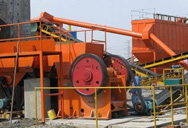
Optimization of FeO in iron ore pellet with varying blend of
2015.10.24 It was observed that FeO content decreases from 1.2 % to 0.5 % with decreasing Carbon content from to 0.75 % to 0.35 % and temperature from 12800 C to 12400 C in the pellet mix, thereby enhancing...
More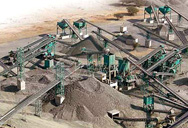
Iron ore - Wikipedia
Iron ores are rocks and minerals from which metallic iron can be economically extracted. The ores are usually rich in iron oxides and vary in color from dark grey, bright yellow, or deep purple to rusty red. The iron is usually found in the form of magnetite (Fe 3O 4, 72.4% Fe), hematite (Fe 2O 3, 69.9% Fe), goethite (FeO(OH), 62.9% Fe), limonite (FeO(OH)n(H2O), 55% Fe) or siderite (FeCO3, 48.2% Fe).
More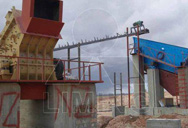
Influence of Iron Ore Characteristics on FeO Formation
2011.5.1 The results indicate that LOI (loss on ignition) in iron ores have a positive influence on FeO formation by promoting the sintering process of Fe 2 O 3 decomposing
More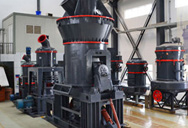
(PDF) Analysis of the factors affecting the iron ore pellet FEO index ...
2020.12.15 This study aims to predict factors affecting the FeO (Iron Oxide) of iron pellets and find out the contribution of each factor to reduce the pellets FeO (the ideal
More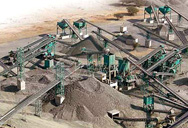
(PDF) Iron Ore Sintering: Quality Indices - ResearchGate
2017.5.2 Abstract and Figures. Sinter plants process a mixture of iron ore fines, recycled ironmaking products, slag-forming agents and
More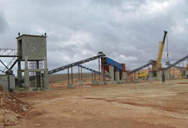
Iron oxide - Wikipedia
Iron oxides feature as ferrous ( Fe (II)) or ferric ( Fe (III)) or both. They adopt octahedral or tetrahedral coordination geometry. Only a few oxides are significant at the earth's surface, particularly wüstite, magnetite, and
More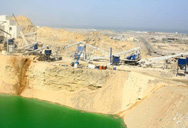
Optimisation of FeO in iron ore sinter at JSW Steel Limited
2012.4.1 FeO in iron ore sinter is directly related to its magnetite content (Umadevi et al. 2012). Sinter productivity reaches maximum values when sinter FeO values of 8.6
More
Effect of FeO-content and potentials for quality improvements of
1995.12.1 Abstract. The FeO-content strongly influences the physical and metallurgical properties of iron ore pellets. A wide range of FeO-contents within the
More
Effect of FeO concentration in sinter iron ore on reduction
2022.8.22 The reduction of wustite to iron was carried out at 1000, 900, and 800°C in a CO—CO2—H2 atmosphere for the mineral morphology-controlled sinter, and the
More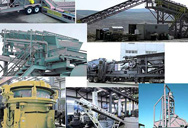
Phase transformation during roasting process and ... - ScienceDirect
2017.12.1 Oolitic-iron ore material is one of the most important iron resources in China. However, due to its low grade of Fe, poor liberation of iron minerals and high
More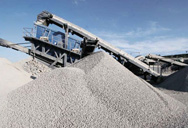
Iron Ore Agglomeration Technologies IntechOpen
2017.5.18 Until the 1950s of the last century, the oxidized iron ores that were loaded into the blast furnace had granulometries within 10 and 120 mm. However, the depletion of high-grade iron ore sources has made
More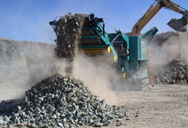
Why Is Feo Important In Iron Ore
