
Control oriented modeling of flow and size distribution in cone
2014.2.1 Thomas Gustafsson Add to Mendeley doi/10.1016/j.mineng.2013.10.031 Get rights and content • Dynamic model for
More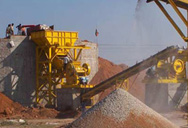
Jaw Crusher - an overview ScienceDirect Topics
Jaw crusher: The material is crushed between a fixed jaw and a mobile jaw. The feed is subjected to repeated pressure as it passes downwards and is progressively reduced in
More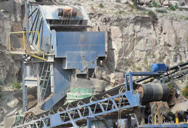
Modelling energy and size distribution in cone crushers
2019.8.1 This paper presents a model for predicting particle size distribution and energy consumption. The particle size distribution model is derived using a first-order
More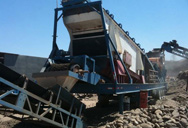
Particle size distributions for jaw crusher products of
In this research, the particles size distribution (PSD) are investigated of the jaw and cone crusher's products, while they both setting size were same. Two methods of fractal geometry and Rosin ...
More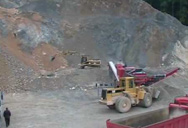
Control oriented modeling of flow and size distribution in cone
2014.2.1 This work presents a dynamic model for prediction of flow and output size distribution of cone crushers. The main purpose of the model is for simulation of
More
Fractal dimension of crushing products: effects of feed size ...
2021.8.9 The obtained fractal dimensions of the particle size distributions for the particles crushed by the jaw, cone, and roll crushers were in the range of (2.16–2.38),
More
Fractal evaluation of particle size distributions of chromites in ...
2009.1.1 The D F values obtained from experimental comminution results of this study give fractal dimensions between D F = 2.26–2.34 (jaw crusher), D F = 2.18–2.29
More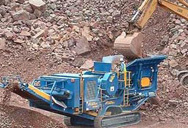
Fractal dimension of crushing products: effects of feed size ...
2020.12.21 The obtained fractal dimensions of the particle size distributions for the particles crushed by the jaw, cone, and roll crushers were in the range of (2.16–2.38),
More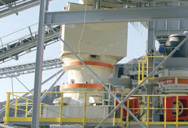
A performance model for impact crushers - ScienceDirect
2002.10.1 A schematic representation of the size-distribution model developed for cone and jaw crushers by Whiten (1972) and later improved by Whiten and White (1979) is shown in Fig. 1. The particles are characterized by their size distribution, which is represented in a discrete form by the vectors f (feed) and p (product) respectively.
More
Improved flow- and pressure model for cone crushers
2004.11.1 To determine the size distribution and bulk density above the choke level, ... The blasted rock is hauled to a primary crusher, usually a jaw- or gyratory crusher. ... 2010). Cone crushers utilize compressive mechanism and are the most commonly crusher type used in minerals processing circuits for secondary and tertiary crushing ...
More
Liner wear in jaw crushers Semantic Scholar
Semantic Scholar extracted view of "Liner wear in jaw crushers" by M. Lindqvist et al. ... A generic model to explore the relationship between the parameters of cone crusher and liner wear is provided in this paper. ... Prediction of Size Distributions from Compressing Crusher Machines. C. Evertsson. Engineering, Materials Science. 1995; 11. Save.
More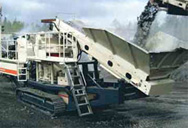
Crusher - an overview ScienceDirect Topics
Mechanical Crushing and Grinding. Oleg D. Neikov, in Handbook of Non-Ferrous Metal Powders, 2009 Crushers. Crushers are widely used as a primary stage to produce the particulate product finer than about 50–100 mm in size. They are classified as jaw, gyratory and cone crushers based on compression, cutter mill based on shear and hammer
More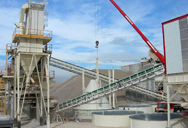
Evaluation of blast fragmentation effects on jaw crusher
2021.9.21 The main objective of this study was to determine relationships between the K07 jaw crusher’s running performance and P 20, P 50, P 80, and top size values of feed particle size distribution. After the muckpile is loaded into the trucks and transported to the crusher, the particle size distribution of the feed rock in the truckloads is
More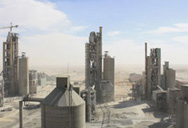
A fundamental model of an industrial-scale jaw crusher
2017.5.1 Abstract. In this study, an analytical perspective is used to develop a fundamental model of a jaw crusher. Previously, jaw crushers were modelled in regard to certain aspects, for example, energy consumption (Legendre and Zevenhoven, 2014) or kinematics (Oduori et al., 2015). Approaches to date have been mainly property specific.
More
Investigating the effects of feeding properties on rock breakage by jaw ...
2021.5.1 As for the fundamental rock comminution issues on jaw and cone crushers, Tavares and Da Silveria [21] reported that cone crusher capacity increases with decreasing the abrasion resistance of rocks. Refahi et al. [22] found remarkable relationships between shape parameters of the feed and production yield.
