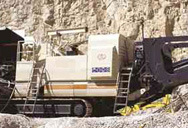
Nano Grinding Mills Methods — When Smallest is Best
Ball mills, dry and wet media mills, and jet mills can all be used to reduce particles down into the nano range. What are some of the advantages of particles measured in nanometers — and what’s the best way to achieve
More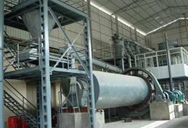
Grinding to nano-sizes: Effect of media size and slurry viscosity
2015.4.1 Grinding to nano-sizes: Effect of media size and slurry viscosity Michael H. Moys 1 Add to Mendeley doi/10.1016/j.mineng.2014.11.018 Get rights and
More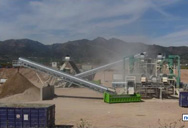
Silicon Powder Properties Produced in a Planetary Ball Mill as a ...
2020.1.15 In this study a metallurgical grade silicon quality was milled in a planetary ball mill and the properties of the powder were investigated as a function of grinding
More
Grinding to nano-sizes: Effect of media size and slurry viscosity
tive the production of particles in the nano-size range. They have used a planetary mill for this purpose and have found an apparent grind limit at a d50 of 100 nm. Media size is an...
More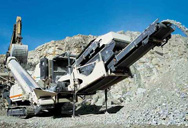
Grinding to nano-sizes: Effect of media size and slurry viscosity
2015.4.1 Ball wet/dry media and jet mills are often used to reduce large particles to nanosize range 1-100 nm (Cho et al. 2009). Wet or dry milling methods would be used to
More
BALL MILLS FROM NANO GRINDING TO
2019.12.11 The variety of grinding modes, usable volumes and available grinding tool materials makes these mills perfectly suited for a vast range of applications – from producing nanosized particles to...
More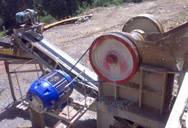
Grinding to nano-sizes: Effect of media size and slurry viscosity
2015.4.1 A 1.5 MW Kelsey mill is in operation and larger mills are contemplated. It should be possible to exploit this approach for nano-milling. Work done at Tata
More
The design and optimization process of ball mill to reduce particle ...
2020.11.16 Small particle size in the order of micrometer of event nanometer size is preferred. The raw materials were ground from the big particle size to the smallest
More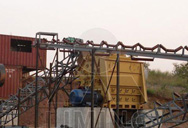
The Impact of Ball Milling Process Parameters on the Preparation
Then this paper studied the impact of different ball milling technical parameters on the grain size of nano silicon powder, so as to work out the fitting function model and the optimal
More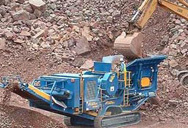
Planetary Ball Mills for Nano-scale Grinding - 2011 - Wiley
2011.5.6 A suitable tool for this method is a planetary ball mill, such as Retsch's PM 100, PM 200 or PM 400, which provides the necessary energy input. The common rules
More
Ball milling as a synthesis method - Aalto University Wiki
2022.4.4 Ball mills can be classified into high-energy ball mills and low-energy ball mills by their rotation speed. Selection of certain ball mill depends on used technique; MA, MM or MD. However, some ball mills can be utilized for all three of these techniques. Table 2 presents the most common ball mills and their energy types. [1, p.26] [4] Table 2.
More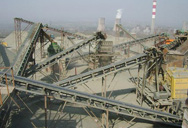
Mixer Mill MM 500 nano - for ultrafine grinding
The mixer mill MM 500 nano is a compact, versatile bench-top unit which has been developed specially for dry, wet and cryogenic grinding of up to 2 x 45 ml sample material within seconds. With a maximum frequency of
More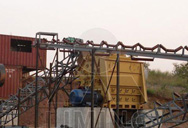
The Impact of Ball Milling Process Parameters on the Preparation
The experimental results showed that when the ratio of grinding media to material is 20: 1, without considering the influence of other factors such as temperature and humidity, when the agitator shaft speed is 1100/1200 rpm and the milling time is 150 min, the smallest grain size of nano silicon powder could be obtained, and the fitting formula of the agitator shaft
More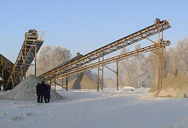
A green protocol ball milling synthesis of dihydropyrano [2,3-
2023.3.4 Ball mill is an effective, ... The morphological properties and size of Nano-SiO 2 /AEP nano-catalysts were investigated by FESEM and the results are compiled in Fig. ... from neat and liquid-assisted grinding to polymer-assisted grinding. Angew Chem. 2015;127:7479–83.
More
How can I decrease the particle size from Micro to Nano scale?
I have mineral wollastonite within average particle size of D50 = 3 micrometer, I am trying to decrease the particle size to nano scale, using a planetary ball milling, I hope I can understand the ...
More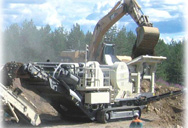
Ball mill - Wikipedia
A ball mill, a type of grinder, is a cylindrical device used in grinding (or mixing) materials like ores, chemicals, ceramic raw materials and paints. Ball mills rotate around a horizontal axis, partially filled with the material to be ground plus the grinding medium. Different materials are used as media, including ceramic balls, flint pebbles ...