Influence of Iron Ore Characteristics on FeO Formation. 2011-5-1 Specifically, the content of FeO generated by Australian limonite A is the highest, while mixed ore B and hematite C 18 I I 1200 12!3l 1300 1350 Temperature/v Fig. 3 Comparison of FeO contents in 5 iron-ore samples at different sintering temperatures Issue 5 Influence of Iron Ore Characteristics
More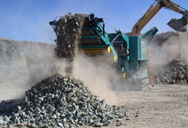
Why Is Feo Important In Iron Ore
Influence of Iron Ore Characteristics on FeO Formation. 2011-5-1 Specifically, the content of FeO generated by Australian limonite A is the highest, while mixed ore B and hematite C 18 I I 1200 12!3l 1300 1350 Temperature/v Fig. 3 Comparison of FeO contents in 5 iron-ore samples at different sintering temperatures Issue 5 Influence of Iron Ore Characteristics
More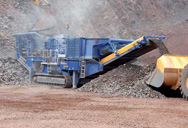
Effect of Prior Oxidation on the Reduction Behavior of Magnetite
2021.6.1 It can be noted that if the temperature is higher than 700 °C, the RD of the raw magnetite-based iron ore remains stable at 20 pct, which could be the critical RD for starting the de-fluidization.[33,34] In actual case, metallic iron can be formed before the reduction to FeO completed, indicating that even RD is smaller than 33 pct the
More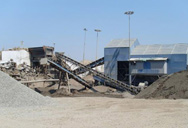
A literature study on measurement methods for calculating the FeO ...
Direct reduced iron is a product of a reduction process where iron ore is reduced by natural gas in a shaft oven. It too uses the counter-current principal where iron pellet is charged at the top of the shaft and reduced by the reduction gas [6]. The reduction gas used in this case is natural gas that has been cracked to primarily hydrogen, H 2
More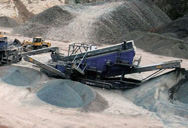
How iron ore is powering China’s infrastructure boom, and why ...
2021.2.14 China’s appetite for steel has surpassed 1 billion tonnes a year, but it is becoming increasingly expensive and difficult to source the most vital ingredient – iron ore – from abroad.
More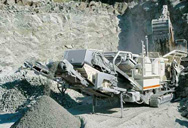
Reserves and Resources of Iron Ores of India — A Perspective
2022.5.1 India is not only one of the leading producers of iron ore but also at present second largest manufacturer of steel in the world (2021). Though the country can boast of huge good quality iron ore ...
More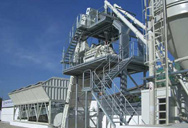
Efficient iron sintering process control - Materials Talks
2020.11.4 Efficient iron sintering process control. By Dr. Olga Narygina, Wednesday 4 November 2020. In the previous blog, we discussed the importance of minerals analysis for efficient iron ore mining and beneficiation. In this blog we will discuss the added value of mineralogy monitoring at the next step of the ore-to-metal process, iron ore sintering.
More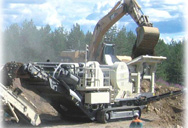
Thermal Decomposition Behaviour of Fine Iron Ore Particles - J
There are three main forms of iron oxides: hematite (Fe 2 O 3), magnetite (Fe 3 O 4) and wüstite (FeO), and their melting points are 1838 K, 1870 K and 1644 K, respectively.According to the literature, the thermal decomposition of hematite ore has been mentioned in some laboratory experiments.
More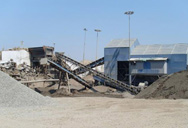
Influence of Iron Ore Characteristics on FeO Formation
2011.5.1 Abstract. The influence of iron ore characteristics on FeO formation during sintering was examined mainly in terms of chemical composition and the melting characteristics of iron ores. Statistical regression and X-ray diffraction were used to further explain the specific effect of iron ore characteristics on FeO formation.