More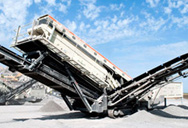
اب یطيشخم ي یکف یاَهکضگىس تلاًصحم تاسر ...
Comparison of particle size distribution of jaw and cone crusher's ... the fractal dimensions of the products of jaw and cone crushers are obtained between (2.18 to 2.27) and (2.23 to 2.29), ...
More
Fractal dimension of crushing products: effects of feed size ...
2021.8.9 The settings of both crushers were adjusted so that all the particles coming out of them have size less than 19 mm. Based on the results, the fractal dimensions of the products of jaw and cone ...
More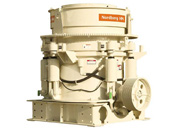
A review of modeling and control strategies for cone crushers
2021.8.15 The minimum distance between the mantle and concave is defined as the closed side setting (CSS) of the cone crusher. The CSS is easily changed online in a large variety of commercial crushers; different principles of CSS adjustment are described in (Quist, 2017).The maximum distance between the mantle and concave, on the other
More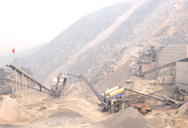
Effect of Feed Rock Size Distribution on Crusher
2015.10.22 The effect of the undersize in the feed upon the capacity of the crusher depends upon several factors. If the crusher is a primary breaker, and the discharge opening is large, undersize will usually sift
More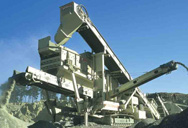
Stone Crushers: A Technical Review on Significant Part of
2022.5.14 The parameters like displacement, power draw, product size distribution, amplitude and throughput capacity for analyzing and optimizing the performance parameter of cone crusher and by varying a drive speed for different selected parameters we can simulate the performance result .
More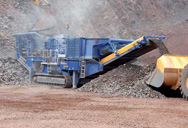
McLanahan How To Size A Jaw Crusher
2023.6.23 A Jaw Crusher is sized so that the maximum feed size is 80% of the gape and width openings. The gape is the measurement between the two jaw dies, while the width is the measurement between the two side plates. For example, if the maximum feed size is 29”x49”, the crusher gape would be 32” and the width would be 54”.
More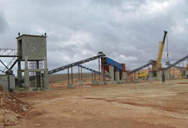
Understanding Comminution: Compression versus impact crushing
2020.9.16 Jaw crushers are generally considered a primary or first-stage crusher. The maximum feed size can be as large as 80–85% of the crusher’s gape or depth, while reduction ratios range from 2–3 times. Cone crushers are typically used in the secondary or tertiary stage after a jaw crusher has begun the reduction process earlier in the circuit.
More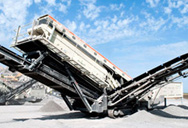
اب یطيشخم ي یکف یاَهکضگىس تلاًصحم تاسر ...
Comparison of particle size distribution of jaw and cone crusher's ... the fractal dimensions of the products of jaw and cone crushers are obtained between (2.18 to 2.27) and (2.23 to 2.29), ...
More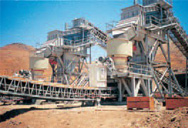
Prediction of worn geometry in cone crushers - ScienceDirect
2003.12.1 Previous investigations on cone crusher performance have been carried out by Evertsson (2000), who developed a method to model flow of rock material and the breakage. Evertsson and Lindqvist (2002) has also done some investigations on the pressure distribution and power draw in cone crushers. An alternative method for wear
More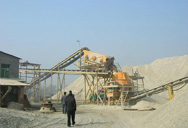
Development of wear model for cone crushers - ScienceDirect
2006.8.30 Silica sand of different size classes between 0.725 and 2.03 mm was used. The crushing load was varied. The results show a strong relationship between particle size and wear rate. The wear rate increases as particle size increases. Not only mean particle size, but also size distribution width also has an influence on wear rate.
More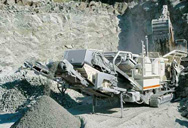
14 Size ranges applicable to Von Rittenger, Kick, and Bond
Crushability tests were carried out using a laboratory-scale cone crusher for different feeding size fractions, namely + 11.20 − 16.00 mm (size I), + 9.52 − 16.00 mm (size II), and + 6.30 − ...
More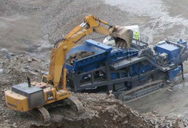
Measured (symbols) and predicted (curves) product size distributions ...
Jaw crushers reduce rock sizes between a fixed and moving jaw while cone crusher crush the rock between an external fixed element (bowl liner) and an internal moving element (mantle) [9,10].
More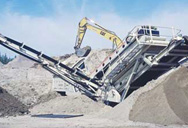
Liner wear in jaw crushers - ScienceDirect
2003.1.1 Jaw and cone crushers are commonly used in the mining and aggregates industry. Today, it is possible to predict the performance of a cone crusher, provided the geometry, crusher settings and the characteristics of the material fed into the crusher are known (Evertsson, 2000). The geometry of the crusher will change because of wear.
More