More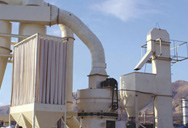
Effect of Slurry Concentration on the Ceramic Ball Grinding
2022.12.6 Nano ceramic balls have been widely used in stirred mills as an emerging ... In general a is only related to the fragmentation characteristics of the mineral itself and not to the ball mill size and grinding conditions. However, the values of parameter a for −0.500 + 0.300 mm, −0.300 + 0.150 mm, and −0.150 + 0.075 mm in ...
More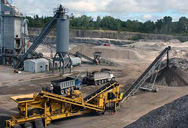
Ball Milling - an overview ScienceDirect Topics
To initiate the size reduction process, bulk samples of the NPs are transferred to a container containing heavy balls that assist in size reduction by continuous grinding. Reduction of particle size can be accomplished using numerous types of ball milling techniques such as high energy mills, planetary ball mills, attrition ball mills, low energy tumbling mills,
More
(PDF) DESIGN AND FABRICATION OF MINI BALL MILL.
2016.3.25 milling time depends on the type of mill, size of the grinding medium, temperature of milling, ball- to-powder ratio, etc.[23] [24] An increase in the number of balls had a minimal impact on the
More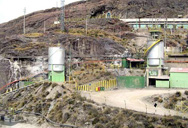
OPTIMIZATION OF MILLING PARAMETERS OF PLANETARY BALL MILL
The ball mills can be classified into two categories according to the axis of rotation of the bowl. 1. Vertical axis and 2. Horizontal axis. Figure 1 Direction of rotations of drums in (a) Vertical and (b) Horizontal axis ball mills In Vertical axis ball mill, the drum with material to be ground and grinding balls rotates about
More
HIGH ENERGY BALL MILLS
pulverized in the most powerful planetary ball mill and in the Emax (50 ml grinding jar of zircomium oxide, 110 g matching grinding balls 0.1 mm Ø, 10 g sample, 15 ml 1% sodium phosphate). After 30 minutes the d 90 value of the Emax sample was 87 nm. The planetary ball mill achieved a grind size of only 476 nm after this time (excl. cooling ...
More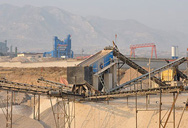
Grinding to nano-sizes: Effect of media size and slurry viscosity
2015.4.1 Ball wet/dry media and jet mills are often used to reduce large particles to nanosize range 1-100 nm (Cho et al. 2009). Wet or dry milling methods would be used to make nanoparticles, and each ...
More
BALL MILLS FROM NANO GRINDING TO
2019.12.11 Ball mills are among the most variable and effective tools when it comes to size reduction of hard, brittle or fibrous materials. The variety of grinding modes, usable volumes and available ...
More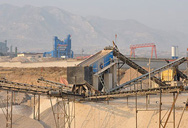
Rapid development of API nano-formulations from ... - ScienceDirect
2019.6.30 Related to the increasing grinding energy gained by typical scale-up trials using the laboratory mill DeltaVita 300 (DV300, max. 1.5 kg), pilot-scale production using the DeltaVita 600 (max. 3 kg) as well as manufacturing of the API-particles in the production scale using a DeltaVita 10,000 (max. 50 kg), the SGE could be a parameter for the
More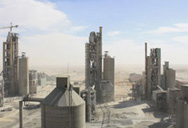
Nanomaterials Free Full-Text High-Energy Ball Milling for High ...
2022.9.19 The current production method of nanobiochar (NBC), an emerging, environmentally friendly nanocarbon material, is tedious and lengthy. Therefore, in this study we aimed to improve the productivity of NBC via high-energy ball milling by manipulating the grinding media and processing time. The particle size distribution of the resulting NBC
More
Mechanical Milling: A Superior Nanotechnological Tool for Fabrication ...
2021.9.24 At the turn of the century, several ball mill manufacturers started to produce cryo-ball mills, which grind the desired materials under a flow of liquid nitrogen. It is designed specifically for cryogenic grinding and crushing of tough or temperature-sensitive materials cooled to −196 °C.
More
Grinding to nano-sizes: Effect of media size and slurry viscosity
30 nm which is well within the so-called nano-size range (i.e. typ- ically regarded as particle size less than 100 nm). An exciting recent development is the Kelsey mill which uses
More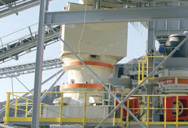
(PDF) Optimization of ball milling parameters to produce
2013.11.1 However, after the use of ball-mill grinding in medicinal plant extraction, Centella asiatica was extracted and the result showed an 82.1% increase in the yield of the bioactive ingredient ...
More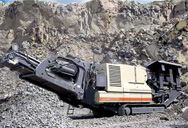
Comminution of mineral fertilizers down to nanoparticles
Ball Mills - (Planetary Mills) Laboratory Mills Milling tests with the FRITSCH Planetary Ball Mills . Comminution of mineral fertilizers down to nanoparticles . Introduction Nanotechnology widely deals with nanoscale particle between 1-100 nm. 1. Alternative definition of nano fertilizer (larger particle size): fertilizer which particle size is ...
More