More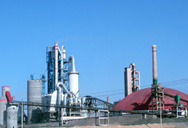
Iron Ore The Canadian Encyclopedia
2006.2.7 Iron ore usually consists of iron oxides and carbonates. Its most important mineral forms are magnetite (Fe 3 O 4 , 72.4% Fe), hematite (Fe 2 O 3 , 69.9% Fe) and siderite (FeCO 3 , 48.29% Fe). In Brazil, some ore that contains practically no other minerals can grade as high as 68% Fe, but the crude ore mined in Canada grades between 30
More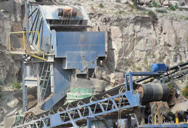
Sinter Quality and Process of Sintering Iron Ores – IspatGuru
2014.11.21 The ore particle size plays an important role. The assimilation ability of fine ores is greater than that of coarse particles. The reaction surface area of iron ore fines is high which results into higher reaction rates. But, the formation of higher concentrations of melt result into decrease in the melt fluidity.
More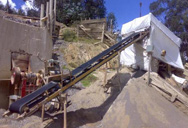
Analysis of the factors affecting the iron ore pellet FEO index
Analysis of the factors affecting the iron ore pellet FEO ... one of the most important of them is the amount of FeO. To analyze the raw data, data mining techniques can be used.
More
(PDF) Thermodynamic Analysis of Iron Ore Sintering
2020.11.16 Abstract and Figures. The sinter process of iron ore with biomass carbon instead of coke breeze as fuel was investigated via thermodynamic analysis in this paper through a comparison of sinter ...
More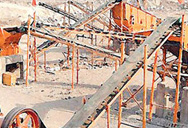
Effect of Iron Ore Pellet Size on Metallurgical Properties - MDPI
2022.2.10 Iron ore pellets are small and hard spherical particles agglomerated from a fine iron ore concentrate. They are used in the blast furnace process to produce hot metal. The diameter of blast furnace pellets is usually between 8 and 16 mm. In this study, a batch of magnesia iron ore pellets was first sieved into particle sizes of 8–10 mm, 10–12.7
More
A Review of Ore Smelting in High Carbon Ferromanganese Production
2019.7.15 This paper provides a comprehensive current review of our fundamental understanding of manganese ore smelting. Process parameters and resultant cost effects are discussed in terms of existing ...
More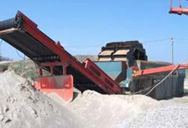
Mechanisms in oxidation and sintering of magnetite iron ore
2008.4.9 Thermal volume changes and oxidation mechanisms in magnetite iron ore green pellets balled with 0.5% bentonite binder, as a function of raw material fineness and pellet porosity, are shown. When a pellet starts to oxidize, a shell of hematite is formed around the pellet while the core still is magnetite. Dilatation curves were measured under
More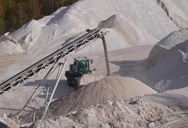
Effect of Amount of Carbon on the Reduction Efficiency of Iron Ore
2016.4.8 The effect of carbon-to-hematite molar ratio has been studied on the reduction efficiency of iron ore-coal composite pellet reduced at 1523 K (1250 °C) for 20 minutes in a laboratory scale multi-layer bed rotary hearth furnace (RHF). Reduced pellets have been characterized through weight loss measurement, estimation of porosity,
More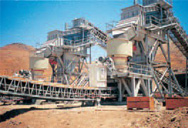
Chromite ore beneficiation: prospects and challenges
2023.1.1 These ores are hard and of high quality (average 50%–52% Cr 2 O 3). In Cuba, important refractory ores carrying 33%–43% Cr 2 O 3 are found in Camaguey, Oriente, and Matanzas. There are also huge tonnages of low-grade chromiferrous nickel-iron ores in Mayari and Mao Bay. Small deposits of high-quality ore occur in the Mysore
More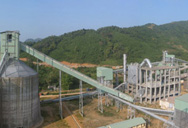
(PDF) Analysis of the factors affecting the iron ore pellet FEO
2020.12.15 One of the most critical factors affecting iron pellet quality is the reduction in FeO (Iron Oxide) index in the final product. This study aims to predict factors affecting the FeO (Iron Oxide) of ...
More