
Optimization of a fully air-swept dry grinding cement raw meal
2015.4.1 The ball mill was simulated as a single compartment mill by eliminating the mill length of 2.935 m which was used in drying stage, such that the full length (L = 9.87
More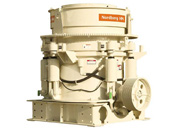
Optimization of a fully air-swept dry grinding cement raw meal
2015.4.1 In this study, production capacity of a fully air-swept dry grinding raw meal ball mill circuit was evaluated by modelling the mill using the perfect mixing modelling
More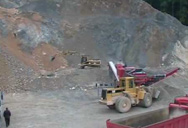
Ball Mill - an overview ScienceDirect Topics
For more than 50 years vertical mills have been the mill of choice for grinding raw materials into raw meal. More recently they have become widely used for cement
More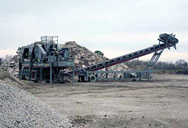
Fives Grinding in ball mills with FCB B-mill - Fives Group
Fives' FCB B-mill goes beyond the traditional ball mill, which is used for grinding raw materials, cement, solid fuels and minerals. The FCB B-mill can grind products at high
More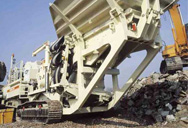
Optimization of a fully air-swept dry grinding cement raw meal
2015.4.1 Optimization of a fully air-swept dry grinding cement raw meal ball mill closed circuit capacity with the aid of simulation DOI: Authors: Ömürden Genç Mugla
More
Rawmill - Wikipedia
Rawmill. A medium-sized dry process roller mill. A raw mill is the equipment used to grind raw materials into "rawmix" during the manufacture of cement. Rawmix is then fed to a
More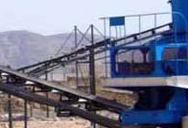
Minerals Free Full-Text Analysis and Optimization of
2022.1.23 As far as we know, there are few multi-objective optimization studies on energy consumption and grinding energy efficiency for a VRM. There are usually four kinds of VRMs in the cement
More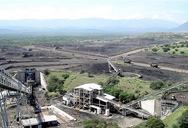
Review on vertical roller mill in cement industry its performance ...
2021.1.1 Raw meal drying, grinding, and homogenization. Raw mix, high grade limestone, sand and iron ore are transported from their bins to raw mills for drying and
More
Efficient machine learning model to predict fineness, in a vertical
2023.3.1 In addition to raw meal and cement clinker grinding, vertical roller mill is also used for grinding phosphate, chalk, etc. On the industrial scale, change in material
More
Optimization of a fully air-swept dry grinding cement raw meal
Optimization of a fully air-swept dry grinding cement raw meal ball mill closed circuit capacity with the aid of simulation @article{Gen2015OptimizationOA, title={Optimization
More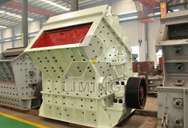
Raw Meal Ball Mill
Raw material ball mill, also called raw meal mill, is important grinding equipment in cement production process. After being crushed, the raw meal enters the raw material mill. The raw meal is grinded into fine powder by the motion and squeezing of steel balls. The raw material mill manufactured by Chaeng (Great Wall Machinery) can meet the raw ...
More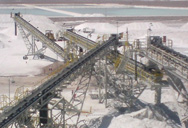
Review on vertical roller mill in cement industry its performance ...
2021.1.1 Raw meal drying, grinding, and homogenization. Raw mix, high grade limestone, sand and iron ore are transported from their bins to raw mills for drying and further fine grinding. The raw mill is either a Ball mill with two chambers or Vertical roller mill with inbuilt classifier.
More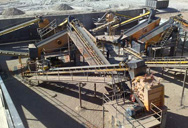
Optimization of a fully air-swept dry grinding cement raw meal ball ...
2015.4.1 Introduction. Air-swept raw meal ball mills introduced by the cement mill manufacturers F.L.Smidth ® (Smidth, 2002), Polysius ® (Polysius, 2002) and KHD Humboldt Wedag® are the most commonly used ones. KHD Humboldt Wedag® manufactured fully air-swept raw meal mills which have two compartments used for drying and grinding
More
From raw materials Extracting raw materials Raw material
The desired raw mix of crushed raw material and the additional components required for the type of cement, e.g. silica sand and iron ore, is prepared using metering devices. Roller grinding mills and ball mills grind the mixture to a fine powder at the same time as drying it, before it is conveyed to the raw meal silos for further homogenisation.
More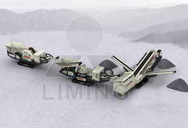
Vertical Raw Mill for Cement Raw Meal Grinding in Cement
So the vertical raw mill particularly suitable for the grinding of cement raw meal in cement factory. The vertical raw mill in cement industry has been applied in the field of medicine and food because of its high grinding efficiency, can dry up to 10% moisture materials and energy saving of 20% – 30% compared with ball mill of the same scale.
