
The six main steps of iron ore processing - Multotec
1. Screening We recommend that you begin by screening the iron ore to separate fine particles below the crusher’s CSS before the crushing stage. A static screen is used to
More
Comminution and classification technologies of iron ore
2022.1.1 This chapter reviews current iron ore comminution and classification technologies and presents some examples of flowsheets from existing operations. New
More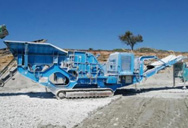
Iron Ore production in the Pilbara
Iron Ore production in the Pilbara. Activities involved in finding, mining and processing iron ore at our Pilbara operations have been simplified in the following diagram. Rio Tinto
More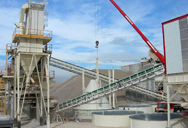
Physical Beneficiation - an overview ScienceDirect Topics
The first step of physical beneficiation is crushing and grinding the iron ore to its liberation size, the maximum size where individual particles of gangue are separated from the iron
More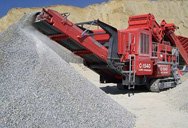
11.23 Taconite Ore Processing
ore concentrate. A simplified flow diagram of these processing steps is shown in Figure 11.23-1. Liberation is the first step in processing crude taconite ore and consists mostly
More
How to design an iron ore processing facility with crushing and ...
1. Assess the physical properties of the ore, such as grade, mineralogy, hardness and variations within the deposit, as this will determine the process route. 2. Design and
More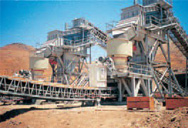
Crushing Circuit - an overview ScienceDirect Topics
Flow sheet of typical iron ore crushing and grinding circuit. Jaw and gyratory crushers are used for initial size reduction to convert big rocks into small stones. This is generally
More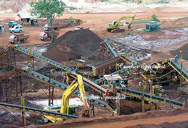
Iron Ore Processing, General SpringerLink
2022.10.20 Making iron and steel from iron ore requires a long process of mining, crushing, separating, concentrating, mixing, agglomeration (sintering and pelletizing),
More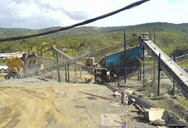
Research into the crushing and grinding processes of iron ore with
1 Introduction The effectiveness of simultaneous effect of mechanical load and electric field of ultra-high frequency (UHF) in the process of iron ore crushing is substantiated in
More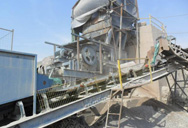
Iron Ore Processing, General SpringerLink
2022.10.20 Iron ore handling, which may account for 20–50% of the total delivered cost of raw materials, covers the processes of transportation, storage, feeding, and washing of the ore en route to or during its various stages of treatment in the mill.. Since the physical state of iron ores in situ may range from friable, or even sandy materials, to monolithic
More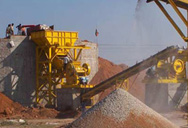
Iron Mining Process Equipment Flow Cases - JXSC
Iron Ore Mining Process. 1. Large raw iron ore for primary crushing are fed into the jaw crusher by Plate feeder and are reduced to 8 inches or smaller. After first crushing, the material will be transferred to cone crusher by belt conveyor for secondary crushing; the crushed iron ore stone will then transferred to vibrating screen for ...
More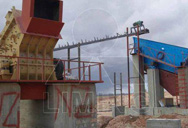
Mining of Iron Ores – IspatGuru
2014.3.14 Fig 3 Types of processing ores. The wet processing (Fig 4) is normally practiced for low / medium grade (60 % to 63 % Fe) hematite iron ore. The wet process consists of multi-stage crushing followed by
More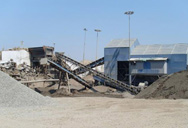
12.5 Iron And Steel Production - US EPA
12.5.1.2 Iron Production - Iron is produced in blast furnaces by the reduction of iron bearing materials with a hot gas. The large, refractory lined furnace is charged through its top with iron as ore, pellets, and/or sinter; flux as limestone, dolomite, and sinter; and coke for fuel. Iron oxides, coke and fluxes react with the
More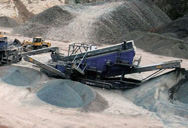
Minerals Free Full-Text An Evaluation on the Impact of Ore
2022.2.17 For example, the effect of ore crushing on the shovels of the Gol-e-Gohar iron ore mine was presented with a mathematical model to determine their production levels. This model was obtained using data that differed from the shovels’ production levels in different blasting patterns with different fragmentation results.
More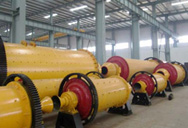
sbm/sbm crushing plant cement industry flowchart.md at master
You've already forked sbm 0 Code Issues Pull Requests Packages Projects Releases Wiki Activity
More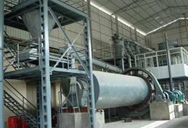
Crushing Circuit - an overview ScienceDirect Topics
The first step of physical beneficiation is crushing and grinding the iron ore to its liberation size, the maximum size where individual particles of gangue are separated from the iron minerals. A flow sheet of a typical iron ore crushing and grinding circuit is shown in Figure 1.2.2 (based on Ref. [ 4 ]). This type of flow sheet is usually ...
