iron Ore Beneficiation
2021.6.21 The crushing and grinding of iron ore are responsible for the task of providing selected materials for the subsequent beneficiation process. Henan Forui Machinery Technology Co., Ltd. ... Why Should Iron Ore be Crushed First in Iron Ore Beneficiation. June 21, 2021
More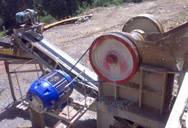
Iron ore beneficiation: an overview - ScienceDirect
2023.1.1 In this iron ore deposits (mentioned above), the iron ore was crushed using three stages of crushing to a size below 32 mm and then was subjected to beneficiation. Primary and secondary crushing was done by gyratory crushers. For sticky iron ores with a high clay content, primary and secondary sizers were also used instead of gyratory
More
Iron ore mining and dressing - tec-science
2018.6.21 An ironworks (or iron works) is an industrial plant for the production of steel from iron ores! Before the iron ores can be fed to the ironworks, they must first be mined (ore extraction) and specially processed for the blast furnace process (ore processing). These process steps are described in more detail in the following sections.
More
Collections: Iron, How Did They Make It? Part I, Mining
2020.9.18 One distinction here is between bog iron and iron in ore deposits. Bog iron is formed when ground-water picks up iron from iron-ore deposits, where that iron is then oxidized under acidic conditions to form chunks of iron minerals (goethite, magnetite, hematite, etc.), typically in smallish chunks.
More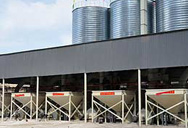
The screening process: a vital component of the crushing circuit
2022.1.20 This is where optimisation of screening comes into play. "There are two ways of looking at it: there's screening prior to crushing, and then screening after crushing. We want to make sure that we've got the whole process balanced. We're not just looking at getting the crusher working at 100% or a screen working at 100% efficiency.
More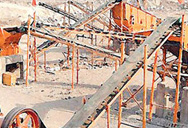
25.1 Exploration: Finding minerals Mining of mineral resources
We will discuss the extraction of iron from iron ore as an example. Extraction of iron. Iron atoms are found in the compounds FeO, Fe 2 O 3 and Fe 3 O 4 and in rocks like haematite and magnetite. South Africa is the seventh largest producer of iron ore in the world. Iron has been mined in South Africa for thousands of years.
More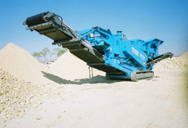
Effect of Binders on the Crushing Strength of Ferro-Coke - PMC
2021.2.10 In this paper, the addition amount of iron ore powder (10%, 20%, 30%, 40%, 50%) were used to reveal the effect of iron power amount on the crushing strength of ferro-coke. Then four types of binders (phenolic resin, silicon metal powder, corn starch, and coal tar pitch) were added into the coal to test their effect on the cold and hot crushing ...
More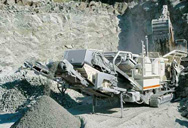
reasons for crushing iron ore
Apr 03, 2015 blasting, crushing, Hematite, Iron ore, magnetite, open pit mining, screening, underground mining, Understanding Iron Ores and Mining of Iron Ore. Iron (Fe) is an abundant and a widely distributed element in the in the crust of the earth, constituting on an average ranging from 2 % to 3 % in sedimentary rocks to 8.5 % in basalt and gabbro.
More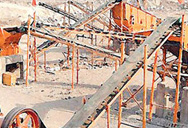
(PDF) Ore crushing in the high-pressure roller-press as a
2021.2.19 The results of improving ore crushing in a high-pressure ... 500/15-1000 roller-press using 40-0 mm oxidized iron ore . ... corresponds to the fact that due to random reasons the maxi-mum ...
More