More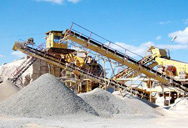
Ball size distribution for the maximum production of a
2015.11.1 Section snippets Review of grinding and ball wear models. Austin et al. [3] proposed a grinding circuit model (Eq. (1)), which comprises a mathematical description of a continuous grinding in open circuit from which the general size-mass balance equation applicable to the particle size reduction process was derived: p i = w i τ = ∑ j = 1 i d i, j. f
More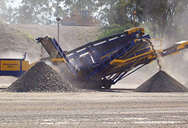
Cement grinding Vertical roller mills versus ball mills
For a ball mill grinding OPC to a fineness of 3200 to 3600 cm2/g (Blaine) the cost of wear parts (ball, liners and mill internals) is typically 0.15-0.20 EUR per ton of cement. For an OK mill grinding a similar product, the cost of wear parts depends on the maintenance procedures, i.e. whether hardfacing is applied.
More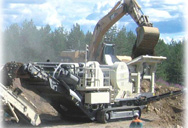
Ball mill - Wikipedia
A ball mill, a type of grinder, is a cylindrical device used in grinding (or mixing) materials like ores, chemicals, ceramic raw materials and paints. Ball mills rotate around a horizontal axis, partially filled with the material to be ground plus the grinding medium. Different materials are used as media, including ceramic balls, flint pebbles ...
More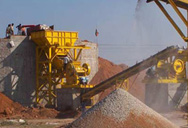
Optimization of a fully air-swept dry grinding cement raw meal ball ...
2015.4.1 Optimization of a fully air-swept dry grinding cement raw meal ball mill closed circuit capacity with the aid of simulation April 2015 Minerals Engineering 74:41-50
More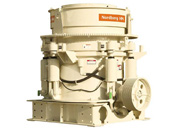
IG PERFORMANCE PARTS Mill Liners for Ball Mills Increase grinding
Mill Liners . for Ball Mills. Increase grinding efficiency and productivity. 3. Mill liners that increase . ... The feed materials for both coal and raw meals typically contain significant amounts of moisture, ... mm in cement mills and balls of up to 100 mm in dry-process raw mills. (100mm ball size is used only for correction, 90mm ball size is
More
Ball milling: a green technology for the preparation
The use of ball milling as a defibrillation method after a series of pre-treatments of raw materials was also described by the group of Elkoun, who reported the extraction of CNFs and CNCs from carrot pulp by ball
More
Ball Mill - an overview ScienceDirect Topics
For more than 50 years vertical mills have been the mill of choice for grinding raw materials into raw meal. More recently they have become widely used for cement production. They have lower specific energy consumption than ball mills and the separator, as in raw mills, is integral with the mill body.
More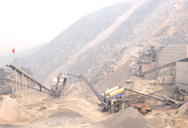
Raw Mill – Raw Mill In Cement Plant AGICO Cement Raw Mill
Raw meal grinding is a vital link in the cement raw material preparation process. After the cement raw material is crushed, it will be sent into the raw mill for further grinding until a certain degree of fineness is reached, and then enter the clinker calcination process. From the production experience of many cement plants, the selection of ...
More
Optimization of a fully air-swept dry grinding cement raw meal ball ...
Optimization of a fully air-swept dry grinding cement raw meal ball mill closed circuit capacity with the aid of simulation @article{Gen2015OptimizationOA, title={Optimization of a fully air-swept dry grinding cement raw meal ball mill closed circuit capacity with the aid of simulation}, author={{\"O}m{\"u}rden Genç}, journal={Minerals Engineering}, year={2015},
More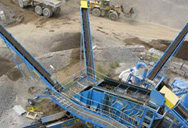
Energy and cement quality optimization of a cement grinding circuit ...
2018.7.1 Comminution in cement manufacturing takes place in both raw meal and finish grinding operations and responsible for about 60% of the whole electrical energy utilization [2], [3], ... Modeling and simulation of a fully air swept ball mill in a raw material grinding circuit. Powder Technol., 150 (2005), pp. 145-154.
More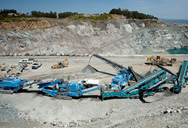
OPTIMIZING THE CONTROL SYSTEM OF CEMENT MILLING:
the grinding process remains a challenging issue, due to the elevated degree of uncertainties, process non-linearity and frequent change of the set points and the respective model parameters during operation. For productivity and quality reasons, grinding is mostly performed in closed circuits: The ball cement mill (CM) is fed with raw materials.
More
Optimizing Raw Mills Performance ; the Materials WAY
2019.6.22 Mill output and power consumption not only depends upon the input materials but also on the desired fineness (200 / 90 Micron) of the raw meal produced; hence a careful evaluation and target ...
More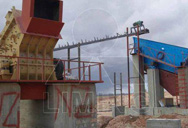
Fives Grinding in ball mills with FCB B-mill - Fives Group
The FCB B-mill is particularly well adapted to grinding products at high fineness, as well as very abrasive products and solid fuels. Featuring customized design, steady operation, and pioneering shoe-bearing technology, the ball mill is ideal for a wide range of applications, including: Cement raw meal. Cement (clinker and additives)
More
Operational parameters affecting the vertical roller mill
2017.4.1 Vertical roller mills (VRM) have found applications mostly in cement grinding operations where they were used in raw meal and finish grinding stages and in power plants for coal grinding. The mill combines crushing, grinding, classification and if necessary drying operations in one unit and enables to decrease number of equipment in
More