More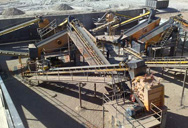
Executive Summary
Iron Ore Crushing Plant --- 17,95,200 TPA 17,95,200 TPA 2. DRI (Sponge Iron) 1,15,500 TPA (1X350 TPD) 8,08,500 TPA (7X350 TPD) 9,24,000 TPA 3 ... The process flow diagrams are shown below:- Figure : Flow chart for Iron Ore Pelletization . Executive Summary 10 Fludized bed gasifier
More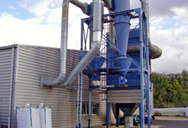
Process flow sheet for Pelletization using wet grinding process
Download scientific diagram Process flow sheet for Pelletization using wet grinding process from publication: Iron Ore Pelletization Technology and its Environmental Impact Assessment in Eastern ...
More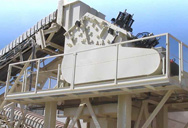
flow diagram of ore processing
concentrating the ore by separating the particles from the waste material (gangue), and pelletizing the iron ore concentrate. A simplified flow diagram of these processing steps is shown in Figure 11.23-1.
More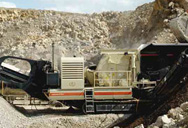
Nuclear fuel cycle' Extractingg uranium from its ores
Extractingg uranium from its ores by D.C. Seidel* The development of the uranium mining and ore processing industry is unique. In the space of a little less than 10 years it grew from almost nothing to a major hydrometallurgical industry, no other ore-processing operation has developed so quickly. Not only did the
More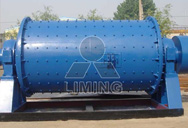
(PDF) Iron Ore Pelletizing Process: An Overview
2018.7.11 Bentonite, an inorganic binder, has been the main binder used in the iron ore pelletizing. process since the beginning of pellet production in the 1950s. Bentonite promotes the forma-. tion of ...
More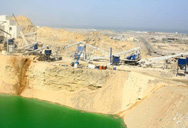
Iron Ore Pelletizing Process: An Overview - IntechOpen
The iron ore pelletizing process consists of three main steps: Pelletizing feed preparation and mixing: the raw material (iron ore concentrate, additives —anthracite, dolomite—and binders are prepared in terms of particle size and chemical specifications, dosed, and mixed together to feed the pelletizing process;
More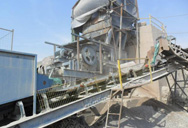
Effect of Iron Ore Pellet Size on Metallurgical Properties - MDPI
2022.2.10 In this study, the effect of pellet size on the metallurgical properties of magnesia iron ore pellets was investigated. Reduction and softening behaviour, cold crushing strength and low-temperature reduction-disintegration were determined separately for pellets sized 8–10 mm, 10–12.7 mm, 12.7–16 mm, and 16–20 mm.
More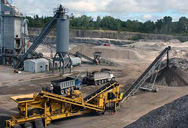
Dry beneficiation of iron ore - Mineral Processing
The haematite ore in South Africa is processed in a dry process to a HQ lump ore with 64 % iron content and a sintered fine ore with 63.5 % iron content. For fine ore beneficiation, wet processes are used. Capacity at the Minas Rio is to be increased from 26.5 Mta capacity to 28 Mta in the forthcoming years.
More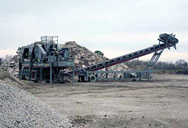
Iron Ore - an overview ScienceDirect Topics
Iron ore minerals, particularly hematite and goethite, are beneficiated by a combination of size fraction, preconcentration, and flotation in stages (Fig. 13.45).Iron ore requires removal of silicate impurities of a finer size by flotation for higher-grade products of +60% Fe. ROM ore at 400–600 mm is fed to a primary crusher with product set at –40 mm.
More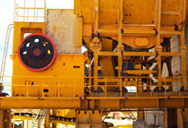
iron ore refinery processing plant Mining Quarry Plant
2013.4.21 Vibrating feeder is the machine used to feed iron ore evenly to iron ore crushing and grinding machine in iron ore processing plant. Iron – Wikipedia, ... Gold Ore Refining Process Flow Chart,Gold Extraction Process diagram flow chart of magnetite iron ore processing plant.
More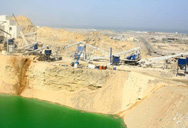
11.24 Metallic Minerals Processing - US EPA
11.24.1 Process Description1-6. Metallic mineral processing typically involves the mining of ore from either open pit or underground mines; the crushing and grinding of ore; the separation of valuable minerals from matrix rock through various concentration steps; and at some operations, the drying, calcining, or pelletizing of concentrates to ...
More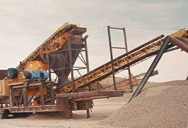
(PDF) Beneficiation and flowsheet development of a low grade iron ore
2020.12.1 In the present study a detailed characterization followed by beneficiation of low grade iron ore was studied. The Run of Mine (R.O.M) sample assayed 21.91 % Fe, which is very low grade in nature ...
More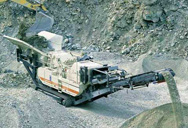
INTRODUCTION TO MINERAL PROCESSING FLOWSHEET DESIGN
CRUSHING PLANT DESIGN The number of crushing stages necessary to reduce ore to the proper size varies with the type of ore. Hard ores like gold, iron, and molybdenum ores, may require as much as a tertiary crushing. To design a good crushing plant one has to follow these three steps: 1. Crusher selection 2. Crusher layout and 3.
More